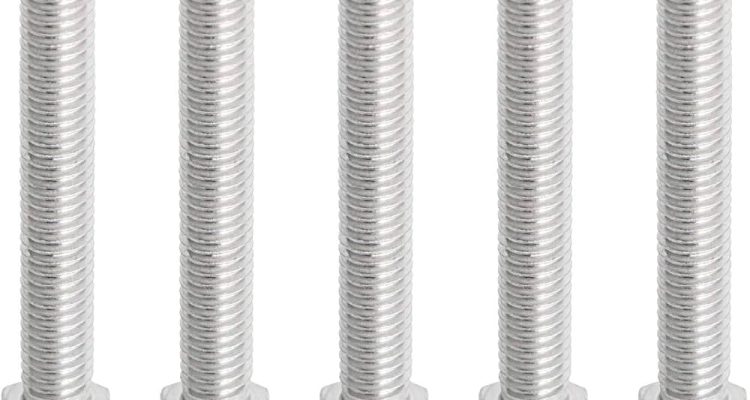
How to customize fasteners for unique requirements
Customize fasteners by selecting materials for strength, using 3D printing for prototypes, applying specialized coatings, and testing under actual conditions for optimal performance.
目录
ToggleChoosing the Right Materials and Application
-
Customizing fasteners for specific demands
Material apposite
When fabricating fasteners for specific application, it is essential to determine the most suitable material. Material choice is influenced by the unique requirements of the application, such as the temperature it will be exposed to, the strength, the corrosion resistance, and the cost. For example, titanium fasteners do well in aerospace applications because of their strength to weight ratio and their excellent resistance to corrosion . They can stand heat levels of up to 600° without losing their strength. This makes them ideal for engine components, where the ability to withstand high temperature is critical.
Designing for harsh condition
Where fasteners are designed for harsh environmental conditions, some requisite adjustment are made in their design. For instance, putting a coating of zinc on the fasteners or basing them with a cadmium plating material can make it highly resistant to caustic environments, such as salt water . The zinc coating process is called galvanizing and it slows the corrosion processes by preventing moisture from coming into u contact with the fastener, thus prevents rusting.
Improving production mechanisms
The modern 3D printing technique has revolutionized the manner in which custom fasteners are made. It provides a unique prototyping feature, which allows precise modeling. Since fasteners are typically relegated to holding material together mechanically, the 3D printing technology can help in crafting unique shapes that are normally too tasking or expensive to manufacture. For instance, a company may design a custom bolt with a non-standard arch or curve to dovetail it in a unique space between two pieces of a machine. Here, the precise curve of the bolt can distribute the load optimally using a precisely printed part.
Testing and quality controls
When designing fasteners for demanding conditions, it is compulsory to implement a rigorous testing regime. Numerous tests are performed to ensure they meet the specific requirements. For instance, tensile tests can be carried out to determine the loading threshold the fastener can withstand before destruction. A bolt meant for construction, for example, can withstand tensile stress of up to 100,000 psi, which will ensure the bolt will not break when the structure is exposed to the highest load. Other fasteners are subjected to mandatory commands, such as measuring their temperature or preventing them from coming into contact with water. Others are rigidly tested. Fasteners can also be passed through non-destructive tests. After passing the test, the quality of the prototype or the batch is approved, before the fasteners are produced in bulk.
Functionality
Modern technology implements the use of Radio Frequency Identification (RFID) technology on fasteners. It helps monitor the inventory but also assist in organizing scheduled maintenance regime. A good example is when used in fastening the critical engine parts in an automotive. Such assemblies can be appended with unique idents, which are tagged in the vehicles system. Such technology shows the health of the fastener and well as warnings of immanent failures that necessitate service.
