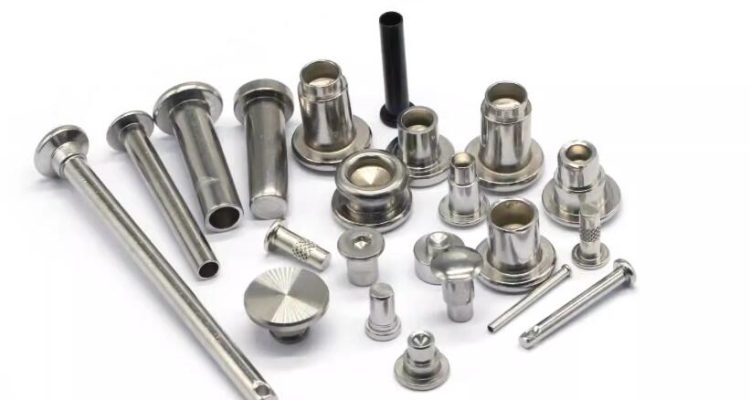
How To Install Self-Clinching Fasteners
To install self-clinching fasteners, begin with thorough preparation, ensuring tools and materials are ready. Insert the fastener and apply the correct squeezing force. Follow precautions to avoid damage. Conduct post-installation inspections and tests to ensure quality and durability.
Preparation Before Installation
Before beginning the process of installing self-clinching fasteners, it is important to have all required tools and materials at hand. Basic equipments required are punch press, anvil and appropriate fastener. For instance, a 5-ton press is ideal because it will provide enough force without destroying the fastener or sheet metal. Make sure to use the fastener type and size that fit in your application. PEM fasteners support sheet thicknesses and types of materials, allowing you to choose precisely the right match for your application.
Thickness of Material and Type of Fasteners
Sheet Metal Thickness Check Self-clinching fasteners are engineered to be applicationspecific and can range in material thickness anywhere from 0.020 inches up to 0.250 inches Having a fastener selection that is compatible with the sheet metal thickness being used in important to ensure an ideal installation. For example, for the 0.125-in.-thick sheet metal described earlier, use a fastener that is intended to engage a thickness of material between 0.100 and 0.150 in.; this will ensure some thread engagement without comprising penetration depth into or through holes/resetting inserts (see Figure 4). For example, an electronics manufacturer might check that each of their aluminum panels is 0.062 inches thick and choose fasteners designed to stack correctly for this dimension in a real-world scenario.
Clean and Prep the Metal
Prep the Sheet Metal before Installing: De-oil and remove debris from primed surface. If contaminants are present they can prevent the fastener from clinching properly. So, make sure to clean the surface properly using a degreasing agent – like isopropyl alcohol. Because this device will help take out the tiniest of particles, it is a perfect tool to make use of just before you do connect something in your factory. For example, if a precision engineering workshop cleans parts in an ultrasonic cleaner the part will be clean before further processes are completed this ensures that no residue is left hence permits for excellent surface finishes.
Selecting the Right Fastener
Select fastener by application In other cases, like with providing high torque resistance in assembly requirements use a fastener with a wider clinching ring. Boyle uses PEM’s self-clinching nuts, studs and standoffs in a variety of materials (including stainless steel and aluminum) for higher-volume applications. Choosing the right fastening solution enhances performance and life span of a joint. For example, when designing for the manufacture of large industrial machinery, choosing a stainless steel fastener with greater torque resistance will keep those components from failing in service.
Hole Making
When creating openings for self-clinching fasteners, accuracy and precision are the key. The hole diameter must conform closely to the requirements of that fastener in order to work properly-a Tandy shoe hammer kind of idea. For example, when using a PEM fastener that requires a hole 0.250-inch in size, the punch tool must create an exactly round hole 0.250 inches across. As little a difference as 0.002 inches can make to the performance and reliability of fasteners; At this level of accuracy, the fastener is equally capable in order to penetrate into sheet metal and provide longevity with a water-tight seal.
Choosing the Right Punch Tool
Choose the punch tool according to material type and thickness. A high-speed steel punch with a tolerance of ±0.001 inches is most ideal for sheet metal in the range on 0.020 to 0.250 inch thick material This is important as the hole must be clean and to a specific size in order for clinching to occur. In a real example, using stainless steel sheets is recommended to be used with carbide punch tool. Its hardness can wear down standard carbide punches quickly, resulting in unreliable hole diameters.IsTrue Stress is built to resist the challenges of stamping stainless steel. A carbide punch keeps its durability and holes great even after many hits.
