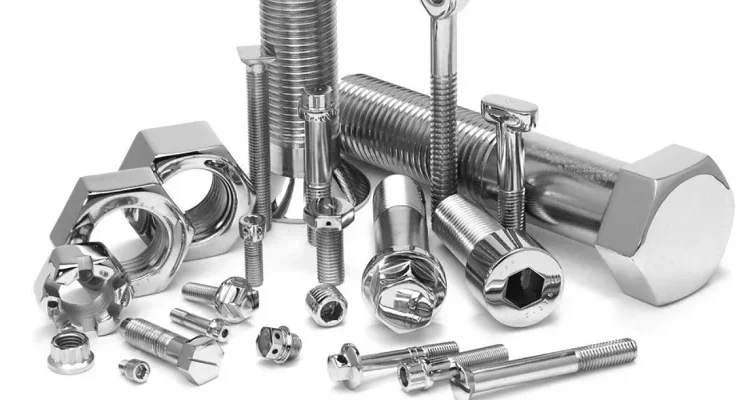
What is the difference between bolts and screws
Bolts are used for high-strength connections, such as bridges and heavy machinery, with each bolt having a tensile strength of up to 1200 MPa. Screws are used for lighter structures, with a 40mm wood screw having a tensile strength of about 200 Newtons.
Table of Contents
ToggleBasic Characteristics of Bolts
Bolts are an indispensable component in various industrial and construction applications, serving as the go-to fastening tool of choice for connecting structures or pieces of equipment. Bolts are generally made of high-strength steel, and their surface hardness, including toughness, can be guaranteed to withstand the higher load requirements required under harsh environment conditions. Standard 8.8 and 10.9-grade bolts offer tensile strengths of around 800 MPa for the former and about 1000 MPa for the latter, thus maintaining strength under tremendously high-pressure circumstances.
One of the design features of bolts is their smooth cylindrical structure, combined with hexagonal or other shaped heads, allowing torque to be applied using tools such as wrenches. Bolt connections are frequently used in the machinery manufacturing and construction industries for connection between large structural components (i.e., bridges, steel structures, and heavy machinery). High-strength bolts with diameters larger than 25mm are usually employed in large steel bridges, and nearly all of the few thousand or tens of thousands of bolts on each bridge ensure they can safely bear traffic loads.
The process for installing fastening bolts is quite simple but needs a certain amount of torque control to guarantee a firm enough connection. With a torque wrench, it is possible to tighten with the exact desired torque; a medium-sized M20 high-strength bolt should receive 500-600 Nm force during initial tightening. If the connected part loosens during operation, even some high-precision mechanical equipment or hydraulic wrenches are used for bolt tightening to make each connection evenly stressed. For example, more than 2,000 bolts are required during the installation of a large wind turbine; each bolt must be tightened to exactly 600 Nm.
A second important feature of bolted joints is that they are removable, which can be crucial for equipment with high maintenance requirements and regular inspection. Tens of thousands of bolts hold the tower and blades of wind turbines, making them easier to maintain and mostly replace after a decade or so in service. According to statistics from the wind power industry, a general type of turbine has over 2000 bolts or more on every unit, whose bolting quality is strictly stipulated in cyclic fastening and loosening to guarantee proper functioning and safe operation of overall equipment. The process of doing a thorough repair or upgrading the wind turbine sometimes takes tens of man-hours and can cost tens of thousands if required to loosen and re-tighten bolts.
The use of bolts to join prefabricated elements is also common in the construction industry. High-strength bolts are mostly used in the installation process of prefabricated concrete slabs, which not only reduces construction time but also ensures safety and reliability. Using bolt connections provided at the cogging end of prefabricated slabs, installation happens 30% quicker than by traditional welding methods – 1.4 hours per slab compared to two full working hours for each and with fewer sparks and less dust on site, as in-site data reveals.