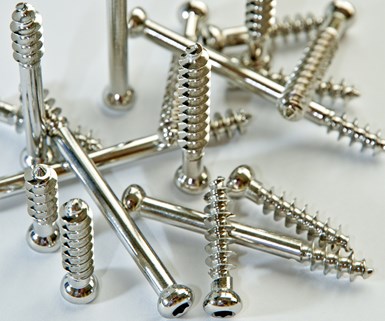
Medical Screw Solution Include
Length Requirement
The ability to tailor the length of a fastener as needed is especially beneficial in the case of unusually long or short applications for which conventional sizes lack in. However, it also allows for improved precision in length, which is an important factor for proper fit and function in any case, but especially for specialized machinery or aerospace applications, where every millimeter of length can mean the whole system. Thus, the specialty customization process for fastener length is as follows:
Defining the Exact Length Required
The process initiates with the evaluation of the joint or assembly. Engineers measure the required length robustly using special tools to ensure that the fastener will go through the materials at a depth sufficient to hold them together while not extending farther than necessary. For example, a custom fastener with the exact length of 23.5mm may be necessary to secure the cover of the electric compartment in the aircraft.
Custom Production Process
The manufacturing process itself may rely on “cutting a longer product to a more suitable length” or creating the fastener from scratch . In either case, a company would likely use special tools to cut the fastener using a CNC machine to ensure the highest level of precision. A cutting tool and a threading tool would be used to reach the respective results.
Material Choice
The choice of material is a critical element, as not all materials could sustain alteration without significant loss of their mechanical properties. As a result, stainless steel would be suitable for the process, as its capabilities would remain even after the cutting tools are used on it. High-grade steel in non-standard fasteners would ensure greater corrosion and mechanical resistance in the customer’s application.
Testing and Assuring the Quality
Finally, every fastener would undergo testing to ensure that it works as required. For example, a load test would prove that a fastener of an unconventional length of, in the example, 23.5 mm, would get break along with that length. Undoubtedly, such testing is especially important for applications like construction in which a breakage might result in significant hazards.
Meeting Load Requirements
A crucial aspect processes of designing fasteners in construction and aerospace is their application meeting the load standard. The very previous steps include understanding and meeting the load specifications.
Analysis of Load Specifications
Firstly, the needed load specifications to accommodate a certain range of loads should be defined. To this end, one will typically consult with engineers and seek to understand the maximum forces in tension or shear the fastener will be subjected to. For example, if the fastener is used in bridges, the tensile force might be estimated as 50,000 pounds, and the shear forces as 30,000 pounds.
Material selection
It is also important to choose the apt material to meet the load specifications when designing fasteners. For example, one can choose grade 5 titanium since it has a very high tensile strength of up to 150,000 psi . Hence it is appropriate for meeting the established load standards in bridge constructions. Since fasteners of these uses are often outdoors, especially in corrosive environments related to weather, this high corrosion resistance of up to tens of thousands of hours will not be an excessive advantage.
Engineering the Fastener
When the load specifications are studied and materials are decided upon, one will have to develop the fastener itself. This will include deciding its needed outer diameter, thread count, and length in order to distribute the load across the length of the fastener most efficiently. CAD can be used to engineer the design of a fastener and construct 3D models of it to check their properties and see how they will be working when manufactured.
Prototyping
The design is then sent to be prototyped. Afterward, it will be tested to see if the effects of the load comply with the needed specifications. The real tests will be usually emulated to work in ideal conditions, and the force or the pressure used, plus more is multiplied by safety factors were defied. If the prototyped fastener falls short, the result will be taken to the phase of reiterating the design in the direction pointed by the results.
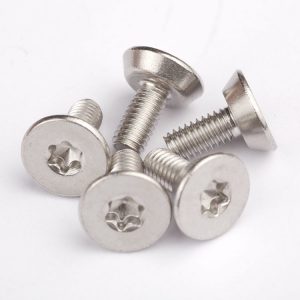
M4 Screws Custom Made
Balancing Resistance and Strength
Producing fasteners that are perfectly balanced against environmental factors and mechanical strength is vital for their applications in harsh conditions. It determines the right choice in terms of materials and design.
