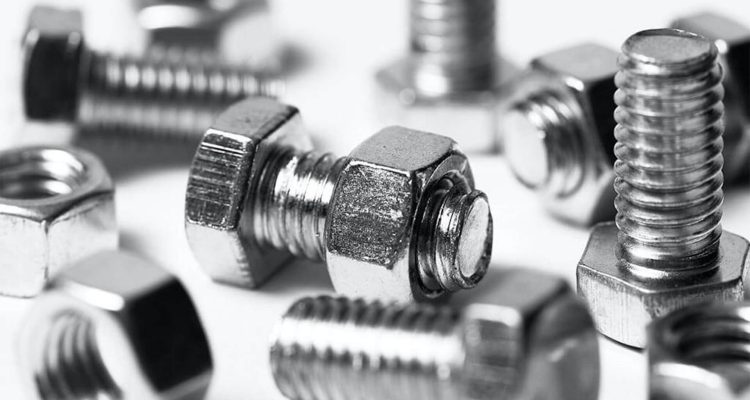
What grade bolt is best for shear strength
For optimal shear strength, grade 8 bolts are recommended due to their tensile strength of 150,000 psi and yield strength of 130,000 psi. In applications like structural connections, ensure to torque grade 8 bolts to 100-120 foot-pounds for maximum effectiveness, enabling them to handle shear loads exceeding 12,000 pounds per bolt.
Bolt Grades Explained
Bolt grades have a great influence on both the shear strength and performance of an application. For example, grade 2 bolts have a tensile strength of around 60,000 psi, which may just be OK for lighter applications where they would fasten furniture or appliances. These are unsuitable for high-stress situations. A grade 5 bolt offers a tensile strength of 100,000 psi, making them perfect for automotive components in medium-duty applications where the connecting of vehicle frames is crucial in relation to safety and structural integrity.
Grade 8 bolts are primarily used in those applications where high shear strength is in demand. These bolts possess a tensile strength of 150,000 psi and yield strength of 130,000 psi. The most common uses of these are heavy machinery, construction, and aerospace. A construction involving, for example, 1,000 grade 8 bolts can have a colossal bearing capacity that will assure steel beams and supports to bear more than 20,000 pounds each for safety in high-rise buildings and bridges.
Specialty grades, such as ASTM A325 and A490 bolts, serve specific applications. The minimum tensile strength of an ASTM A325 bolt is 120,000 psi, which makes these bolts ideal for structural steel connections in large construction projects. A typical high-rise building would have thousands of A325 bolts installed, with each bolt supporting more than 8,000 pounds of shear load.
Basics of Shear Strength
Shear strength refers to a material’s maximum load that can be supported prior to failing in shear. This is one of those material properties that becomes very important when forces act parallel to the surface of a material. For instance, steel normally possesses a shear strength of 50,000 to 70,000 psi, which depends on alloying and treatment. This becomes a very important strength in terms of construction, as most beams and columns have a shear force acting on them due to lateral loads such as wind or seismic forces.
Shear strength on bolts has many practical uses—because being aware of such strengths prevents catastrophic failure. As an example, the shear strength of a standard grade 5 bolt that has a tensile strength of 100,000 psi will be approximately 60,000 psi. With a grade 5 bolt in a structural connection, each bolt can handle roughly 5,000 pounds of shear load. In these constructions, when there are 200 grade 5 bolts to hold a steel beam, then this is about 1,200,000 pounds of shear capacity, being on the safe side from all kinds of prospective shear forces.
The design of the connection shall also depend on the type of load and configuration that the bolts have. For example, in the case of lap joints, the calculation for shear strength may differ from a bolt in single shear or a bolt in double shear. A bolt in double shear can resist effectively twice the shear force of a single shear. That would mean a grade 8 bolt with a shear strength of 120,000 psi supports about 12,000 pounds in conditions of double shear. These configurations enable the engineers to adequately design safe and effective connections in structural applications.
Moreover, the shear strength might also be altered by environmental factors. The shear strength of bolts can deteriorate at high temperature. For example, the shear strength of some types of steel at temperatures above 800°F reduces significantly, up to 30% of its normal value in some cases.
Grade 8 Advantages
Grade 8 bolts possess a significant advantage in high stress applications due to the great strength and durability they embody. With a minimum tensile strength of 150,000 psi, these bolts find their way into heavy-duty applications where failure cannot be an option. For example, a grade 8 bolt used in construction and industry can withstand shear loads of up to 12,000 pounds each, meaning the type of fastener is important in securing structural steel connections in buildings and bridges from large forces caused by wind and seismic activity.
Perhaps most noteworthy about grade 8 bolts is that they do not deform under load. The yield strength for grade 8 bolts is roughly 130,000 psi; these are the kinds of bolts that can support heavy loads without permanently deforming. In one word, this characteristic is important in the practice of manufacturing automobiles wherein the bolts are very well subjected to dynamic forces. For instance, with a grade 8 bolt to anchor suspension components, the connection will not come apart under forces of acceleration and deceleration, and cornering forces that often approach greater than 10,000 pounds.
What’s more, class 8.8 bolts are extremely resistant to fatigue, and because of that, they are great for applications with cyclic loading. For example, in aerospace and automotive industries, components often undergo repeated cycles of stresses. It has been determined that class 8.8 bolts can withstand over 100,000 loading cycles without significant fatigue failure. Such durability is really important in parts such as engine mounts or landing gear, where reliability is of utmost importance and bolt failure may lead to terrible consequences.
