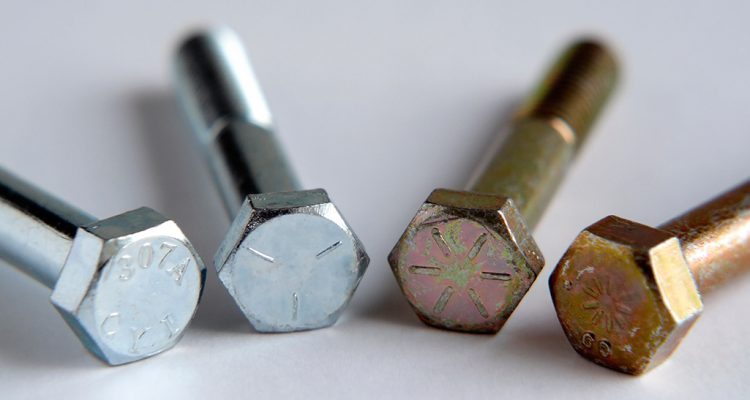
What is the yield strength of SAE Grade 5 bolts
Table of Contents
ToggleWhat is SAE Grade 5?
SAE Grade 5 bolts are one of the most widely used fasteners that are made from medium carbon steel. They should have a combination of good strength and excellent ductility. These bolts receive a heat treatment that gives them a minimum tensile strength of 120,000 psi. Due to this, it also finds great applications in automobile assembly, machinery, construction, among others. For instance, in heavy machinery assembly, Grade 5 bolts ensure that the parts under extremely heavy load conditions stay well bolted.
By yield strength, SAE Grade 5 bolts usually possess 105,000 psi. This level of strength means that they can handle a substantial amount of stress before permanently deforming. For any practical application, this could be crucial—for example when one is securing a heavily loaded load, then, one should know that such bolts will not fail out due to the applied force. Considering that the strength of SAE Grade 8 bolts is around about 130,000 psi, one will see how acceptable Grade 5 bolts become for applications that are of lesser strength but so sturdy.
Material composition is mainly carbon steel in SAE Grade 5 bolts, which strengthens and generally improves performance. Typically, the carbon content is between 0.25% and 0.55%, which raises the hardness and subsequently the wear characteristics. Alloying elements, such as manganese, can be added to further improve toughness and strength. As will be explained later, such bolts have a peculiar strength that is highly crucial, for example, when applied to vehicle chassis or structural building components in ensuring the entirety of the structure supports different forces and loads for a considerable period of time.
Knowing the appropriate torque specifications for SAE Grade 5 bolts is important for their effective application. Torque for a ½-inch Grade 5 bolt varies from 75 to 90 foot-pounds. This is dependent on the exact application and the materials to be fastened. The right torque ensures that the bolt will hold without over-tightening, which may cause failure. For projects that require many fasteners, such as deck building or heavy-duty shelving, judicious use of Grade 5 bolts with proper torque can make a huge difference in the longevity and strength of the assembly.
Yield Strength Basics
The most critical property in material science, yield strength describes how well a material resists stress without permanent distortion. Because, in SAE Grade 5 bolts, for example, the yield strength would run about 105,000 psi, determining how much more additional amount of stress could be applied before the material starts to deform plastically. This property is vital in those applications where bolts are subjected to various loads and forces, hence keeping components in place for functionality over a period of time. For instance, in automotive applications, the yield strength helps in showing how much stress a bolt can bear without it bending or breaking, something important in maintaining structural integrity within vehicles.
Yield strength, in real situations, may affect bolt selection for certain projects. For instance, a construction engineer may use those bolts that can withstand loads due to both static as well as dynamic forces in order to build the construction for constructing a metallic building frame. If heavy roofing is placed on it, such heavy roofing can be supported because of SAE Grade 5. In cases where their yield strength is not required or if their design is not in a position to require, higher yield strength of a bolt is used, but they can withstand up to 130,000 psi, which is SAE Grade 8. This selection process underscores the importance of knowing the yield strength to ensure that the selected fasteners would have a chance to bear the anticipated loads.
