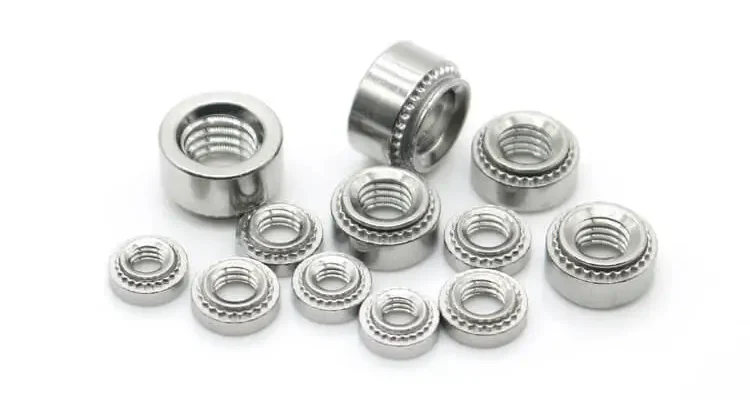
Differences Between Self-Clinching Fasteners and Welding
Self-clinching fasteners offer superior strength, easier installation, lower costs, and greater versatility compared to welding. They provide consistent durability, are compatible with various metals and thicknesses, and require less skilled labor, making them ideal for diverse industrial applications.
Load Capacity
- Self-clinching fasteners deliver more load carrying capability. As an example, self-clinching studs can bear loads to 1,000 pounds in steel panels as thin as 1mm that Tip Togs (www.tiptogs.com) uses for its electronic motorsports toe-links assignments. The fastener is securely locked in place during installation through the cold flow process, which provides excellent load distribution. This method avoid stress concentrations and possible failure nodes.
- It may also be added that welding can have vastly different load capacity depending on the technique and skill of welder. This is enough to carry 800-1200 pounds for a set of similar materials with a properly completed MIG weld. But welding is not always a perfect join-based process. As much as 30% of the load rating on a machine may be lost due to substandard or incorrect practice.
Here’s a comparison of the load capacities for different fasteners and welding techniques:
Fastener/Weld Type | Material Thickness | Load Capacity (pounds) |
---|---|---|
Self-clinching Stud | 1mm Steel | Up to 1,000 |
Self-clinching Nut | 1mm Aluminum | Up to 900 |
MIG Weld | 1mm Steel | 800 – 1,200 |
TIG Weld | 1mm Aluminum | 700 – 1,100 |
Long-term Reliability
Such fasteners retain good strength and structural integrity due to self-clinching. For aerospace applications, these fasteners retain 95% of their original strength after 10,000 flight hours. Durability becomes quite crucial in any prospective application for the long term, since reliability is essential.
Thermal cycling along with stress concentrations at the weld seams degradate welded joints. Welded steel structures subjected to cyclical loading may lose as much as 20% of their functionality following 2000h operations. These microcracks and stress risers are typically due to poor welding conditions which develop along long-term use.
Environmental factors are resistant to
- Self-Clinching Fasteners are resistant to environmental factors such as corrosion and moisture. But stainless steel fasteners or those with anti-corrosive coatings last well in severe conditions without degrading. A stainless steel self-clinching nut, for instance, will stand salt spray tests in the higher hundreds of hours before forming white and red rust at least.
- Corrosion Welded joints are especially vulnerable to corrosion, due primarily to the possibility that welding may alter material properties around joint areas. Welds must be protected and coated to guard against rusting in the aggressive marine environment. Welds that are improperly protected may exhibit corrosion with 100 hours of salt spray exposure.
Here’s a comparison of environmental resistance:
Fastener/Weld Type | Test Condition | Duration (hours) |
---|---|---|
Self-clinching Nut | Salt Spray | 1,000+ |
Self-clinching Stud | Humidity Chamber | 1,200+ |
MIG Weld (Protected) | Salt Spray | 500 |
MIG Weld (Unprotected) | Salt Spray | 100 |
Automotive Industry
Self-clinching fasteners are quite different than welding in the automotive industry. One top OEM realized a 30% improved on their assembly time just in installation of chassis components from welding to self-clinching fasteners! Use of the switch not only cut installation time but made the cars more structurally sound.
