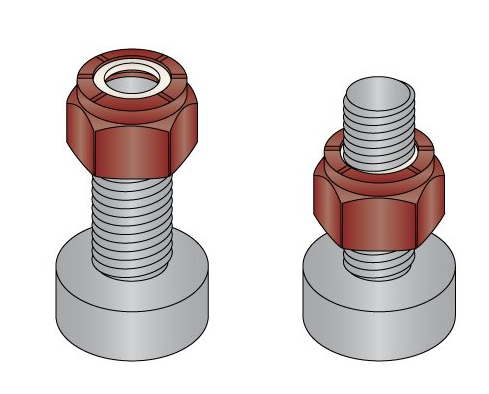
What is the most common lock nut
The most common lock nut is the nylon insert lock nut, known for its effective vibration resistance. It features a nylon collar that grips the bolt thread tightly, reducing loosening even under dynamic loads.
Nylon insert lock nut
Nylon insert lock nuts, commonly referred to as Nilock nuts, are a popular choice in various industries to prevent bolts from loosening due to vibration and dynamic load. The nut contains a nylon collar that, once enabled, forms a tight frictional fit with the applied bolt thread. Nilock nuts retain their rigidity even under harsh vibration conditions, and in a vibration test simulating automotive road conditions, Nilock nuts maintain their torque and clamping force better than traditional lock nuts. Nylon inserts are able to flexibly adapt to the shape of the thread, creating a locking action that is largely unaffected by changes in temperature and pressure in a typical operating environment, with an operating temperature limit of 120 degrees Celsius.
Nilock nuts are available in a variety of materials including carbon steel and stainless steel grades. Stainless Steel variants Galvanized or cadmium-plated carbon steel Nilock nuts offer additional durability and corrosion resistance at a lower cost and are suitable for general use in industries such as construction and machinery.
The use of Nilock nuts can significantly reduce the need for additional locking mechanisms such as washers or thread locking adhesives, and replacing traditional locking washers and bolting devices with Nilock nuts can reduce assembly costs by up to 20%. Nylon inserts begin to lose their elastic properties and begin to degrade at temperatures above 150 degrees Celsius, which limits their use in high-temperature applications such as near engine blocks or exhaust systems. In these cases the use of all-metal locking nuts or chemical thread locking agents may be more appropriate.
Nyloc nuts are known for their durability, nylon properties are affected by temperature, the maximum operating range is about 120-150 degrees Celsius, in the manufacturing industry, machinery needs regular maintenance, can reuse Nyloc nuts two to three times before replacement.
Material compatibility
Material compatibility of nylon insert lock nuts (commonly referred to as Nilock nuts) are engineered to provide a reliable locking mechanism through which the nylon insert interacts with the thread of the bolt, but the metal material choice of the nut significantly affects its effectiveness, durability, and suitability in a variety of environments.
The most commonly used material for Niloc nuts is carbon steel, which provides excellent strength and durability. Carbon steel Niloc nuts are often coated with zinc or cadmium to provide corrosion resistance and are suitable for general use in industries such as construction and automotive.
In environments susceptible to high humidity and corrosive elements such as the ocean or chemical processing applications, stainless steel Niloc nuts are preferred. Stainless steel variants such as AISI 304 or 316 provide better corrosion resistance without the need for additional coatings.
In environments where there is frequent exposure to chemicals, seawater or other corrosive elements, stainless steel Niloc nuts are necessary. Their inherent corrosion resistance ensures long-term performance and is not compromised by degradation of nut integrity.
Despite the heat tolerance limits of the nylon insert itself (usually up to 150 degrees Celsius), the metal part of the nut can withstand higher temperatures. Special superalloys are sometimes used when Nilock nuts must work at extreme temperatures.
Vibration resistance
Nylon insert lock nuts (or Nilock nuts) are specifically designed to keep bolted connections secure under conditions of high vibration and dynamic load, which are common in many industrial, automotive and aerospace applications.
The main mechanism of vibration resistance of Niloc nuts lies in nylon inserts. The insert deforms elastomeric during installation and fits the thread of the bolt tightly. The resulting interference fit provides significant resistance to loosening, and the nylon creates a radial force on the thread. This force effectively increases the friction between the bolt and the nut, preventing inadvertent loosening.
The nylon used in these inserts is usually a polyamide type, chosen for its excellent balance of strength and elastic deformation. This allows the insert to grip the bolt effectively under normal operating conditions without permanent deformation.
Nilock nuts consistently outperform conventional fasteners in terms of vibration resistance, and in vibration tests simulating automotive suspension conditions, Nilock nuts have shown superior ability to maintain clamping forces over long periods of time. Under similar conditions, the failure rate of conventional nuts may be 50% higher than that of Nilock nuts.
Although Niloc nuts are strong, they do have limitations in environments where the thermal tolerance of nylon (usually about 150 degrees Celsius) exceeds the limit. Nylon may lose its elasticity under such conditions, reducing the vibration resistance and overall effect of the nut.