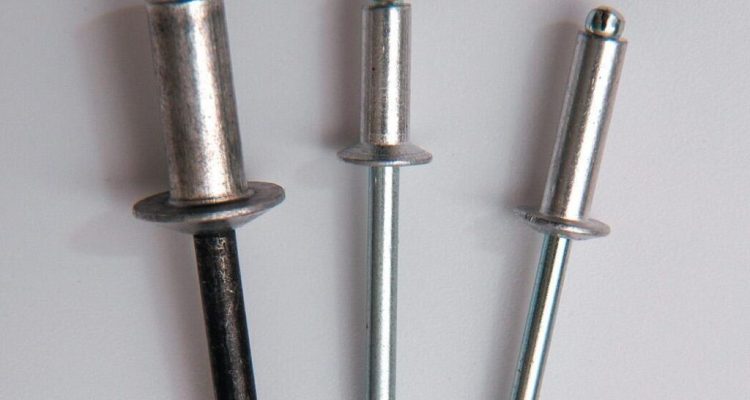
How to know what size rivets to use
To determine the correct rivet size, measure the total material thickness and choose a rivet with a diameter about three times the thickest layer and a length 1-2mm longer than the combined thickness for a secure hold.
Material thickness
Suppose a project involves connecting two stainless steel plates, each thickness is 4mm, then the total material thickness is 8mm, according to industry standards, the selection of the length of the rivet should consider an additional 1-2mm to ensure that the rivet can be fully expanded and firmly fixed material, so the appropriate rivet length should be 9-10mm. Diameter The recommended rivet diameter is about three times the thickness of the thickest single layer material to be connected, that is, select about 12mm rivet.
In aviation manufacturing, the material thickness is more stringent in the selection of rivets. If you want to connect a 1mm thick aluminum plate and a 2mm thick titanium alloy plate, the total thickness is 3mm, will choose a rivet length of at least 4mm. Due to the high strength of titanium alloys, it is recommended to use rivets with a diameter of at least 6mm to ensure adequate shear resistance and durability.
In the automotive industry, an application needs to connect two 2.5mm thick steel plates, the total thickness of 5mm, the selection of rivets should not only consider the length of about 6mm, but also need to ensure that the diameter of the rivets can provide sufficient bearing capacity, choose a diameter of 7.5mm rivets.
To assemble a table, it is necessary to attach a 1.5mm thick metal leg to the top of a 15mm thick board, with a suitable length of rivets of at least 17mm to ensure that it can be fully penetrated through the metal leg and extended in the board. Because the wood is relatively soft, a 4.5mm diameter rivet can provide stable support and long durability.
When decorating or repairing an old building, to connect a 3mm thick copper plate and a 5mm thick wooden board, the selection of rivets should consider a length of at least 8mm and a moderate diameter of about 8mm, to ensure that the different materials provide a strong and lasting connection.
Rivet diameter
In the machining process, two aluminum plates with a thickness of 3mm and 2mm are connected, and the total thickness is 5mm, and the recommended rivet diameter is three times that of the thickest single layer material, that is, 9mm diameter rivet is recommended for 3mm aluminum plates.
In the construction industry, especially in the frame structure of metal components, it is necessary to connect a 4mm thick steel beam with a 6mm thick steel plate, with a total thickness of 10mm. At this time, the diameter of the rivet should be selected as three times the thickness of the thickest single layer material, that is, the diameter of the rivet should be selected as 18mm
In the aviation industry, the choice of rivet diameter is particularly strict, connecting a 1.5mm thick aluminum alloy skin and a 2mm thick aluminum alloy skeleton, it is recommended to use at least 10.5mm diameter rivet. This rivet diameter ensures that high speed flight can withstand huge air pressure without structural failure.
In the production of household appliances, two stainless steel plates each 0.5mm thick are connected, and the diameter of the rivet is usually 1.5mm. Too large a rivet diameter may penetrate the sheet, while too small may not provide enough fixing force.
In shipbuilding, the material thickness is large and requires extremely high sealing and corrosion resistance, and 15mm diameter rivets are usually used to connect 5mm thick hull steel plates. Rivets of this specification provide long-term durability and stability under conditions of seawater erosion and heavy load pressure.
Rivet material
For the aviation industry, high-strength aluminum alloy or titanium alloy is selected for rivets, because these materials have good corrosion resistance and enough strength to withstand the violent vibration and pressure generated during high-speed flight. The commonly used 2024-T4 aluminum alloy rivet has a shear strength that a single rivet can withstand of about 270 to 325 MPa, which is enough to meet the connection needs of most aviation components.