Installation Process
Steps for Installing Self-Clinching Fasteners
- Add a Hole: Make an unadorned circular hole at the center of the metal panel where you will insert your fastening device. The diameter of this hole needs to correspond with the size of fastener you are using. This means a 5mm stud will work best with a 5.2mm hole etc. The hole must be +/- 0,1 millimetres machined to work as designed.
- Install the Fastener: carefully align self-clinching fastener with hole and install. It can cause the fastener to fail or weaken Before putting pressure on the fastener, it is important that you make sure your screw or bolt looks rightly centered in opposition to the top of a panel.
- Put It in a Parallel-Acting Press: Give it steady pressure with a press that acts parallel to the direction on work. This varies with fastener size and material but the amount of force required is different. Extrapolate that out to, for example a 5mm stud into just a 1m thick steel panel and we need about 3000 lbs of force. Under pressure, the metal around the hole cold flows into this undercut of a fastener and it is forever tightened in place.
- Force Requirement: Approximately 1,500 pounds of forces will be needed for a 3mm stud in.5- thick aluminum Friction stir welding 10mm stud into 2mm thick stainless might require as much effort as up to ten thousand pounds of force!
- Press Type: Generally hydraulic or pneumatic-but with the option of adjustable pressure settings to adapt for various fastener sizes and materials.
Methods and Procedures Used in Welding
- SURFACES (PREP): Carefully, prepare the metal surfaces to rid them of impurities that could cause contamination in your weld. Most of the time this includes sanding, grinding or chemical cleaning. Depending on the size and condition of the metal, surface prep can charge 10-20 minutes each part.
- Locate Parts: Accurately position parts for welding. It may have adequate tools for clamping to hold the components in place while welding. The positioner and clamping, in general can consume 5 to 15 minutes (see Fig. ) or more with complex assemblies as a function of the calendar downtime needed for changing hands.
- Weld the Joint: Based on material and thickness select your preferred welding method (MIG, TIG or Spot) For instance:
- MIG Welding- Works for thicker stuff (1.5mm to 10mm). Uses settings of 18-22 volts and a wire feed speed range from 200 to 300 inches per minute. Multiple beads per weld, 30-60 seconds/weld
- TIG Welding: Delivers precise control over joints and works well for thinner than 0.5mm -2 inch thick materials (1/16 inch to /4 ). Normally runs on 15-20 amps Welding happens at 1 to 2 minutes per weld which can be time consuming due to the extreme accuracy required.
- Spot welding – Used for thin sheet metals (such as 3mm) One spot weld is done in 1-2 seconds but the initial setup and alignment can be time consuming.
- Post-processing: Following welding, remove all slag, spatter and oxidation. This might require the use of wire brushing or grinding in other areas where welding has been carried out so they have a smooth clean finish. The cleaning and finishing of a single part may need 10 to about 30 minutes, this being dependent on how grand or sophisticated the weld was.
Cost Analysis
Initial Costs
- Initial costs to use self-clinching fasteners are usually lower than welding. Your average self-clinching stud? about 0.50 each The one-time costs for the tools needed to install it (a hydraulic or pneumatic press, shown above) are somewhere in the ballpark of $5-10,000. The presses have low maintenance costs, typically $1,000 per year or less.
- A good MIG welder setup will run you $2,000-5,000 and even more than $10K for professional use in industrial applications. Welding supplies and consumables like electrodes, gas and safety equipment are also ongoing expenses. One spool of MIG wire is about $50, a bottle of shielding gas runs for $200. These are consumable items that periodically have to be replaced, which ups the bill even higher.
Labor Costs
- In general, a worker can install 500 self-clinching fasteners every hour. Installation labor costs are about $20 per hour, so that works out to be only $.04 / fastener.
- The process of welding was slower, since a welder can perform 20 to 30 weld per hour. At a slower rate, it can cost $1 to $2 per weld.
Energy Consumption
- A hydraulic press, for example, consumes about 2 kWh an hour and amounts to $0.20 per hour at a typical electricity rate of just under $0.10/kWh.. This effectively drives down average energy cost per fastener to-wait for it… $0.0004
- On the other hand welding, especially MIG and TIG based one use significantly low energy. MIG welding consumes 4-10 kWh per hour. This costs between only $0.40 to a few dollars per hour at an average rate of 10 cents, kWh.) As welding is slower, the energy cost per weld can vary from $0.02 to $0.05.