In addition, yield strength is related to the general safety factors involved in engineering designs. There is usually a safety factor applied by the engineers, usually from 1.5 to 3, depending on the application. For instance, if the loading is 30,000 pounds, SAE Grade 5 bolts having a yield of 105,000 psi will safely carry this loading within the selected safety factor. For this example, the bolts can withstand load up to 210,000 pounds with a safety factor of 2 before they yield. Proper selection of yield strength does indeed make a structure highly reliable and safe.
Common Uses
With this, the versatility and strength-rich SAE Grade 5 bolts may be extensively used in all applications. The most typical uses for the same in the automobile industries are attachment parts, such as engine mounts, suspension system parts, and chassis component parts. For instance, in building the car suspension system, Grade 5 bolts can come in with stresses of over 1,000 pounds per wheel just to ensure stability and safety while the car is under use. Their tensile strength of about 120,000 psi makes it perfect for such highly stress-prone environments.
Construction very importantly uses SAE Grade 5 bolts as they serve in the construction of frameworks, bridges, and other infrastructures wherein one can never be so sure when reliability may come in handy. Thousands of such bolts are used by engineers in building a commercial building. Each bolt, with a yield strength of about 105,000 psi, supports quite a lot of weight and contributes to the overall stability of the building. As a standard, in a simple steel frame structure, for example, Grade 5 bolts are utilized when assembling pieces that would encounter lateral loads during strong winds or earthquakes; these bolts enable the building to better withstand those loads.
Equipment and machinery assembly is the other widespread application of SAE Grade 5 bolts. These are applied for assembling any form of equipment or machine from farm machines to industrial ones. For instance, Grade 5 bolts secure some critical parts of tractors and harvesters, among others used for agricultural activities. Considering the harsh environment farming machinery often operates in and significant mechanical loading they are exposed to, the strength and toughness of a Grade 5 bolt may be significant. It makes such bolts retain their integrity under dynamic loads, so field performance is ensured to be reliable, where equipment downtime can lead to significant losses.
Comparison to Other Grades
When SAE Grade 5 bolts are compared with other grades, it is better to consider mechanical properties and suitable applications. SAE Grade 5 bolts offer a tensile strength of about 120,000 psi, while the yield strength is about 105,000 psi. For higher strength applications, the SAE Grade 8 bolt offers a tensile strength of 150,000 psi and a yield strength of about 130,000 psi. The great difference in strength involved makes Grade 8 bolts more suitable for heavy-duty applications like high-stress auto and aerospace components where safety and reliability become a great concern.
Another important issue associated with these grades of bolts involves material comparisons. SAE Grade 5 bolts are commonly fabricated from medium carbon steel, which offers a good balance between strength and ductility. But SAE Grade 8 bolts are mostly made of alloy steel, heat-treated to give superior mechanical properties. These resultant material and treatment allow Grade 8 bolts to be more resistant against shear forces and impacts, ideal for machinery that constantly goes through stress and vibration. Moreover, for high-performance engines, Grade 8 bolts can avoid failures due to extreme conditions.
Costwise, SAE Grade 5 bolts are cheaper compared to Grade 8 bolts. In comparison to the manufacturing process of Grade 8, the additional heat treatment involved, along with a number of alloying elements, increases its production cost. This fact alone would make Grade 5 bolts worth considering in projects on tight budgets, such as home improvements or non-critical applications. In such instances, the choice of Grade 5 bolts could be way cheaper without losing performance that matters much. For instance, on a residential project, the contractor will be able to use Grade 5 bolts to fix wooden frames but keep the Grade 8 bolts for places that require additional strength, like load-bearing walls.
In practice, many uses will therefore rely on the needs of the project. For instance, on a construction site, although Grade 5 bolts could easily hold structural members together, Grade 8 bolts are often preferred in areas which receive higher tensile and shear forces, such as in the connections of bridges or heavy machinery. Further, Grade 2 bolts, having a tensile strength of about 60,000 psi, are usually applied to light-duty uses—another example of the range of choice dependent upon needs for strength.
