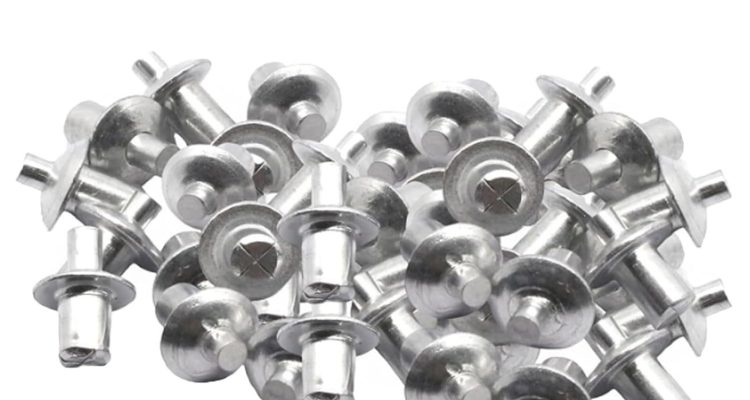
What Is A Custom Bolt And How To Use It
Custom bolts are specifically engineered for unique applications in industries like automotive and aerospace, ensuring optimal performance and enhanced safety.
Types of Custom Bolts
This implies that custom bolts are manufactured to handle specific functions and a variety of custom options such as material, head style, thread size, and coatings can be selected to meet special needs.
Material Varieties
Depending on strength, corrosion, and temperature requirements custom bolts can be made from a range of materials. Carbon steel is often employed for general use due to its strength and cost-effective price whilst Stainless steel, which offers high corrosion resistance (ideal in marine and chemical-processing environments); Titanium, which has a high strength-to-weight ratio (valued in aerospace applications) and Inconel, designed for use at extreme temperatures up to 982°C typically in engine and turbine applications.
Head Styles
The head style of the bolt will determine required tooling for installation and how load will be spread. Options include:
- Hexagonal heads are the standards and is compatible with a wide variety of tools to be used with good torque leverage.
- Originally designed for high torque resistance with wrenches, square heads are less common now.
- Torx heads of all sizes are good for anything with more torque – especially in automotive and electronics where other drives would risk cam-out.
Thread Types
Threads are special-purpose defined explicitly to perform well in particular situations such as:
- Coarse threads are stronger and easier to work with in materials such as cast iron, but are less accurate so fine threads is the preferred choice for use with thin-walled sections.
- Thin threads has higher tensile strength and applied in the high precision applications.
- ACME threads are trapezoidal in shape and used for applications that demand strong, easy-to-use load bearing, such as vices or lead screws.
Surface Coating or Treatments
Specific coatings and treatments are normally carried out on custom bolts in order to support their desired properties.
- Galvanized steel bolts are coated with zinc, which protects them against corrosion making them ideal for outdoor applications.
- These offer very low friction and good chemical resistance, and can be used together with coatings that help stabilise surface friction when they may slacken after repeated assembly/disassembly actions.
- In marine environments, it is able to provide very good corrosion resistance, but cadmium is less commonly used due to environmental concerns.
Applications of Custom Bolts
In a monopoly situation, custom bolts play a critical role by several of the demanding industries, where they are 100 % required to be specially designed and made to get safety, reliability, and performance. Here are the common sectors where custom bolts find application:
Automotive Industry
Custom bolts are a core need for the automotive sector as well, because custom nails help to assemble both engines and the bus chassis. Many manufacturers require bolts that can withstand those same intense vibrations and thermal cycles without breaking. For example, proprietary high-temperature bolts used in engine assemblies can easily handle temperatures up to 300°C and are passivated with corrosion-resistant coatings to withstand exposure to the many harsh chemicals found in automotive environments.
Aerospace Sector
For the aerospace industry, lightweight bolts that can hold up to the high pressures and temperatures of flight are essential. Common materials are Titanium and Inconel. For critical flight components like jet engines and airframes found in aerospace applications, custom bolts are specifically engineered to withstand stress loads in excess of 1,000 MPa ensuring that they are robust and safe for their intended use.
Architecture & ConstructionInfrastructure
Custom bolts are used to build bridges, or skyscrapers which standard bolts cannot provide the necessary strength and durability; In bridge construction, for instance, you frequently see large diameter high-strength tension control bolts. The bolts range in size and can be as big as 4 inches in diameter with the ability to resist tensile loads of several tons – an important capability when firmer materials are needed to ensure structural stability under changing loads and environmental conditions.
