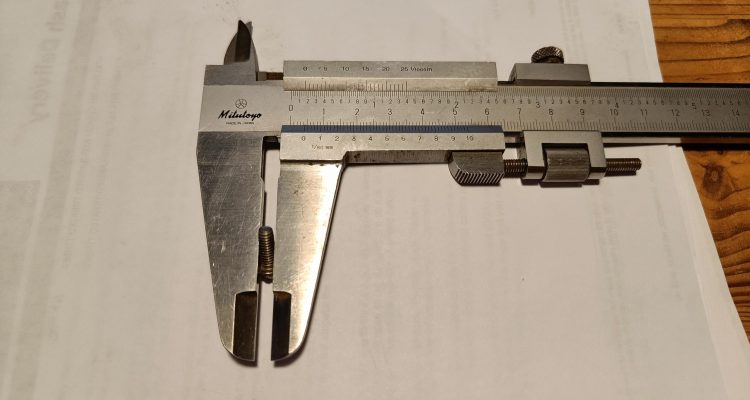
how to measure thread size with caliper
To measure thread size with a caliper, first measure the outer diameter (OD), such as 10 mm for an M10 bolt. Then, measure the pitch, like 1.5 mm between thread peaks for coarse threads. Finally, check the thread length, for example, 30 mm on a 50 mm bolt.
Measure the Outer Diameter (OD)
This is where accurate dimensions are critical to insure compatibility and prevent a number of different failures when measuring the OD of a thread with a caliper. To measure the OD, place the jaws of a caliper on the highest points of the threads-known as crests-against the widest part of the threaded component.
Using a standard M10 bolt, the OD would have an exact measurement of 10 mm. This reading of 9.85 mm with the caliper would suggest that the bolt might be worn down and compromised in its structural integrity or function. Common examples for OD in metric threads include M6 at 6 mm, M8 at 8 mm, and M12 at 12 mm. Commonly used sizes in many mechanical and automotive industries, the slight differences greatly influence strength and fitment. For example, over a 0.1-mm difference in OD can be the difference between a properly seated thread in a hole and one apt to strip during tightening.
For imperial threads, a 1/2″ bolt has an OD of 0.500 inches. And if the caliper reads something like 0.492 inches, that small difference might mean the bolt is undersized or has been subjected to wear. A variation of this little can become crucial in applications that involve high torque, as in construction equipment.
For accuracy, take the OD that you measure against the specifications of the manufacturer. In case you are measuring an M8 x 1.25 bolt, it should be measured at 8 mm OD, while any low value will signify the degradation of material. In industries where precision is an important aspect, like in aerospace, even a deviation of 0.05 mm makes a part null and invalidates it and results in costly replacements.
Even 0.1 mm of difference on the OD might be pretty negligible. But this little variation will result in high-stress applications or catastrophic failure in heavy machinery, which could lead to thousands of dollars in damages and repairs.
Measure the Pitch
Thread pitch measurement using a caliper is all about the measurement over the distance between adjacent threads’ peaks, which shall help in ascertaining the kind of thread, either coarse or fine threads. In metric threads, the pitch is expressed in millimeters, while for imperial threads, it is expressed in threads per inch, TPI. In measuring pitch, carefully place the jaws of the caliper on two consecutive thread crests.
For a bolt M10 x 1.5, the pitch of the bolt is 1.5 mm, which means that two consecutive peaks of the thread should be exactly 1.5 mm apart. Therefore, any distance measured with a caliper of 1.45 mm or 1.55 mm may simply indicate minor wear or damage in the thread. For finer threads, like M10 x 1.0, the pitch will be 1.0 mm, which means that within the same length, more threads are packed. This is usually applied when high accuracy or more tightness in fastening is required, in car engines where M10 x 1.0 threads share a better grip as compared to the coarse one.
This would mean that a common pitch measurement in imperial units would be for a 1/2″ x 13 bolt, and it would have a pitch of 13 threads per inch. What this means is that within one inch of the threaded section, there are 13 distinguishable threads. If you measure and find 12.8 TPI or 13.2 TPI, this variation could result in improper mating with a nut and lead to stripping or failure under load. A 1/2″ x 20 bolt has a pitch of 20 TPI, meaning it’s a finer thread that allows more surface contact for better fastening in high-stress applications.
It is much easier to appreciate the importance of pitch when comparing different applications. A typical case is that in which an M6 x 1.0 bolt has a coarse pitch of 1.0 millimeters, while an M6 x 0.75 bolt has a fine pitch of 0.75 millimeters. In precision machinery, the 0.75-millimeter pitch is fine and therefore better for control and tension, for this type of components requires tight assembly and minimum loosening after some time. Whereas a coarse pitch such as 1.0 mm suits an application requiring rapid assembly and disassembly such as the scaffolding for the use in construction.
Accuracy of the pitch measurement has much importance, especially in high-load applications. The pitch of a big bolt like M20 x 2.5 has 2.5 mm. If it is off by only 0.1 millimeters, then 2.4 mm or 2.6 mm will give a very different load distribution in the threads. It may lead to short-term failures in highly loaded structures like bridges and cranes.
In aerospace, the 5/16″ x 24 bolt has a pitch of 24 TPI. It is very fine and thus finds its application in very high-precision assemblies. Any deviation, even of 0.1 TPI, may lead to serious consequences.
Measure the Thread Length (if needed)
The length of the thread will be necessary when determining the amount of engagement that a bolt or screw will have in the mating material. Measuring over the thread with a caliper ensures a precise measurement, which is crucial in load-bearing applications. To make a thread length measurement, open the jaws of the caliper and span from the first thread to the last full thread.
For instance, consider the ordinary M10 x 50 mm screw. The “50 mm” denotes the total length, whereas the actual length of the thread itself may be 35 to 40 mm, the caliper reading of 38 mm may be sufficient to keep in place heavy materials such as steel or aluminum with sufficient engagement. If you mistakenly use a bolt with just 30 mm of thread length, it cannot grip satisfactorily, in particular in those applications where maximum threads engagement is needed for stability in the material being fastened.
The thread length in automotive matters a lot concerning proper fastening. A 1/2″ x 3″ bolt could have its thread length of 2 inches. The difference will matter when securing engine components. You only measure 1.5 inches of thread, meaning the bolt couldn’t completely secure the part, especially under vibration or high torque.
Fine-thread bolts like M8 x 1.25 x 60 mm may have a thread length of 50 mm – which leaves only 10 mm of unthreaded shaft. This is used in those applications where there is a longer threaded length, especially for fastening through thick materials. Even a slight variation in thread length while measuring can make the difference. 45 mm thread length of a bolt may weaken the fastening; this is true especially if the load dictates a full engagement of 50 mm thread.
In construction, the bolt-like M20 x 150 mm has about 90-100 mm of thread length to fasten big structures like beams or girders. As a result, if you apply only 80 mm of thread length when taking the measurement with a caliper, the reduced length might lead to a failure in load distribution. The structural weaknesses in high-stress environments like bridges and cranes, where the thread length directly influences the load-carrying capability, hence compromise the integrity of the structure involved.
Precision is everything when it comes to aerospace applications. A 5/16″ x 24 x 2.5″ bolt could only have 1.75″ of threaded length. If the actual length measured with a caliper falls short by even as much as 0.1″, then disaster can occur under high stress and high torque conditions.