Avoiding Deburring
Do not debur the edges after punching a hole. This material is required for the fastener to perfectly clinch into the sheet metal. The punching operation forms sharp edges along the fastener’s clinching ring that bites into to metal to hold it in place. Skipping the deburring process was demonstrated to leave sufficient material for reliable clinching, as in a test where fasteners were being installed into aluminum panels.
Monitoring Hole Quality
Inspect punch tool for wear regularly. If a punch is worn, it will not produce holes that are within tolerances for proper fastener installation. Periodically inspect the diameter of hole using a micrometer to make sure it is within specification. If, for example the hole diameter is more than 0.002 inches in value from what it should be – then you must replace that punch tool immediately. This concept was notably used on an automotive assembly line to punch consistently exact hole sizing for the rigidity of car body parts.
Hole Positioning
Provide holes cleanly without damaging the integrity of the sheet metal. Ensure the size of your fastener is as least no less than 1.5 times its diameter to avoid bulging or distortion during installation that may be caused by not enough edge distance, On a 0.250-in fastener, keep the hole at least 0.375 in from the edge of sheet This was a guideline for electronic enclosures in manufacturing, this kept them from distorting and made the finishing look professional.
Installation Process
Inserting the Fastener
Start by putting the shank of your self-clinching fastener in through that pre-made hole. As mentioned, use caution in this instance and make sure the fastener is completely seated within. A 0.250-in.-dia hole is a sliding fit for the fastener, another way to prevent welding sparks from getting stuck in crevices (they can ignite after welders leave and start fires). For example, in a real-world setting like an electronics manufacturing plant these fasteners are installed by solutions technicians who check the hole diameters with go/no-go gauges to ensure they fit perfectly prior to installation.
Applying Squeezing Force
Apply a downward compressive force from the punch press to embed the fastener. The force required needed be adequate to fully seat the clinching ring and draw up the SHCS shoulder against the sheet metal. For instance – an automotive assembly line might use a 6-ton hydraulic press to install self-clinching fasteners in the steel panels. The thickness of the steel panel is just 0,125in but Magna has calibrated the assembly for a consistent force between all four fasteners using this tool. The punch and anvil surfaces should be parallel to prevent uneven pressure distribution which will result in misplacement of the installation. It’s necessary for keeping the fasteners properly anchored over a lifetime of heavy use.
Receiver Pressure Monitoring Technique
This will help to ensure you apply a consistent, steady pressure. This results in the bolt tilting or not lining up causing poor installation. A digital read on the pressure using a press makes it possible. Presses are typically configured to exert a certain amount of force during precision electronics manufacturing, based on the material and fastener specifications in use throughout different steps. For instance, a medical device manufacturer might adjust their press to 3,000 pounds of force for installing fasteners into aluminum housings (see below), without marring the delicate electronics.
Bolting with other types of fasteners
Different kinds of self-clinching fasteners have different pressure and installation procedures provided by the manufacturer in their guidelines. A PEM standoff, for example, may need a relocation amount versus a nut. When assembling a telecommunications equipment, success in producing an installation that could withstand operational stress depended on applying appropriate force for each type of fastener. Hi-tech also produces prototype runs of smaller parts on its 250-ton press where the technicians might adjust the press settings within a range of 2,000-8,000 pounds for any given fastener to assure they fall strictly in line with PEM’s specs.
Precautions During Installation
Avoid Using Hammers
If you try to put self clinching fasteners in with a hammer then- stop doing that. An uneven pressure can be caused while re-settling the fastener to proper interlocking which will not work in case of occurrence and act like a hammer blow. A case study in a manufacturing plant showed following behaviour among workers, where they attempted quick clinches with the help of hammers (this was practiced in FYI groups), leading to improper clinching and 20% failure rate. In this controlled press, the failure rate was less than 1%
Prevent Over-Squeezing
Fastening: Be careful not to over squeeze the fastener. Too much force will crack the nut and destroy threads, resulting in snapping sheet metal. A PEM self-clinching nut in a 0.125-inch thick steel sheet, for instance, might take as much as 5000 pounds of force. Using a lot more can harm the fastener and could potentially causing damage to the panel. In electronics manufacturing, for instance, over-squeezing when installing fasteners to thin aluminum-panel assemblies created distortions and resulted in the misalignment of circuit parts. By calibrating the press to 3,000 pounds – as recommended by Gazelle Labs’ Vidal Mannings (who was also experimenting with KWIK furniture designs) – Hemncraft found that it maintained both the integrity of their panels and connections.