Material Composition
The material makeup of SAE Grade 5 bolts is basically made up of medium carbon steel, and this forms a major part of its mechanical properties. They typically hold about 0.25% to 0.55% carbon content. This amount of carbon increases the hardness and gives additional strength to the steel so that the bolt can reach tensile strength of approximately 120,000 psi with a yield strength of approximately 105,000 psi. With its medium carbon content, it has good strength and enough ductility that it is far from brittle.
Aside from carbon, common alloying elements added in making SAE Grade 5 bolts are manganese at up to about 0.60% to 0.90%. Manganese increases the hardenability of the steel—or, in other words, its resistance against wear and fatigue. This becomes especially advantageous in applications where bolts are subjected to repeated stress cycles, such as in automotive assemblies or heavy machinery. Manganese further assists in enhancing the capability of performance at high temperatures because it stabilizes the structure and maintains strength upon heating.
Silicon is another significant constituent of SAE Grade 5 bolts, though in a little amount—usually less than 0.40%. Silicon acts as a deoxidizer for steel at manufacture and greatly improves the toughness of the resulting material. This toughness is essential for preventing disastrous failures under high stresses. For example, if these are installed in suspension systems, then the performance with regards to absorbing impacts and withstanding deformation will become vital factors that affect vehicle safety and performance.
Testing Methods
Testing methods on SAE Grade 5 bolts are meant to ensure that their mechanical properties come up to standard and expectations of the industries and various performances. To date, a tensile test is a common testing procedure that finds application on a bolt’s strength through increasing loads until they break. On this type of test, a typical minimum tensile strength of any SAE Grade 5 bolt is required to attain 120,000 psi. By practical interpretation, this means that if a bolt fails at loads lower than expected, there might be material quality or manufacturing process issues with it and hence should be taken for further investigation.
The other important testing method is the yield strength test, which is aimed at showing beyond what point a bolt has started to set in permanent deformation. This test typically encompasses loading the bolt to obtain a measure of the corresponding stress up until yielding. For a standard SAE Grade 5 bolt, the yield strength should be about 105,000 psi. If a bolt were to deform under a lower amount of load, this may raise red flags regarding potential safety risks where structural integrity is concerned. This process will guarantee that the bolts operate satisfactorily under forecasted loads in service.
Another significant quality control test for SAE Grade 5 bolts is a hardness test. Hardness is a symptom of the resistance of the material to wear and deformation. The most common methods of testing the hardness are Rockwell and Brinell tests. Commonly, for the Grade 5 bolts, the HRC taken will have values ranging from around 25 up to 35 HRC. Achieving the right level of hardness is important; insufficient hardness could result in early wear or even failure during service, especially in those applications like automotive assemblies that exert tremendous dynamic forces on bolts.
Finally, fatigue testing is essential in determining how well bolts can sustain repeated loading cycles over some time. This test simulates conditions through which bolts experience service, such as in automotive suspension or machinery parts. This means that thousands of loading cycles at different levels have to be imparted in order to perform fatigue tests on SAE Grade 5 bolts. Tests of this nature have given indication regarding the life span and reliability of bolts under application. For instance, bolts that withstand at least 100,000 cycles at 50% of their yield strength qualify as being fit for high-stress applications and additionally assure manufacturers and consumers of durability and performance in service.
Factors Affecting Strength
Material composition, heat treatment processes, and environmental conditions are some of the critical factors that determine the strength of SAE Grade 5 bolts. The main material used in the making of these bolts is medium carbon steel, usually comprising 0.25% to 0.55% carbon. The carbon content in this metal will significantly influence its hardness and, thus, the tensile strength of the bolt. A bolt that has a higher carbon content normally has greater strength. However, when this goes beyond the range of the optimum, brittleness might also be caused. This in turn can render a bolt incapable of delivering appropriate performance against such an application that needs flexibility under the load.
