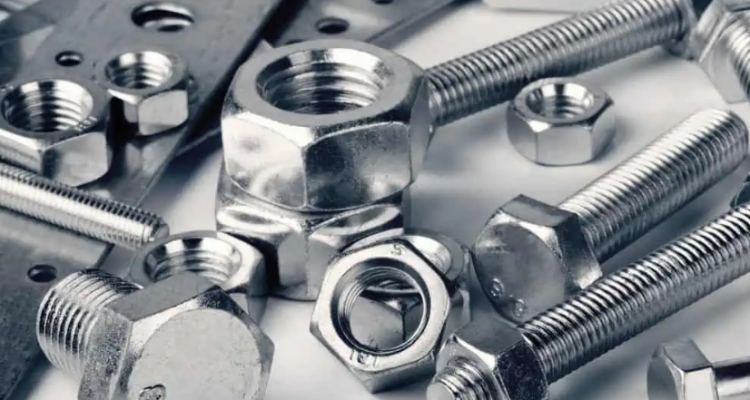
What are the 4 main types of threads used on fasteners
Uniform Thread Standard (UTS)
Uniform Thread Standard is a thread specification widely used in the U.S. market and covers many industries. The main features of UTS are measured in inches and fall into three main specifications: coarse, fine, and extra fine teeth. Application scenarios are quite huge: machinery manufacturing, automobile maintenance, and construction industries.
In mechanical manufacturing, there are many assemblies or fixations using UTS threads for various equipment. Medium strength connection parts often use common 3/8 “-16 threads, with a diameter of bolt 3/8″ and 16 threads per inch. Where higher strength is required in mechanical equipment, 1/2-inch to 13 threads are used for example, connectors holding large-diameter rotating shafts or supporting equipment. These larger threads can withstand higher torques by as much as 50%-60%, providing very welcome stability in a high-intensity operating environment. Smaller diameter threads, such as the 1/4″-20 threads, have found more usage in the assembling of precision equipment; their use allows space for flexible adjustment and can be put together very fast.
The use of UTS threads is pretty common in automotive repairs, with coarse threads, since they speed up repairs and provide sufficient strength. 5/16 inch-18 thread bolts are used in automotive chassis and suspension systems. This coarse thread maintains the stability of the bolt against high vibration and installation speed is about 25% to 30% faster than a fine tooth bolt. Where high-performance cars are concerned, such ultra-fine threads as 7/16 inch-24 thread could further enhance the accuracy and vibration resistance so crucial in the field of racing cars and high-performance engines that they could bear up against the strong vibration that a running engine goes through at 6,000 to 7,000 revolutions per minute.
UTS threads are commonly used in the construction industry for joining reinforcement bars and steel beams. Taking 5/8 “-11 thread, this type of coarse thread is extensively used for the fixation of steel beams and columns in high-rise buildings and withstands over 4,000 pounds of shear forces. If more precise fixation is involved, then in most of the places fine threads are used, such as 1/2 “-20 threads used in the steel cable connectors during bridge construction. Compared to coarse thread, such a thread could realize an improvement of 15%-20% in tensile strength and ensure stability in building structures under long-term load.
Carbon steel UTS threaded bolts are cheaper, can only be used in general indoor environments, the price is 30% to 40% lower than stainless steel bolts. However, in these cases of outdoor or high-corrosion environmental usages, stainless steel bolts are expected to outlast carbon steel, with an expected service life of more than 20 years, compared to only 10-12 years. In higher-performance requirements, the strength of titanium bolts can support higher strength, the weight lighter compared to conventional materials by 50%, and is often used in aerospace and highly valuable equipment, though at a price of three to five times higher compared to standard carbon steel bolts.
Apart from the selection of materials, the machining precision of threads also affects the service life and efficiency of UTS threads. For example, threads with high precision, such as H5 machining accuracy, can lower the friction loss during installation and prolong bolt service life, improving installation efficiency. Compared to ordinary-grade threads, the installation speed of high-precision threads can be 15%-20% faster, saving hundreds of hours of installation time in large-scale engineering projects and thus massively reducing labor costs.
Metric thread
Unlike the UTS, metric threads have been measured in millimeters and represent a basis of two types of measurement: diameter and pitch. Metric threads have been widely applied in machinery manufacturing for the assembly and fixing of various kinds of equipment. The popularly used M6×1 thread means that the diameter of the bolt is 6 mm and the pitch is 1 mm. M6 bolts have a high usage rate in light mechanical assembly for panel and bracket fastenings. M12×1.75 bolts are commonly used during the assembling of casings of heavy machines. Under tensile forces of over 5000 Newtons, these bolts easily maintain the stability of the equipment during high-intensity work. Metric thread uses smaller specifications during manufacturing, such as M2×0.4 bolts that can be used to fix very small parts with high machining accuracy for precision equipment watches and instruments.
These bolts of M8×1.25 are used in automotive engines and suspension systems, while the larger M14×2 bolts are intended for securing automotive hubs. They will have a design and build to handle over 10,000 Newton·m of torque so that the wheel is solid during driving. Threaded metric bolts range in diameter and pitch from M4 to M16 and beyond for various vehicle types and design requirements, serving the diverse assembly needs of everything from subcompact cars to large trucks.
Metric threads are widely used in the connection of steel structures. Common M20×2.5 bolts connect the steel beams with the supporting columns, providing a tensile force that can be as high as 150 kN under the action of external forces such as wind and earthquake. Fine threads such as M16×1.5 are usually used in a bridge cable connection which can give higher tensile strength above 100 kN owing to smaller thread spacing. Smaller diameter metric bolts such as M10 or M12 would be selected to install guardrail and protective mesh which may be sufficient for safety and more convenient for construction and installation.