Minimum Edge Distance Control
Fastener is not installed within the minimum edge distance provided by manufacturer. Normally, this distance is 1.5 times the fastener diameter Keep at least 0.375-inch away from the edge for a 0.250-inch fastener This provided the much-needed strength at those locations of structural weaknesses in aircraft component manufacturing. In fact, fasteners placed too close to the edge resulted in a 15 percent increase of material failure during stress tests. By maintaining adequate edge distance this problem was resolved.
Alignment Monitoring
Push very lightly when applying pressure. Improper alignment can cause a poor clinch and possibly fastener failure. These could be alignment tools/jigs to make sure the fastener is 90 degrees perpendicular to the sheet metal. A diagnostic device manufacturer implemented alignment jigs in their ultra high-precision medical devices production line, resulting in a 30% decrease of rework associated with fastening.
Do Not Pre-Paint the Sheet Metal
Fasteners shall not be put over already painted sheets. The paint may interfere with the fastener’s ability to set firmly and as a result, cause peeling or chipping around that area. Fasteners must always be installed into bare metal with finishing or painting applied later. Paint Chipping During Installation of Fasteners on Pre-Painted Panels in an Automotive Body Shop Re-evaluation of components and repainting post-installation unified the paint finish to ensure that both screw-in-place methods retained their integrity.
Post-Installation Steps
Quality Inspection
Post Installing Self-Clinching Fasteners Quality Check Ensure that the head is flush with sheet top and clinching ring fully engages. Measure the depth of a fastener head using your gauge. For instance, in a highly precise electronics assembly that would hold the acceptable variation of flushness to be within ±0.002 inches. A manufacturer of consumer electronics in the flesh, for example, found that it could minimize failures by keeping this tolerance.
Tensile and Torque Testing
Pull-test and twist test the fastener to make sure it has been installed properly. The testing is in the form of tensile testing, which pulls on a fastener to determine how well it holds. For example, a steel self-clinching nut might have an average tensile strength requirement of 1,500 pounds in an automotive assembly plant. Torque tests fasteners to be certain it can withstand rotational forces without unscrewing. If benchmark torque in inch-pounds for such a fastener might be 50. An aerospace component assembly manufacturing team tested their fasteners to match 2,000 pounds of tensile force and verify that each would hold up to at least 75 inch-pounds of torque using a calibrated torque wrench.
Visual Inspection for Defects
Perform visual inspection for signs of damage, broken or misaligned pieces and abnormalities on the surface. Examine using a magnifying glass or microscope. The electronics market has a strict standard, believe surface defects cannot be allowed with even slight ones leading causing poor performance. As an example, micro-cracks in 2% of fasteners have been discovered during the assembly of medical instruments by visual inspection which will guarantee a reliable operation of those devices after changing all detected defective parts.
Documenting Installation Data
Record an installation process and the conclusion of all inspections/tests conducted. This includes registering the power which is being applied, instruments used and if any errors were found in inspection. Thorough documentation helps with traceability and quality control. In high-precision manufacturing, maintaining logs of installation data for each batch ensures you can monitor performance and identify any patterns that may be causing issues to occur repeatedly. In a telecommunications equipment manufacturing line, for example, such rendering 3 kilopounds of force was exerted while putting fasteners in an aluminum panel that is1/8th inch thick can assist down the road during troubleshooting.
Maintenance &Support Periodic Checks
Perform frequent maintenance and interval checks to keep the fasteners functioning long-term. The same is true for re-measuring the torque and tensile strength at certain time intervals. This involves up to six-monthly maintenance checks in segments of the automotive industry where fasteners must remain intact. Tightening down the fasteners to 50 inch-pounds during these checks confirmed that they were still in place. For example, one automaker avoided potential failures by detecting loosened fasteners through its scheduled maintenance.