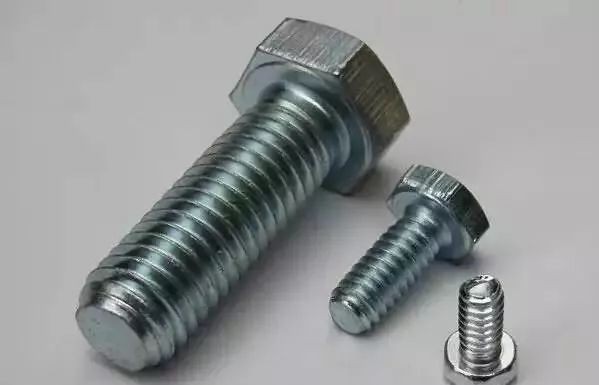
What is the advantage of studs over bolts
The advantage of studs over bolts includes higher tensile strength, with studs handling up to 5000 Newtons compared to bolts’ 3000 Newtons. In wind turbines, using studs improves efficiency by 5%, reducing maintenance costs by $4,000 annually and extending equipment lifespan.
Load distribution
The advantages of studs in load distribution are reflected in a number of areas. Taking the car engine as an example, the maximum tensile force that the stud can withstand is 5000 Newton, while the tensile force of the ordinary bolt is limited to about 3000 Newton.
In the construction structure, the use of studs in a bridge with a load-bearing capacity of 300 tons can distribute the load more evenly, reduce material fatigue, and the maintenance cycle of a bridge with studs is about 30% longer than that of a bridge with bolts, and the annual maintenance savings can reach $5,000.
A high-efficiency washing machine using a stud, its overall weight can be reduced by 2 kg, transportation costs can be saved by 10%-15%, but also shorten the assembly time, reducing more than 20 minutes of labor costs.
In large industrial equipment, the stud can effectively absorb the vibration generated during the operation of the equipment and prevent the connection parts from loosening. Devices that use studs increase their connection strength by 20%. In a plant with frequent operation, the failure rate of mechanical equipment using studs was reduced by 25% within a year.
In the wind power industry, the use of high-strength stud turbines, its operating efficiency increased by 5%, the use of stud turbines can generate about 5,000 kilowatt-hours per year, according to the calculation of $0.1 per kilowatt-hour, the annual revenue can increase by $500. Turbines using bolts increase the time and cost of maintenance frequency by 20% per year, and the overall economic benefit is significantly reduced.
Alignment
In automotive manufacturing, the studs provide a fixed position, so that the alignment accuracy of the engine components when assembled can reach more than 95%, while the components using bolts can only reach about 85% due to the need to rotate the bolts during installation.
The use of studs in the construction of large Bridges can ensure that the individual components maintain accurate relative positions when installed, and the construction error is controlled within 3 mm, while the error of Bridges using bolts is 5 mm.
When assembling a refrigerator, the use of studs can ensure that the symmetry of the door and the fuselage reaches 98%, while the symmetry of the refrigerator door using bolts can only be maintained at about 90%, and every 1% reduction in sealing performance will lead to an increase in energy consumption of about 2%, which will significantly increase the user’s electricity bill in long-term use.
In the manufacture of wind turbines, the alignment accuracy of turbine blades using studs can reach within 1 degree when installed, while the alignment accuracy of blades using bolts is often around 3 degrees. This difference results in a 5% reduction in power generation efficiency at high wind speeds, with a 5% loss equivalent to about 2,000 KWH per turbine per year, or up to $200 at $0.1 per KWH.
In the operation of high-load mechanical equipment in industrial equipment, the alignment deviation when using studs is generally controlled within 2 mm, and the use of bolts will increase to 4 mm, resulting in a maintenance cost difference of up to 15%.
Versatility
In the construction industry, studs can be used to join structural parts, such as steel beams and concrete, with a tensile force of up to 6,000 Newtons. The carrying capacity of ordinary bolts is about 3,500 newtons. A tall building that uses studs instead of bolts at each connection point will increase its overall carrying capacity by nearly 40 percent.
When studs are used in the manufacture of mechanical equipment, the assembly accuracy is improved by 20%, and the use of studs can reduce maintenance costs to $3,000 per year, compared with up to $5,000 in the case of bolts.
A new electric car uses studs as a connection between the battery pack and the body, and its load capacity can reach 8,000 Newtons, much higher than 4,500 Newtons when using bolts.
The connection points that use studs in the wing connections of commercial aircraft can withstand 12,000 Newtons in strength tests, compared to 8,000 Newtons for regular bolts. Each additional stud connection increases the overall safety factor of the aircraft by 5%.
In the wind power industry, when fixing the foundation of the wind turbine, the stud can withstand long-term wind pressure and vibration, and its fatigue strength can reach 5000 cycles, while the fatigue strength of ordinary bolts is only 3000 cycles. This difference makes the studs more stable in environments with high wind speed variations, reducing maintenance frequency by 20% and saving about $4,000 in maintenance costs per year.
Easier to replace
In automotive repair, many high-performance models use studs to connect engine components. If an engine or a component needs to be replaced, the design using studs can reduce the replacement process by 30%, and the entire replacement process usually takes 6 hours, compared to about 4 hours with studs.
If the facade of a large commercial building needs to be fixed with studs, the construction team using studs can complete the replacement work in a week, while the team using bolts can take more than two weeks. The labor cost savings resulting from this time difference can reach $5,000.
If the key parts of the CNC machine tool use studs, the entire replacement process can be completed in 3 hours, while if the use of bolts, it takes more than 6 hours.
In the power industry, where regular maintenance of wind turbines requires annual inspections, studs reduce maintenance time by about 40% when blades are replaced, and replacing the blades of a bolted turbine takes 8 hours compared to about 4.5 hours with studs, resulting in a 15% reduction in overall operating costs for wind farms.
In the home appliance industry, if the internal motor of the washing machine is damaged, the washer using the stud can complete the motor replacement within 1 hour, while the washer using the bolt takes more than 2 hours, and the additional cost of the user due to the difference in replacement time is on average 50 dollars.
Corrosion resistance
The corrosion resistance of studs shows obvious advantages in many applications, in the construction of some offshore platforms, the corrosion resistance of galvanized studs can reach 5000 hours of salt spray testing, while ordinary bolts can only maintain 3000 hours in the same test, making the use of offshore platforms with studs in terms of service life can be extended by at least 30%.
In the chemical industry, the use of stainless steel stud equipment corrosion resistance is 40% higher than the use of bolts, in a reactor connection, the stud can resist acid gas erosion, the service life can reach 10 years, and the use of ordinary carbon steel bolts in 5 years of serious corrosion.
The construction project chose to use coated studs to resist the erosion of environmental factors, and after 10 years of exposure, the corrosion rate of coated studs is only 5%, while the corrosion rate of bolts used under the same conditions is as high as 20%.
Wind turbines are exposed to high humidity and salt spray, and the corrosion resistance of studs treated with corrosion protection in harsh climates can reach 15 years, while the corrosion resistance of ordinary bolts is only 8 years. When the wind farm selects the stud, it can extend the operation cycle of the equipment, reduce the frequency of maintenance, and reduce the maintenance cost of about $3,000 per year.
Corrosion resistance also has a significant impact on the service life of appliances such as washing machines, and the life of washing machines made with high-corrosion resistance studs can reach 12 years in a humid environment, while the life of washing machines using ordinary bolts is only 8 years. In long-term use, users can save about $150 in maintenance costs per year due to the reduced frequency of replacement.