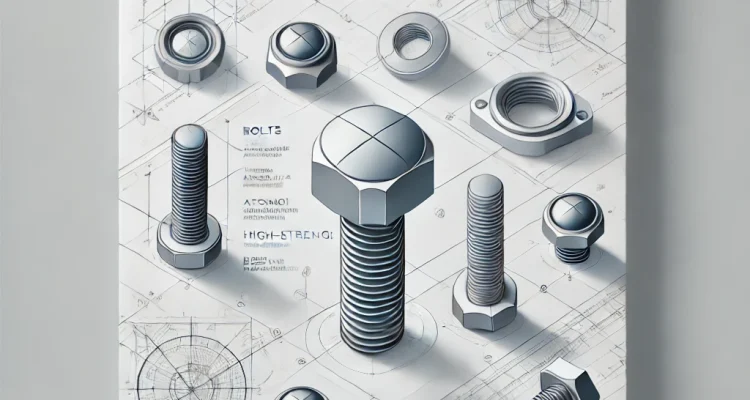
What are special bolts
Special bolts are used in the fields of aerospace, automotive manufacturing, and construction because they have high strength, corrosion resistance, and high-temperature performance. Generally manufactured from alloy steel or titanium alloys with high strength above 1000 MPa, they undergo dedicated manufacturing technologies and quality controls, for example, the precision forging process, heat treatment processes, and surface finishing. Regular ultrasonic and tensile testing standards ensure their strength and dependability in any circumstances.
Characteristics of special bolts
One of the most widely used is titanium alloy bolts in aerospace and has a tensile strength of more than 1200 MPa, while that of common carbon steel is only a quarter. The yield strength of the titanium alloy bolts used in Boeing 787 aircraft was maintained with excellent heat resistance and was able to withstand strong vibration during takeoff, even when they were suddenly removed at minus 60 degrees Celsius or high temperatures up to 450 degrees Celsius. When constructing a tall building built in an earthquake area like Japan, it is required that high-level tensioning hexagon head bolts are utilized as fasteners for steel beam structures since fully tightened nuts do not loosen even under extreme seismic conditions. The bolts have been subjected to severe seismic tests that guarantee resistance to an earthquake of magnitude 8.
Special bolts are well-suited for corrosion and high-temperature resistance. Stainless steel bolts with the same mechanical properties used in shipbuilding have a corrosion depth of less than 0.1 mm after decades of exposure to seawater, making it possible for structures submerged at sea bottom safety assurance decade years structure life cycle and so on. In the chemical industry, Inconel 718 alloy bolts commonly used in high-temperature environments of 700°C can maintain a strength level above 85%, while special alloy bolts employed by oil and gas pipelines can have a service life of over two decades under corrosive gases or liquids. The use of these bolts means expected stresses must be withstood during testing and then prove to remain stable when subjected to the test houses to extreme running conditions.
Applications of special bolts
The Boeing 787 aircraft, contains over 30,000 custom fasteners in just its wings and fuselage. The bolts, built from an aluminum-lithium alloy, are said to be 15% lighter than similar units and capable of withstanding tensile forces up to around the 1000 MPa mark. These bolts are tested for 5,000 load cycles from the pressure experienced by taking off and landing to handle rare situations when a lot of weight is applied. Grade 10.9 high-strength special bolts for fastening electric vehicle battery modules in automotive manufacturing have a tensile strength of 1040 MPa to prevent loosening in case of collision.
The structural bolts of Tokyo Skytree in Japan are made from high-strength materials that can withstand a magnitude 8 earthquake without breaking. The bolts can carry 5,000 kilograms each. Nickel-based alloy bolts are also used in marine engineering for the construction of offshore wind farms, which must be installed and last more than 20 years under corrosive seawater conditions. The structural bolts that make up the oil platform are made of Inconel 718 alloy and have passed a salt spray test for 1000 hours to ensure they will be reliable under extreme offshore circumstances.
Manufacturing process of special bolts
Special bolts are generally made from alloy steel or titanium alloy with strength higher than 1000 MPa. The precision forging guarantees the bolt shape and size, along with a dimensional tolerance of ±0.02 millimeters. Quenching at 950°C and tempering at 600°C are heat treatment processes that increase the hardness of bolts while also improving their toughness. Aerospace bolts are aged for 20 hours, which can reach a yield strength of more than 1300 MPa. Marine engineering bolts usually undergo hot-dip galvanization, with a coating thickness of not less than 15 microns.
The special bolts are closely related to the quality requirements of production. All bolts must clear UTS (ultrasonic testing), with accuracy up to 0.1 mm, showing no internal crack or bubble between its batch of bolts. Bolts should be tested in both tension and fatigue for a minimum of 500,000 cycles to ensure they do not experience any form of failure between loads. In addition to it, bolts have also been subjected to an adhesion test for the coating before they can be packed: Peel resistance of 8 N·mm is necessary because peeled coatings often drop into spray guns. Final inspection of the finished product is carried out under the International standard ISO 898-1 to guarantee safety and reliability for bolt assemblies in multiple sector applications.