Basic Characteristics of Screws
A screw is a type of fastening that can be used in conjunction with other products, and even though they attach to the holes, there are sometimes many usages for these different types. Typically, a screw will have a head on one end that functions as the mechanism to drive it in; older styles had heads at both ends! Often made of carbon steel, stainless steel, or brass, different screws are appropriate for different environments. These screws are made of 304 stainless steel, with different materials suitable for different environments. 304 stainless steel screws are widely used in marine and chemical industries due to their corrosion resistance, with a tensile strength of about 600 MPa, capable of withstanding approximately 61,200 Newtons of tension, maintaining stability for up to 20 years in humid and corrosive environments.
There is a large assortment of screw sizes and types from M2 to M12 in diameter with various lengths respectively and thread forms for different applications. Self-tapping screws are a special type with sharp threads that can penetrate iron and steel or plastic pieces. They are suitable for fastening between thin metal plates and pipes like common bolts that need nuts to be tightened from the rear flank without specific tapping teeth cutting at all times. Metal frames for which 3.5x25mm self-tapping screws are typically chosen feature about 500 Newtons in tension force per screw, guaranteeing a rock-solid connection that is safe to use for a long time. Self-tapping screws are widely used in automotive manufacturing, especially in body and chassis components, where the speed of an installation line can install more than 5,000 self-tapping screws per hour, significantly increasing production efficiency.
In the woodworking industry, wood screws are widely used, designed to form a firm connection in wood. Wood screws typically have coarse threads and sharp tips for quick installation, with a 4x50mm wood screw having a thread depth that effectively grips the wood, providing a pull-out resistance of about 250 Newtons per screw. Approximately 20 to 30 screws per square meter of wood are needed to ensure structural stability, with wood screws accounting for over 70% of fasteners used in the furniture manufacturing industry.
In the electronics industry, micro screws (such as M1.4 and M2 specifications) are used for fixing precision components. The housings and internal components of smartphones commonly use 1.4x4mm micro screws, with each phone using an average of 30 to 40 micro screws to ensure the firm connection and durability of components, allowing smartphone production lines to assemble 500 to 600 phones per hour.
Installation tools for screws include manual screwdrivers, electric screwdrivers, and automated assembly equipment. Automated equipment can install screws faster than 1,000 screws per minute on high-volume production lines. For home appliance manufacturing, there are around 200 screws used per washing machine alone; automated tooling can install all of these screws within 5 minutes, saving production costs by about 15% per machine while enhancing the quality for robustness.
Screw designs also include various head shapes and drive types to meet different installation needs. Common head shapes include flat head, round head, and hex head, with drive types including cross-slot, hex socket, and external hex. In automotive manufacturing, a large number of hex head screws are used to facilitate efficient assembly with automatic wrenches, with each car using an average of about 3,000 to 5,000 screws, ensuring that each connection point reaches the specified fastening force.
Comparison of Bolt and Screw Usage
Bolts are generally used for high-strength joints that resist shearing forces, while screws are used in assembling light and medium structures.
Bolts are widely used in construction and machinery manufacturing, particularly in large steel structures where each connection point typically uses bolts with diameters between 20 to 30mm and lengths exceeding 150mm. Steel bridges require over 20,000 bolts per kilometer, which must withstand enormous tensile and shear forces to ensure structural safety and stability. High-strength bolts are relatively expensive, but they offer high tensile strength and durability, with a lifespan exceeding 50 years. In heavy machinery manufacturing, each large excavator uses over 3,000 bolts to ensure firm connections of various components. For example, M24 high-strength bolts with a tensile strength of up to 1,200 MPa, each costing about 20 yuan, can withstand 120,000 Newtons of tension.
Screws are more commonly used for fixing light and medium structures. In home assembly and woodworking, each item might require 100 to 300 screws, with specifications ranging between 3 to 5mm in diameter and lengths around 20-50mm. An average 40mm No.4 wood screw costs only 0.1-0.3 yuan but can resist approximately 200 Newtons of pulling force. Every single smartphone needs 30 to 50 micro screws in electronic product assembly, with standards like M1.4 or M2 and lengths from 3 to 6mm. These small screws require high-precision manufacturing and characteristics like corrosion resistance and high strength to ensure long-term stability.