Choosing the Material
The initial step is to understand what the fastener will be exposed to. For marine applications, high-grade stainless steel, like 316, is the best option. This is because it has the best resistance to the conditions found in saltwater. However, this has to be achieved without compromising its tensile strength, which often has to be above 70,000 psi.
Engineering It
The next step is the engineering of the fastener, which includes attempts to improve both its chemical and physical properties. For example, adding molybdenum makes the alloys more resistant to corrosion. However, the heat treatment can also be applied to improve tensile strength. FEA allows us to see exactly how the screws such as these below will respond to any given load or condition they are exposed to.
Coating It
Alternatively, coatings can be applied afterwards . The most durable way to do it is through the use of electroplating or thermal spraying. The application of such materials as zinc or aluminum, when properly done, can result in trinity of service life. The fastener will no longer be prone to oxidative damage, but its capacity to bear the load will not be affected, either.
Testing It
Finally, testing has to be performed in conditions that are as real as possible. For the type of screw discussed in this paper, the testing applied includes cyclic salt spray combined with load testing on the columns. It can approximate the experience of a year in a marine atmosphere, and determine that the screw will be capable of withstanding both the intensity of the weather and the physical load it can take for fifty years.
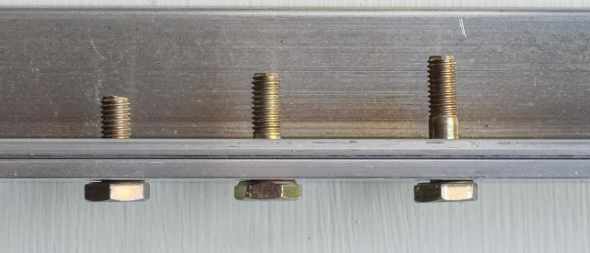
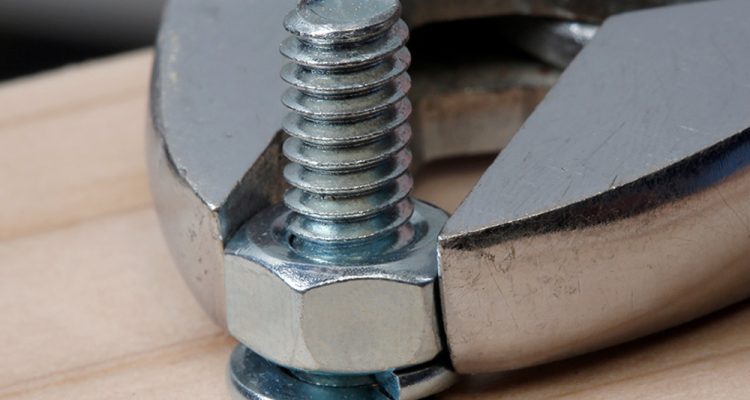
How To Correctly Install Self-Locking Nuts
To properly ins…
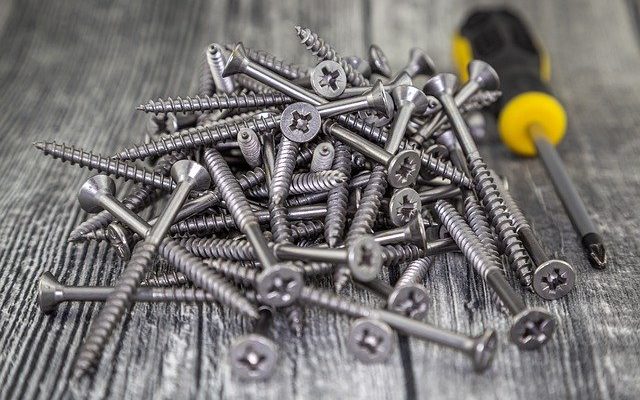
How Manufacturers Produce Plastic Nuts And Bolts
Manufacturers c…