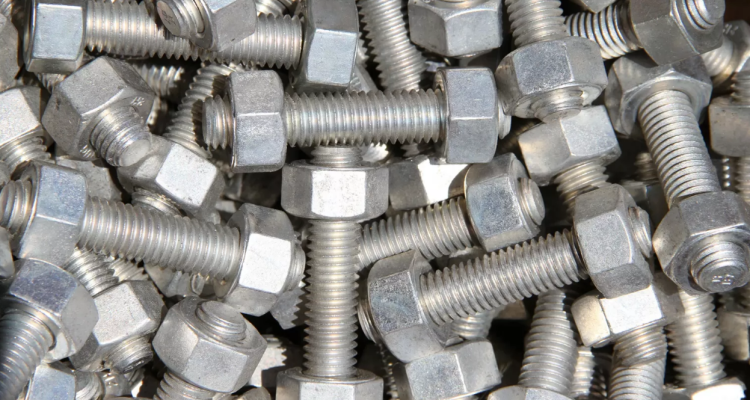
What is a Philip Head screws used for
Assemble furniture
Taking the assembly of a standard-sized wardrobe as an example, it can be done in an average of 75 minutes using Phillips head screws, while traditional flat head screws can take more than 90 minutes. The design of the Phillip head provides better torque transfer and slip resistance, and the tighter engagement between the tool and the screw effectively reduces slippage, thus saving time and labor.
The average selling price of the same number of Phillips head screws is 15% to 20% lower than other types of screws, and the wholesale price of 100 Phillips head screws with a specification of 4mm x 50mm is about 30 yuan, while the price of torque screws with the same specification may be as high as 36 yuan.
The life of the heat treated Phillips head screw can be increased by more than 40%, and the fixing effect of Phillips head screw remains good after 10,000 cycles and the failure rate is less than 5% in the opening and closing test, which is subjected to an average of five times a day.
Phillips head screws can be installed with an automatic screwdriver in one-third the time of a manual screwdriver. Specifically, the installation of a bookshelf with 20 screw points takes only 10 minutes using an automatic screwdriver, compared to 30 minutes for manual work.
Philips head screw manufacturers often use recycled materials such as recycled steel and environmentally friendly coatings, and about 70% of Phillips head screw products on the market are marketed as using environmentally friendly materials.
Electronic product
In the manufacturing process of smartphones, Philips head screws can be used to secure components more efficiently. More than 30 Phillips head screws of different sizes may be used inside a smartphone, and using an automatic screwdriver to assemble a smartphone containing Phillips head screws can reduce assembly time by an average of 20%, from the original 15 minutes to 12 minutes.
Phillips head screws not only increase the assembly speed, but also significantly enhance the overall durability of the product. In the hinge part of the laptop, the use of Phillips head screws can withstand more frequent opening and closing movements. After 10,000 opening and closing tests, the damage rate of the hinge part of the laptop with Philips head screws is less than 1%, while the damage rate with other types of screws is as high as 3%.
The unit price of Phillips head screws may be slightly higher than that of ordinary screws, but they are cost-effective in the long run due to their longer service life and ability to reduce maintenance costs. In the production of tablet computers, for example, although the use of Phillips head screws increases the cost of raw materials by 2%, the total cost can be reduced by 5% over the life of the product due to its lower repair rate and less maintenance needs. For example, replacing Philips head screws inside an ordinary home printer takes an average of 5 minutes, while using special screws can take more than 10 minutes.
Some leading electronics manufacturers have reported success in reducing waste in the production process by 30 percent by using Phillips head screws made of 80 percent recycled materials, without reducing the overall performance and durability of the product.
Construction project
The use of Phillips head screws in steel structural connections in tall buildings can ensure the structure is strong and stable, and a standard multi-story commercial building project may use more than 10,000 Phillips head screws. With the automated screwdriver system, the installation time of each screw can be controlled within 5 seconds. Philips head screws are usually made of high-strength steel, which is heat treated to enhance its corrosion and shear resistance. In bridge construction, Phillips head screws have been tested to withstand tensile forces of up to 500 kg per square centimeter.
Although the procurement cost of Phillips head screws is about 20% higher than that of ordinary screws, the total cost of the entire project can be reduced by about 10% due to its lower replacement rate and less maintenance requirements. Construction projects using Philips head screws are constructed about 30% faster than projects using traditional screws, which directly shortens the total project duration, reduces construction costs and improves the project return on investment.
In some green building projects, more than 90% of the Phillips head screws used are made of recycled steel, which meets the requirements of green building materials and contributes to the green rating of the building project.
In a typical car, about 3,000 to 4,000 screws are used, with Phillip head screws accounting for about 30%. These screws are mainly used to secure interior panels, engine covers and body components. In automotive engine assembly, using electric torque wrenches to install Phillips head screws can reduce the average installation time per screw to 8 seconds, about 20% faster than using conventional screws. The introduction of automated assembly technology, combined with the use of Phillips head screws, can increase production efficiency by 15%.
In a cost analysis of midsize SUVs, despite a 5% increase in initial screw costs, the total cost of ownership of the complete vehicle decreased by 7% over a five-year cycle due to reduced repair and maintenance needs. After 48 hours of continuous salt spray test, the Phillips head screw has no obvious corrosion on the surface, ensuring the long-term performance of the screw in harsh environments. Some Phillips head screws now use recyclable steel and chromium-free environmentally friendly galvanizing process, which not only reduces environmental pollution in the production process, but also improves the recycling rate of screws.