Automotive manufacturing uses both screws and bolts extensively. Each car uses an average of 3,000 to 5,000 screws, costing around 0.2 yuan each, and 1,000 to 1,500 bolts for body and chassis connections, with bolts costing around 5 yuan each. Automated assembly equipment can install screws efficiently, fastening more than 1,000 screws per minute, increasing production efficiency, and reducing labor costs. Bolt installation usually requires torque wrenches or hydraulic tools, offering stronger and more stable connections. The lifespan of bolts and screws depends on their materials and usage environment, with screws lasting up to 20 years indoors and high-strength bolts exceeding 50 years outdoors or in harsh conditions.
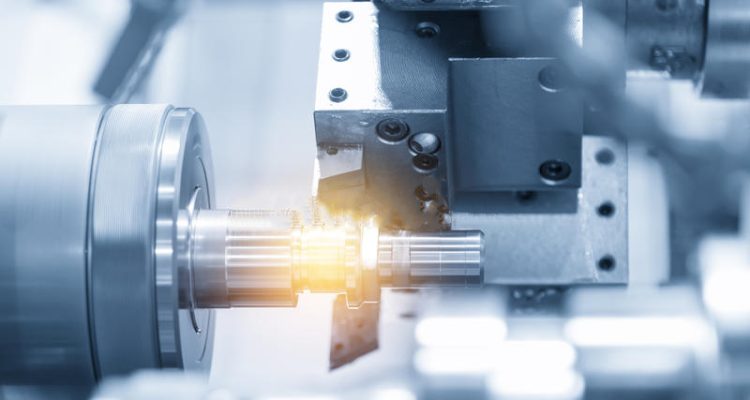
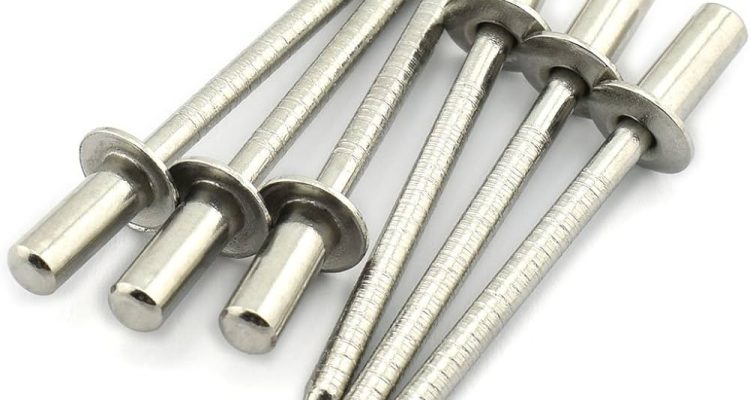
7 Tips For Choosing The Correct Rivet Size
Choosing the ri…
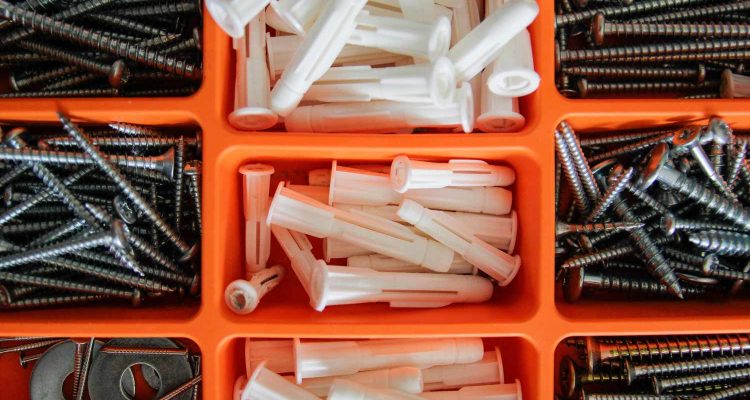
How To Use Screws To Fix Different Materials
To fix differen…