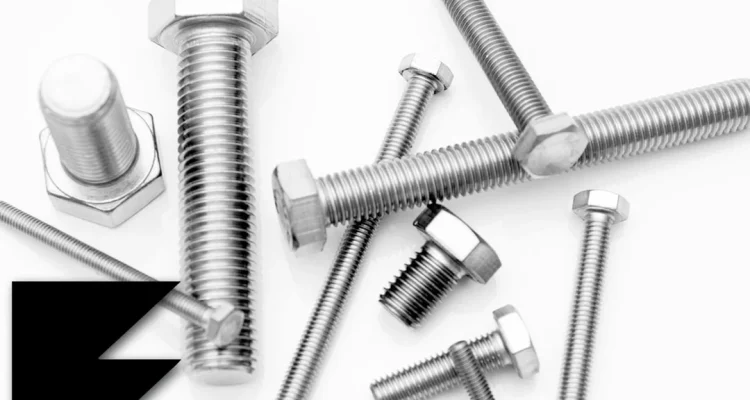
5 Differences Between Set Screws And Bolts
Set screws are headless and fully threaded, used for securing without nuts, and allow precise adjustments, while bolts have heads, partial threading, require nuts, and provide stronger, fixed connections
Physical Properties of Set Screws and Bolts
Physical Properties of Set Screws
Set screws are relatively small components that are used to secure objects or parts to other parts without needing nuts. In order to be able to do so, they need to be made of high-grade steel, stainless steel, or brass so that they can withstand the stress and other environmental factors. On that note, the hardness of these screws is important so that they can grip the part they are screwed into and still withstand this pressure without deforming. The hardness value of a set screw generally ranges from 22 to 32 HRC.
In addition to that, the tip of these fasteners, in this case, set screws, is a defining characteristic that distinguishes them from other similar components. While the most common type is the cup point, suitable for all purposes, cone points can also be used to set screws better by penetrating the part. An example of their application is the automotive industry where the pulleys and gears used are installed with the help of set screws, so they stay in position when the engine puts them under pressure.
Physical Properties of Bolts
Bolts are used with nuts to secure two or more unthreaded parts. They come in a variety of sizes and grades from Grade 2 to Grade 8 where the last is the hardest and most durable. It is constructed of steel, stainless steel, or titanium, with grades 5 and 8 made of steel. The tensile strength of Grade 8 is 150,000 psi. In addition, the threading is one of, if not the most, important features of the bolts. The screwing system is made to specifically fit with its corresponding nut. An example of their use is their application in the construction industry, mostly steel frameworks. In order to choose between these two components, one must take into consideration all of their physical properties, such as what the components are made of, what forces and other factors will they be subjected to, and the precautions to be made when choosing one.
Scenes to be Used for Set Screws and Bolts
Set Screws: Applications and Examples
Set screws, also known as grub screws, are mainly used in applications where space is limited, and a solid and secure connection is required. They are designed to hold an object within or against another object and do not require a nut.
Securing Pulleys and Gears on a Shaft Set screws are used in mechanical systems to secure pulleys and gears to shafts. For example, in conveyor belt systems, set screws prevent the pulley from rotating and slipping on the shaft, ensuring the belt is properly moved and tensioned. Proper support and guidance of the conveyor belt are critical in manufacturing processes where any slip could lead to misalignment and halt the operation.
Electronics and Small Devices Set screws are widely used in small devices and electronics to secure the knob on potentiometers and other rotary devices. For example, in audio equipment, set screws secure control knobs, thus allowing for accurate and proper adjustment without the risk of slippage or falling off.
Medical Devices Set screws are used in the assembly of different medical devices, such as surgical instruments and orthopedic implants. For example, in spinal fixation systems, set screws secure rods and plates to vertebrae, supporting and stabilizing the spine during healing. The stability and accuracy provided by set screws are particularly critical in such applications.
Bolts: Applications and Examples
Bolts are used in applications where a sturdy and detachable connection is needed. They are usually combined with a nut to hold objects together.
Construction and Structural Applications Bolts are widely used in construction to assemble steel beams, columns, or other structural elements. In the case of steel skyscrapers, high-strength bolts secure steel beams and other structural components, ensuring the integrity and stability of the building. Bolts are necessary to assemble the structure and later disassemble and maintain it.
Automotive Applications Bolts are used throughout the automotive industry to assemble various components and parts of motor vehicles, from engines to chassis. For example, bolts are used in the engine to secure the cylinder head to the engine block. They must adequately withstand heat and pressure during engine operation. Such materials are necessary and essential for the proper functioning and safety of the vehicles.
Heavy Machinery and Equipment Bolts are critical for the assembly and maintenance of heavy machinery and industrial equipment. For example, in mining equipment, bolts hold together large and massive components, such as excavator arms or crusher frames. In such cases, the parts are held reliably and securely thanks to the ability to later detach and dismantle them to perform regular maintenance tasks.