M5×0.8 threaded bolts are often used in internal structures, including seat fixation and installation of electronic equipment. Such types of bolts are made from high-strength alloy steel or titanium alloy material whose tensile strength can reach as high as 1200 mpa, which is much higher than for ordinary bolts. They may also apply to external parts, such as the fixation of rocket casings and satellite antennas whose diameters range from M8 to M16. They may bear extreme variations of temperature and an aggressive environment.
There are many smaller specifications of bolts, such as M4 and M6 threads. Typically, a normal desk assembly used in an M6 bolt can withstand about 200 newtons of tension to make sure that the desktop is not easy to loosen while working on it. Metric bolts are in use to fix the housing and internal parts in the assembly of home appliances. Air conditioners make use of M8×1.25 bolts for the fixing of its outdoor frame so as not to be easily brought down by wind and rain.
British Standard Whitworth thread (BSW)
The British Standard Whitworth thread (BSW) is a thread standard invented by the British engineer Joseph Whitworth in the mid-19th century. This thread was one of the first standard threads in the world and was originally used in the steam engine and railway industries.
In the machinery manufacturing industry, the BSW thread is often used for the connection of large mechanical equipment. Take the 1/2 inch to 12BSW thread as an example, the pitch is 12 teeth per inch and the diameter is 1/2 inch. Bolts of this specification are used for fixing parts of heavy machinery equipment. Compared to metric or UTS threads, BSW threads have thicker screws, providing greater shock resistance and stability. In certain industrial equipment with frequent vibration, such as steam engines and older generators, the BSW thread can withstand greater torque and mechanical stress due to its thick screw construction. The tensile strength of the 1/2-12bSW thread can reach 6,000 LBF (26.7 kN), which is about 10% higher than the metric or UTS thread of the same size.
In the automotive industry, although the use of BSW threads has decreased, this thread standard is still retained in some older classic cars and motorcycles. For example, British cars produced in the early 20th century, classic Rolls-Royce and Morgan cars, used a large number of BSW threaded connectors in their body and engine components. 5/16 inch-18BSW threaded bolts are widely used for engine fastening and frame attachment on these older cars.
BSW thread has been widely used in the connection of steel structures, 3/4 inch -10BSW thread bolts for the connection of steel beams, can withstand more than 15,000 pounds of shear force (about 66.7 kN). When repairing some early 20th century Bridges, construction teams often needed to use 1-inch-8BSW bolts to match the original structural design.
In the field of Marine and Marine engineering, the BSW thread was also one of the major thread standards, especially in the early manufacture of steamships and warships. Due to the high corrosion in the Marine environment, BSW threads are usually made of high-strength alloy steel or brass to improve their corrosion resistance and tensile strength. A 1/4 inch -20BSW bolt made of brass has a tensile strength of 4,500 LBF (about 20 kN), while the same bolt made of stainless steel has a tensile strength of 7,000 LBF (about 31.1 kN).
Trapezoidal thread
Trapezoidal thread is a special type of thread with a trapezoidal cross-section that provides excellent load carrying capacity and is commonly found in lead screws, drive shafts, and transmission systems of industrial machinery. Take Tr20×4 trapezoidal thread as an example, where the nominal diameter of the thread is 20 mm and the pitch is 4 mm. This type of trapezoidal thread is commonly used in CNC machine tool feed systems and linear motion devices in industrial machinery. It has high transmission efficiency, is able to convert rotational motion into linear motion, and can withstand axial loads of up to 10,000 Newtons. Compared to traditional V-shaped threads, trapezoidal threads have a torque transfer efficiency of 15%-20% higher, less friction, lower wear rate, and longer service life.
Tr40×7 trapezoidal thread is commonly used in the lead screw drive system of injection molding machine. This thread can not only withstand high loads of more than 50,000 Newtons, but also maintain the stability of the drive during long periods of operation. Compared with the spherical thread, although the trapezoidal thread transmission efficiency is slightly lower (trapezoidal thread efficiency is about 30%-40%, while the spherical thread can reach 85-90%), but in the scenario requiring high load and long life, trapezoidal thread has greater stability and durability, especially suitable for high-speed heavy equipment.
Tr16×3 Trapezoidal threads are used in the design of car jacks to provide lifting power, and jacks using Tr16×3 trapezoidal threads can lift more than 2000 kg of weight at 500 Newton · m of torque. The self-locking performance of trapezoidal thread is better, which can prevent the equipment from slipping in the case of power failure or loss of control.
Thanks to its unique trapezoidal section design, the trapezoidal thread is able to better distribute stress and avoid stress concentration, which makes it maintain good performance in the environment of high temperature or drastic temperature changes. Tr25×5 trapezoidal thread is often used in cooling water valves of nuclear power plants. This thread can operate at high temperatures above 300°C and can withstand loads of 20,000 Newtons without deformation. Compared with other threads, trapezoidal threads have a lower wear rate at high temperatures, and their service life is about 30%-40% longer than that of V-shaped threads.
In high-load, high-wear applications, high-strength alloy steel or stainless steel is chosen. The trapezoidal thread made of 42CrMo alloy steel has a tensile strength of up to 1100 mpa, which can maintain stable performance under heavy load conditions. For some environments that require corrosion resistance, such as chemical equipment, trapezoidal threads made of stainless steel can provide a longer service life and can be used in highly corrosive environments for more than 15 years.