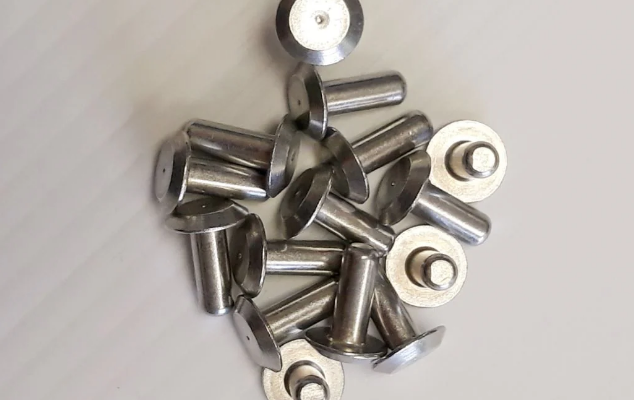
What should the shop head of a rivet be
The shop head of a rivet should be 1.5 times the rivet’s diameter in width and 0.5 times the diameter in height. For example, a 1/4-inch (6.35 mm) rivet requires a 9.53 mm wide and 3.18 mm high shop head for proper fastening.
Diameter
In the fabrication of metals, one of the general sizes of rivets used is 3/16 inch. For such a type of rivet size, the shop head diameter recommended should be 1.5 times the diameter of the shank; hence, the diameter of the shop head is 7.14 mm. Such a reduction in diameter from 7.14 to 5 mm could easily lead to a loosening of the fastening.
In structural steel beam fastenings related to civil and construction projects, rivets as large as 1/2-inch diameter (12.7 mm) are often within engineers’ capability options. In this case, the shop head diameter should be 19.05 mm or about 3/4 inch. If a shop head were manufactured to be too small, only 14 mm, it would not spread the force properly across the materials joined and, would allow the joint to fail under heavier loads. By keeping this ratio at 1.5 times the shank diameter, engineers can ensure longevity and strength for steel frameworks.
Lighter applications of rivets are in aluminum paneling for building facades, so 1/8 inch (3.18 mm) rivets or smaller are common. The shop head for such rivets should have a diameter of 4.77 mm for adequate clamp without undue stress to the lightweight material. For this, if the diameter is not correctly sized to make the shop head only 4 mm, that could result in warping or loosening of the aluminum over time.
Rivets are also very critical in aircraft manufacturing due to the need for precision and safety; these can have diameters such as 5/32 inch or approximately 4 mm. For this reason, the diameter of such rivets’ shop head should be 6 mm so that it may take the forces of flight to an extreme limit. A shop head as large as, say 7 mm, may create undue stresses in the surrounding material, which may lead to material cracks or weaknesses.
For manufacturing heavy-duty equipment, rivets that assemble major machinery could be 3 / 4 inch diameter, 19 mm. In this size, the diameter of a shop head needs to be 28.5 mm in order to support the thick plates of metal it will hold together. Deviation from such a specification, the use of a 25-mm shop head will not provide the rivet with sufficient holding force for parts that are subjected to much force, under conditions of continuous vibration that could lead to higher maintenance costs and even hazard to personnel safety.
Height
Another very critical factor in ensuring the strength and durability of the fastening is the height of the shop head of the rivet. Considering a 1/4 inch (6.35 mm) diameter rivet, the recommended shop head height is usually to be 0.5 times the diameter of the rivet shank; thus, it is 3.18 mm in height. With a more minimal shop head height, say 2 mm, there would not be enough material deformed during installation that could result in a weak joint that may work loose through service, especially where vibration is concerned in machinery or vehicles.
In aerospace applications where precision is vital, a 3/16-inch diameter shank rivet, requires a 2.38 mm shop head height. With a height of only 2 mm, the rivet may not be able to get sufficient clamp with the material, considering the high-pressure environments in flight. The shop head may be too tall, about 3 mm, over-stressing the material around it and probably eventually causing cracks or fatigue in the riveted joints.
Rivets of 1/2-inch diameter shank are normally used in such marine applications where the occurrence of corrosion and environmental stresses is always a big concern. These rivets must possess a shop head height of 6.35 mm. The use of too small of a shop head height, say 4 mm, might not create sufficient deformation to ensure that a watertight seal has occurred; the result could be potential leaks with attendant long-term corrosion. A height of 7 mm might apply too much pressure on softer materials aluminum or composite materials used in boat construction, therefore compromising its structural integrity.
For automotive assembly, rivets with a 5/32-inch (4 mm) shank require a shop head height of 2 mm. With too low of a height, such as 1.5 mm, the rivet would not be able to expand enough to hold down body panels securely, which means loose joints and probably some rattling. If this height is too great, such as 3 mm, there may be excessive stress concentrations in the joint that could deform the material surrounding the rivet over time-especially with the constant road vibration that vehicles face.
For the construction of bridges, where much heavy load and long-term durability are a must, rivets having a 3/4 inch shank should be manufactured in such a way that their shop head height is no less than 9.5 mm. A height of 6 mm could be totally insufficient to cope with the forces that a bridge goes through, like the load of traffic and other stresses caused by environmental factors which might lead to the failure of joints. Increasing the height more than the recommended value, say up to 10 mm, would be adding unnecessary weight and pressure within the riveted area, that could develop fatigue cracking in the steel plates after some time, increasing costs on maintenance, with a decreased life span of the structure.
Load Distribution
Taking the case of structural steel applications where rivets are applied in joining beams and columns, a 1/2-inch diameter requires a shop head diameter of about 19.05 mm to achieve appropriate dispersion and distribution of the load across the joint. This would make the force not in uniform distribution but concentrated around the shop head, causing stress concentrations that, in time, may result in joint failure, especially under heavy-traffic volumes or environmental stress due to wind and vibrations.
Appropriate load distribution shall be ensured in such demanding aerospace applications, where weight and, at the same time, resistance is crucial to avoid structural fatigue. The rivet diameter is 5/32-inch, and the shop head must be as large as 6 mm in diameter to distribute flight loads-air pressure of several thousand pounds per square inch-uniformally. Smaller shop heads, perhaps only 5 mm, would lead to localized points of stress that could easily cause material cracks or failure of the riveted joints under the extreme conditions of flight.
The uses for marine construction include rivets encountering a situation of load distribution across materials that are often subjected to corrosion and environmental stresses, such as waves and saltwater exposure in shipbuilding, including offshore platforms. A 3/4-inch (19 mm) rivet with a shop head diameter of 28.5 mm spreads the load at the joint, while a shop head of 25 mm could create a focal point for corrosion.
Riveted automotive manufacturing requires that body panels and structural members be joined with the load carefully designed to prevent rattling and provide a secure interference fit. Typical applications call for 1/8-inch (3.18 mm) rivet head diameter in shop head form of 4.77 mm. And if the shop head is only 4 mm, then such uneven load distribution may cause the panels to loosen up due to continuous road vibrations and would present structural weaknesses and increased noise over time, necessitating frequent adjustments or replacements.
In the construction of bridges, rivets are used in joining huge steel beams supporting heavy loads, such as those coming from traffic and environmental forces, which include wind and temperature changes. With a view to distributing the applied load uniformly across the steel plates, a 3/4-inch rivet requires a shop head diameter of 28.5 mm. If this shop head is small, say 26 mm, it may develop stress concentrations and promote cracking; under the weight of traffic, a joint may fail.