Another benefit is that grade 8 bolts are available in various sizes and coatings depending on the project. For instance, there are standard 1-inch diameter grade 8 bolts in all lengths from 1 inch to 10 inches, and even more. There are also coatings such as zinc plating or black oxide that can aid in resisting corrosion, especially for outdoor projects. Coated grade 8 bolts can give it very good service life, mostly over 20 years, whereas the uncoated bolts may fail due to corrosion in a couple of years.
Other High-Strength Options
While grade 8 bolts are known to be strong, there are indeed other high-strength options for specific applications and environmental conditions. Another good option is the ASTM A325 bolts, which find application in structural steel connections. These have a minimum tensile strength of 120,000 psi, hence suitable for heavy construction projects. For example, a skyscraper could have 500 A325 bolts in the structural framework of the building to resist shear of up to 8,000 pounds per bolt to provide stability from lateral loads such as wind.
Another high-strength option is ASTM A490 bolts. These bolts are much stronger, having a minimum tensile strength of 150,000 psi, just like grade 8 bolts. However, A490 bolts have specific advantages in certain environments. These bolts undergo some heat treatment and are mainly applied in structural purposes where the security of the connection is vital. For example, in the construction of a bridge, the normal configuration may use 300 A490 bolts which can handle shear forces as high as 10,000 pounds each, that way they will be ideal for critical connections of heavy traffic and weather conditions of structures.
In addition to ASTM specifications, high-strength steel bolts such as SAE J429 grade 5 and grade 8 are also excellent choices for various applications. Grade 5 bolts have a tensile strength of 100,000 psi and can be satisfactorily used in automotive and industrial settings. As such, 200 grade 5 bolts rated to take shear loads of approximately 5,000 pounds are enough for assembling a vehicle frame and fairly cheap. These are the kinds of bolts that occur in mid-range cars where performance and safety become important.
Choosing the Right Bolt
Selecting the right bolt will literally make any construction or mechanical job safe and durable. First, one considers the grade of the bolt, as in its tensile strength and shear capability. A standard grade 2 bolt has a tensile strength of approximately 60,000 psi and is suited for low-stress jobs such as assembling furniture. On the other hand, with a structural steel connection, it would be a different case whereby using a grade 8 bolt independent of 150,000 psi will be strong enough for heavy loads especially in seismic and high-wind areas.
Another important aspect is the diameter and type of thread the bolt will be. The diameter and length are related to the capacity of the load a bolt can bear. For example, an inch-diameter grade 8 bolt will have a capacity in shear at around 12,000 pounds, while the same grade of bolt with a ½-inch diameter may be able to support only 3,500 pounds. Moreover, the thread type – coarse or fine – can impact how good the bonding of materials will be. Finer threads are good for applications involving high stress; however, they are not suitable for applications requiring fast assembly or disassembly.
Environmental considerations also play a critical role in the selection of a bolt. For applications occurring in corrosive environments – such as marine or chemical processing – one must consider that the bolts should be made from corrosion-resistant materials. For example, although the tensile strength of a stainless steel bolt is only about 70,000 psi, it offers exceptional resistance to rust and corrosion. Under severe coastal exposure, it is possible to expect stainless steel or coated bolts to last upwards of 20-plus years versus a few years for standard carbon steel bolts, and thus even out the maintenance costs.
Application and Use
Bolts find their application in many industries, from construction to automotive and aerospace. For instance, in the construction industry, the common types of bolts used in joining structural steel elements are ASTM A325 bolts. The tensile strength for such bolts is at least 120,000 psi, hence very instrumental in making sure beams and girders in skyscrapers stay tight. One A325 bolt can usually resist around 8,000 pounds of shear load; hence, these are so important in high-rise buildings where the safety under dynamic loads such as wind and seismic activity becomes very crucial.
Grade 8 bolts are also useful in automotive industries for the development of highly crucial parts of the vehicle, such as suspension systems and engine mounts. The tensile strength of 150,000 psi stands them up against the very strong forces developed during driving. For example, the suspension system of an average car uses about 200 grade 8 bolts; these have to take a load of over 10,000 pounds when cornering and accelerating. They are this strong so that the vehicle will remain stable and safe on the road.
Aerospace applications also require special types of bolts that could deliver higher standards of safety and performance. For example, titanium bolts, such as those made of 160,000 psi tensile strength, are used in aircraft owing to their lightweight and strong texture. In commercial aircraft, thousands of these types of titanium bolts may be used in fuselage and wings. Their performance under extreme conditions of temperature and pressure changes becomes critical in relation to the safety of passengers.
Installation Tips
Installation is an indispensable aspect in the quest for peak performance and structural integrity of bolts. Among these, attaining correct torque upon installation is the most important. A grade 8 bolt takes on a torque of approximately 100 to 120 foot-pounds when mounted in heavy machinery applications. This level of torque is based on the principle that the bolt develops its full tensile strength without over-tightening, either causing failure in the bolt or stripping of threads. The use of a calibrated torque wrench assists in reaching the exact specification and prevents expensive errors.
The second most relevant factor concerns washers. A flat washer spreads the load over a larger area, reducing any potential damage to the connected materials. In highly stressed applications, such as in the structural connection of steel, this may be fortified through the use of a hardened washer in general. For example, the bearing capacity may be increased by about 30% using a hardened steel washer. For instance, consider beams being bolted in a building that must resist strong winds or earthquakes.
Before installation, threads of both the bolt and the nut should be clean and without any debris. Dirt can lead to improper seating and false torque readings. Actually, according to studies, as little as a small amount of dirt can reduce clamping force by as much as 25%, which might affect the integrity of the connection. Cleaning threads with a thread-cleaning tool or wire brush may fairly well prepare threads for a secure fit.