Another indispensable factor determining the strength of SAE Grade 5 bolts is related to heat treatment. The typical pattern of heat treatment includes quenching and tempering that enhance the tensile and yield strength of the bolt while enhancing toughness. For instance, a Grade 5 bolt properly heat treated should have about 105,000 psi yield strength. Under the conditions of incomplete or incorrect heat treatment, such strength will not be achievable in some bolts. On investigation, it was even revealed that when bolts experience insufficient heat treatment, one may achieve yield strengths at a value as low as 80,000 psi—again, safety from such failure would be overlooked in the high-strength application.
It therefore follows that such bolts owe their strength to the manufacturing process as well. Forgings, machining, and surface treatments are amongst the factors which can vary the microstructure of steel. In forging, for example, the flow of the grain structure in steel might be aligned in a manner which results in increased strength. Bad machining, on the other hand, may introduce stress concentrations which reduce the strength of the bolt. The test results have proved that bolts forged using the optimum forging techniques achieve a tensile strength that is as much as 15% greater than those manufactured through traditional machining processes.
Lastly, temperature and exposure to corrosive elements are also environmental factors affecting SAE Grade 5 bolts. High temperatures alter the mechanical properties of this steel; for example, the yield strength decreases as the temperature increases. As can be seen at a high temperature of more than 400 degrees Fahrenheit, there is some loss of yield strength in Grade 5 bolts—even to the extent of 20% from its normal yield strength—restrictive in many applications in which these bolts are engaged in exhaustive environments or high-temperature conditions, such as an exhaust system.
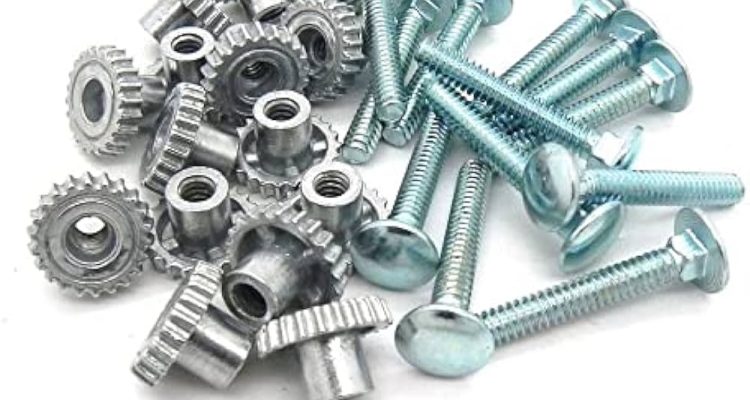
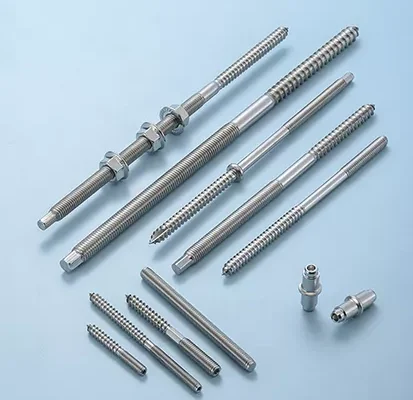
What Is A Double-Ended Bolt And Why Use It
Double-ended bo…
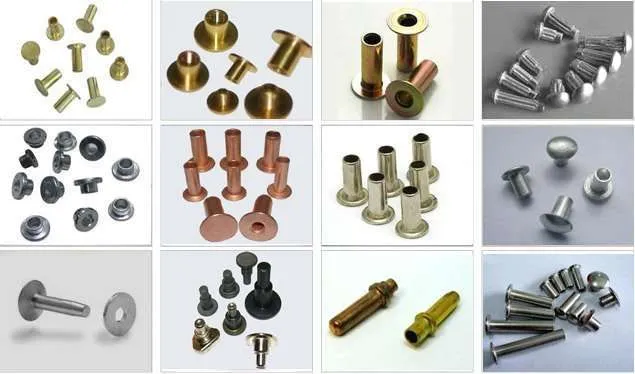
How to Design and Order Custom Rivets
Design custom r…