Consumer and Electronics
Custom bolts made for the electronics industry, typically consumer devices such as smartphone and laptops are very small and exacting. As electrical connections, they are often made from inert metals that do not outgas and which resist thermal expansion. Such as bolts used to secure a heat sink to a microprocessor, where they must conduct heat well and remain in their torque range through repeated heating cycles.
Applications: for Marine and offshore applications
Custom Bolts for MarineWhere the environment is a marine one, custom bolts are essential to bear up in the spearing sea water and high-pressure conditions. Commonly used stainless steel grades 316, and 317L provide excellent corrosion resistance. Bolts are also subject to a high load and have to be fatigue resistant in an offshore platform so that the structure remains in tact when exposed to storm waves and winds.
Design and Manufacturing Process
Custom bolts are high strength bolts requiring careful design and manufacturing to meet specific application requirements with common above-average ultimate tensioning loads.
Original Design And Engineering
The process starts with an extensive engineering analysis to establish exactly what specifications the bolt is going to need in terms of dimensions, tolerances and composition. CAD software models the design of the bolt by engineers, with considerations made for loads on it, environmental conditions and mating components. An example is a bolt intended for aerospace may need to live in temperatures of -50°C up to 150°C and shear stress up to 1100 MPa.
Material Selection
Your choice of the proper material is important. Materials are chosen for their properties strength, corrosion resistance, or ability to tolerate heat. Common materials include:
- High strength applications that use alloy steels, which are often heat-treated and can have tensile strengths between 900 to 1200 MPa.
Corrosion-resistant stainless steel
Aerospace and racing applications in which strength and lightweight are key would make use of titanium.
Manufacturing Techniques
Used particularly for larger or highly stressed components, Forging for the bulk-forming of the bolt, providing a greater grain flow (and therefore superior mechanical properties).
Thread and Head Shape
Toughness & wear resistance to be improved by application of Heat Treatment. E.g., Busing & tempering would raise hardness and strength of steel bolts.
A substance coating may be employed for appearance, corrosion resistance and oxidation immunity, or even for other purposes to clean up a part of the topological government features.
Quality Control
Quality control is of the utmost importance throughout the manufacturing process. This includes dimensional checks, mechanical tests, and material testing. Specific tests might include:
- A Tensile Test to prove that the bolt can withstand the required forces.
- Hardness testing translated the materials have received correct heat treat
- To detect the internal flaws for critical used on the application an Ultrasonic testing would be conducted.
Advantages of Using Custom Bolts
The premium bolts provide a host of advantages that help in a variety of applications, particularly for which standard fasteners fall short or do not operate up to expectations.
be mechanical properties that are tailored
They are designed to provide the mechanical properties required for the application. Aerospace bolts may be made from titanium, due to its low density and high tensile strength of around 900-1,140 MPa in the material used, or else stainless steel. This customization provides the best performance and reliability under the different stresses each application offers.
Enhanced Durability
Custom bolts can have up to 10x the work life of standard bolts in harsh environments by selecting appropriate materials and treatments. For example, excluding the use of higher strength grades e.g. grade 8 or Industrial Strength in carbon steels, bolts used for marine structures may be made from duplex stainless steel which provides excellent resistance to pitting and chloride corrosion. That means they stand up to the corrosive seawater environment for decades without substantial decomposition.
Precision Fit and Assembly
Unlike standard bolt sizes, custom bolts are made to exact specification of the equipment or assembly they serve. This allows precise linear motion and sliding while at the same time keeping a good grip on various load on individually laterally moving synchromesh surfaces where the load may be oriented to just one surface in the opposite direction. This precision avoids problems that include vibration loosening, mechanical fault, or multi-axis alignment. Custom bolts are vital for the automotive industry to guarantee that performance-critical structural and powertrain fasteners never fail, even at speed and under stress.
Very Low Cost over the Long Run
Even considering that custom bolts have a higher initial cost compared to standard bolts they are indeed a cost-efficient alternative in the long run. With less and less need for replacements, as well our ability to minimize risk of failure related damages across the board and decrease machine downtime custom bolts prove highly valuable. These could be anything from a particular bolt in use in an industrial machine, to software which if fails, breaks down the whole logistics system and costs hundreds of thousands of dollars.