Total Cost Per Unit
- Taken together, these factors add up to a significantly lower total cost per part for self-clinching fasteners. This brings the total cost per self-clinching fastener, including acquisition costs for said product along with average labor and energy to install it to be about $0.55 each ago.minimum.guna;
- The total cost per weld,which covers labor and energy makes the range of $1.50 to $3 for welding This marked difference makes self-clinching fasteners a more cost-effective option across the board for most applications.
A Case Study in Electronics Manufacturing
One firm in the electronics manufacturing sector highlights significant cost reductions by moving from welding to self-clinching fasteners. Historically, their chassis assembly welding process was costing them about $50k annually in labor and materials. Switching to self-clinching fasteners saved the manufacturer 60% in assembly costs, bringing its annual cost down from $50,000 a year with rivets and nuts (and no cookies) to just $20,000. Additionally the quicker installation time improved production efficiency to help meet higher demand while still keeping labor costs down.
Versatility And Availability
The Different Types of Metals and Compatible Thicknesses
- These fasteners are truly versatile and can be installed in a variety of metals and thicknesses. Fasteners:These can be used on an aluminum, steel, stainless and few malleable metals such as copper and brass etc. While they can reliably demonstrate their effectiveness in even the thinnest sheet metal at 0.20mm (0.008 inches), thicker materials up to several millimeters are also no problem for truly sharp lasers, such as those found in ByStar Fiber models. This vastly scales down the uses of self-clinching fasteners and through its broad compatibility, even in applications for a wide range of industries including electronics, automotive, aerospace etc.
- In the last process, metals are combi ned based on similar properties to obtain welded material however due thermal expansions and contractions, failing weld joints can exist or even depending on heating temperatures warping. It is really hard to weld thin materials (less than 1mm) without burning the material because of how much heat it will generate. Welding is not as flexible since it can no longer be used on applications that are made up of other types and thicknesses of metal.
Ease of Use and Accessibility
- Self-clinching fasteners are easy to install and do not require special training in the manufacturing process. The procedure includes the drilling of holes, insertion of fastener and pressure to hold them. A $5,000 to $10,000 hydraulic or pneumatic press may be used and the assembly can clamp together in 5-seconds per fastener. This versatility allows self-clinching fasteners to be used in nearly any shop or manufacturing setting.
- This job, by contrast is difficult and takes extensive training which the demand for welders conflicts with. High Quality Welders (Certified) are also needed as welds must be approved for quality and these cans start earning $$$ from $25/hr to over $40/hour. Welding is a multi-step process and includes surface preparation, set-up of the position readied for welding as well as the weld itself achieved with accurate execution at every step. In addition, welding equipment – which can cost anywhere from $2,000 to $10,000 and beyond – is more intricate in nature and needs regular maintenance as well as calibration.
Availability in the Market
- Self-clinching fasteners are these fixtures which can be discovered in nuts, studs or standoffs, panel and so on. According to industry experts and top producers like PennEngineering, Southco etc., millions of these fasteners are produced every year because they have the simplicity that industrial needs. PennEngineering’s PEM® brand, for example produces more than 5,000 self-clinching fastener variations to fit a wider range of thicknesses and materials.
- Welding supplies however can be less routinely available, especially for specific materials or consumables. Welding rods, wires and shielding gases require procurement and stocking carry out bulk buying for ensuring continuity in production. This inconsistency can again be due to the quality of welding consumables and some brands may offer non-performing alternatives than their other specifications.
Application Flexibility
- The self-clinching fasteners are constructed to have the versatility for a wide range of uses. This is a great asset in applications where the finish of end products holds prime importance and you want them installed easily without causing damage to that surface. An example would be the electronics industry; where self-clinching fasteners help in assembly so that enclosures and chassis can stay free from piercings of surface coatings while retaining functionality as well as full look.
- Welding, on the other hand, does have its own list of issues when trying to bond pre-finished material(s). However, the elevated temperatures used during welding can degrade surface coatings that must be refinished and repainted after a weld. This introduces extra layers and stages of friction in the manufacturing process, making welding inefficient for aesthetics-focused mechanisms.