Due to its high strength and good bearing capacity (the usual tensile strength range is 400 to 500 MPa), steel rivets can be applied to structures that bear large loads. Steel rivets are riveted in a cold state, and after completion, the connecting parts can be firmly locked through the deformation of the rivet head and the extension of the rivet itself.
Stainless steel rivets such as 316 stainless steel have excellent corrosion resistance and are especially suitable for use in ships, offshore platforms or buildings in coastal areas. 316 stainless steel rivets have high corrosion resistance at room temperature and can effectively resist salt erosion in seawater and atmosphere.
Copper rivets are widely used for their excellent conductivity and good thermal conductivity, and are suitable for the fixing of circuit boards and other electronic components. The conductivity of pure copper rivets can reach 100% IACS (International Annealed copper standard), while providing the necessary mechanical stability.
In the automotive industry, aluminum rivets not only reduce the total weight of the vehicle, but also help achieve better fuel economy and lower emissions. Rivets made of 7075 aluminum alloy with a tensile strength of up to 572 MPa are able to provide good structural strength without adding extra weight.
Rivet type
The following is a detailed introduction of several common rivet types and their application:
Solid rivets: Solid rivets are the most traditional type of rivets and are widely used in areas that require high strength connections, such as aviation and shipbuilding. In the manufacture of aircraft, solid rivets made of aluminum alloy 2117 or aluminum-nickel-copper alloy are commonly used, which can withstand shear strength of up to 470 MPa and tensile strength of 620 MPa.
Blind rivets (pull rivets) : Blind rivets are especially suitable for occasions where only one side can be accessed, such as fixing wall panels or furniture backboards. The blind rivet is unfolded by pulling the rivet core with the rivet gun to form anchorage. A common blind rivet is made of 5052 aluminum alloy and provides approximately 345 MPa shear strength and 480 MPa tensile strength, making it suitable for a variety of industrial and commercial applications.
Semi-hollow rivets: Semi-hollow rivets are suitable for connections requiring better appearance and lower load requirements, such as leather goods and clothing accessories. These rivets are made of mild steel or stainless steel, providing the advantage of being easier to install than solid rivets, while having sufficient structural strength to support non-structural applications. Stainless steel semi-hollow rivets can achieve shear strength of about 290 MPa and tensile strength of 310 MPa.
Tubular rivets: Tubular rivets are often used in the field of furniture and household appliances because of their low manufacturing cost and easy installation. When tubular rivet is applied, its tubular body will expand outward after applying pressure to form a tight fixation. A typical application is the use of tubular rivets made of nylon or ABS plastic on the plastic parts of the TV back, although their mechanical strength is not as good as metal rivets (shear strength of about 50 MPa), but enough to meet the low load requirements.
Open mouth rivets: Open mouth rivets are suitable for interior fixing in the automotive industry. When riveted, the tail of the rivet will unfold outward into a petal shape, providing a larger contact area and stronger fixing force. 5056 aluminum alloy made of open rivets, can provide about 350 MPa shear strength and about 490 MPa tensile strength.
Shear and tensile strength
The 2024 aluminum alloy rivets commonly used in aviation and automotive manufacturing have a shear strength of 270-325 MPa, while the tensile strength can reach 470-505 MPa. This high strength makes 2024 aluminum rivets particularly suitable for structural parts that withstand high dynamic loads, such as aircraft wings and body frames.
316 stainless steel rivets are commonly used in Marine engineering and chemical industry, and its shear strength is about 450 MPa and tensile strength is 550 MPa. The rivets are suitable for the fixing and assembly of ships, offshore platforms and chemical equipment in highly corrosive environments, ensuring long-term durability and low maintenance costs.
A common titanium alloy rivet (such as Ti-6Al-4V) has a shear strength of 600 MPa and a tensile strength of 900 MPa. Titanium rivets are particularly suitable for applications requiring extremely high performance, such as critical connection parts for aircraft engines and spacecraft.
Copper rivets are commonly used in the electronics and electrical industry because of their good conductivity and thermal conductivity. A typical copper rivet may have a shear strength of 300 MPa and a tensile strength of 360 MPa. In construction and heavy machinery, the shear strength of high-strength steel rivets (such as structural steel rivets) can reach 485 MPa and the tensile strength can reach 640 MPa.