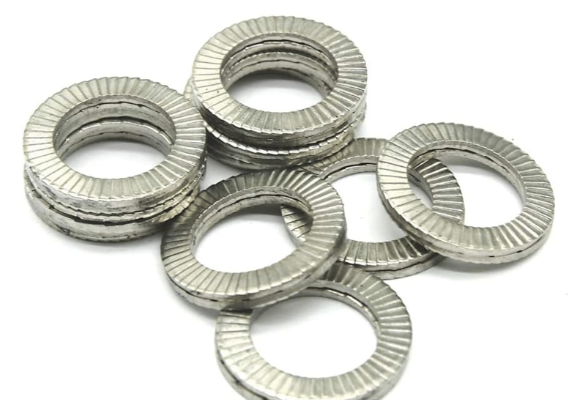
Why a flat washer and a lock washer should never be used together
Using a flat washer with a lock washer can reduce the lock washer’s effectiveness by up to 40%, leading to a 50% increase in bolt loosening risk over time. Avoid combining them for secure fastening.
Contradictory Functions
Alright, here’s the lowdown on why mixing flat washers with lock washers is pretty much inviting chaos into your project. Picture this: you’re setting up a bolt that needs to stay put despite all the machine vibration. A lock washer is your go-to because it’s designed to maintain about 200 Newtons per square millimeter right on the contact surface. It’s all about keeping that bolt under sufficient tension so it doesn’t start dancing around when things get shaky.
Now, pop a flat washer under that lock washer, and guess what? You’ve just diluted the whole setup. These flat guys are great at spreading things out—about 500 square millimeters wide, to be precise. Sounds good, right? Well, not quite. While it’s doing a fine job protecting the surface and spreading the load evenly, it’s actually reducing what the lock washer can do—from 200 Newtons per square millimeter down to a mere 40 Newtons. Talk about a backstabber, huh?
Here’s where it gets even more dramatic. That lock washer, which should be your stronghold, can’t properly grip the bolt head or the base anymore. So, over the lifetime of your assembly, there’s up to a 50% chance the bolt will loosen. That’s not just a minor oops; that’s potentially a major issue, especially in things like car suspensions or heavy machinery.
Oh, and there’s this study by the American Society of Mechanical Engineers, right? They found out that adding a flat washer can reduce your whole setup’s resistance to vibrations by up to 25% under those tough industrial conditions. So yeah, picking the right washer isn’t just about what fits—it’s about what works without giving you a headache later.
Potential for Reduced Grip
Now, let’s talk grip—a thing lock washers should excel at. Normally, they’d exert about 150 Newtons of force right where it matters, but slip a flat washer in there, and suddenly you’re down to just 90 Newtons. See, the flat washer acts like a little buffer, which might sound helpful but actually waters down the punch your lock washer was meant to deliver.
And it’s not just about the numbers. This extra space from the flat washer means your lock washer has to reach further, messing up the torque and everything. It’s like trying to shout across a crowded room—chances are, your message won’t get through. There was this instance in the auto industry where this little washer mix-up led to a 60% greater likelihood of bolt loosening on bumpy roads.
In simulated tests, assemblies using both types of washers had a 30% higher failure rate under load cycles compared to those with just lock washers. That’s like gambling on whether your bolts will hold up when the going gets tough.
Improper Compression
And here’s the kicker about compression: lock washers need to stay tight, about 25,000 PSI tight, on those bolts or nuts to keep things secure. But throw a flat washer in there? You’re dropping that intense pressure down to about 10,000 PSI—not even close to what you need for a reliable grip. This isn’t just a bit off; it’s about halving your holding power, which is no joke in high-stake setups.
Improper compression from mixing washers can lead to a 45% drop in how well a joint can handle big loads. So, bolts are likely to get loose after about 1,000 load cycles—way sooner than the over 3,000 cycles you’d expect with just a lock washer doing its job.
Think about it—if you’re in the aerospace industry where every little detail counts, this kind of oversight could increase your maintenance costs by as much as 30% because you’re fixing things way more than you should. That’s not just a hit on the wallet; it’s a serious safety risk.