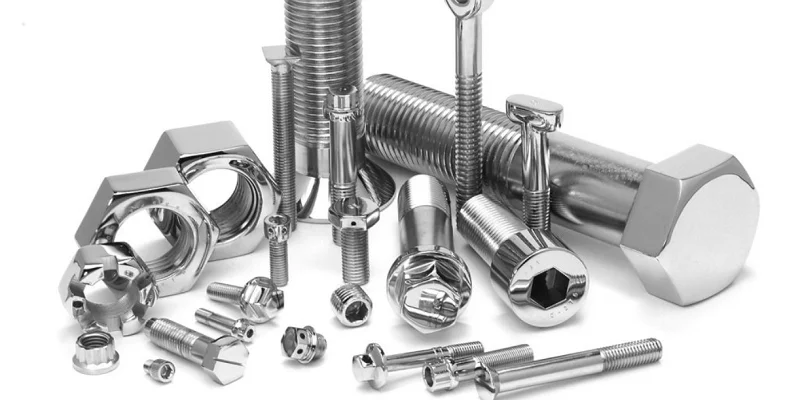
Types of Fasteners and Their Application – WayKen
Attachment Method of Set Screws and Bolts
Set Screws: Attachment Method
A set screw, also known as a grub screw, is used for internal applications where it is threaded into a tapped hole of one part and tightened against a second part to prevent movement.
-
Direct Pressure Attachment Method Set screws attach parts by utilizing direct pressure. The screw is attached to a pre-threaded hole and tightened with the help of a hex key or Allen wrench. For example, in order to put a pulley on the shaft, a set screw is weighted with the help of an Allen wrench to transmit the power to the pulley by exerting a pressure on the others’ sides. Since the pulley is threaded on one side and the screw applies pressure on the other side, the pulley does not move and start rotating with the screw.
-
Differences in Tips Usage Differences between set screws are concerned with the tips and the effectiveness of its use. The most popular types of tips are cup points, flat points, and cone points. The former is efficient and applies a good grip in a given surface without causing any damage. The second tip is used where surface damage should be minimized, such as for delicate machinery parts. The latter type is necessary to penetrate addiction into the softest of surfaces to provide a grip where it is impossible for a set screw to penetrate further.
Example in the Invention: Set screws in a cup are used in the robotics industry to attach gear to the rotating shaft, with a cup point providing a grip that is useful for the shaft with no ruing of a surface. The motion of the motor put through a gear can be useful for accurate rotation purpose. The gear’s movement must stay accurate for the robot to function.
Bolts: Attachment Method
Bolts attach two parts by clamping to them with the help of applied pressure and are designed to be removable.
Bolts secure join between bolts by threading them through unthreaded parts and attaching with the help of a nut.
-
Nut Clamping Force Application Bolts are primarily used to secure clamping force over the selected two or more parts. The high pressure is applied by tightening the nuts through the pressure of the parts. The parts are applied together by such pressure. It is susceptible to either disassembly and further assembly. This is necessary for situations that involve application.
-
Washer Use to be Stabilized the Part Application wasters spread the load and help minimize damage where the parts are applied. Flat wasters that are both used to provide a wider application surface to spread the load. Lock wasters are used when nuts can become unscrewed at a part pressure application.
Example in the Invention: Bolts are widely used in bridge construction to attach the components. They are used with nuts and wasters to apply a load to the pre-drilled holes in a big steel construction. This can be useful in attaching to assemble the bridge for minimizing the used surface.
Material and Strength of Set Screws and Bolts
Set Screws: Material and Strength
Set screws are usually made from high-grade materials to guarantee durability and adequate performance. The material type directly determines the strength and application suitability of set screw.
Material Selection Set screws are generally constructed from steel, stainless steel, and brass. Steel set screws, heat treated to boost the hardness, are used in general applications. These are more economical, and they offer a good balance of strength and cost. Stainless steel set screws are used because of their high corrosion resistance. They are also good for highly moist or chemical environments including marine or chemical processing facilities. Brass set screws are constructed because they are quite soft. They are used in situations where the surface or the material being assembled should not be damaged in any way, for example, an electronic assembly bolt.
Hardness and Tensile Strength The hardness of set screws is very critical for their function. Heat treated steel set screws, for example, have a hardness of around 45 to 50 HRC. Tensile strength for set screws ranges from 170,000 to 180,000 psi, which means that they can withstand loads of pressure or torsion without snapping or bending.
Example in Action: In aerospace engineering, stainless steel set screws are used to fix the aircraft engine components in place. This high tensile strength and good corrosion resistance would provide a screw that can withstand the high heat and the high speeds of an aircraft engine while resisting the wet or dirty external atmosphere of such a component.
Bolts: Material and Strength
Bolts are made from a wide variety of materials including those designed to work in corrosion-prone or heat affected environments. The material and strength of a bolt determine the suitability for its specific application.
Depending on the application, bolts can be made from different materials. The most common types are carbon steel, alloy steel, stainless steel, and sometimes exotic materials such as titanium. Carbon steel bolts are the most widely used, as they have a good combination of strength and affordability. The most common type of carbon steel bolts – Grade C, – can be often seen in general construction and machinery. Alloy steel bolts, which are usually heat-treated to get an additional degree of strength, are used in more high-stressed applications like automotive and heavy machinery. Stainless steel bolts are corrosion-resistant, so they can be used in marine or chemical construction. Titanium bolts have poor machinability but are still used in aerospace construction due to their high strength-to-weight ratio and high resistance to extreme temperatures.
Bolts are also classified by grades, based on their material properties and tensile strength. For example, a medium carbon steel bolt of Grade 5 has a tensile strength of roughly 120,000 psi, so it can be primarily used in automotive applications. A medium carbon alloy steel bolt of Grade 8 has a tensile property of about 150,000 psi and is used in high-stressed applications such as heavy equipment and construction. The construction example provided would be a wind turbine; such a structure is assembled from dynamically-loaded sections, so the use of the high-tensile property alloy steel bolts is justified. The application is also subject to high operational loads, and so a high tensile property is needed to ensure the bolts can withstand the dynamic loads and environmental conditions.
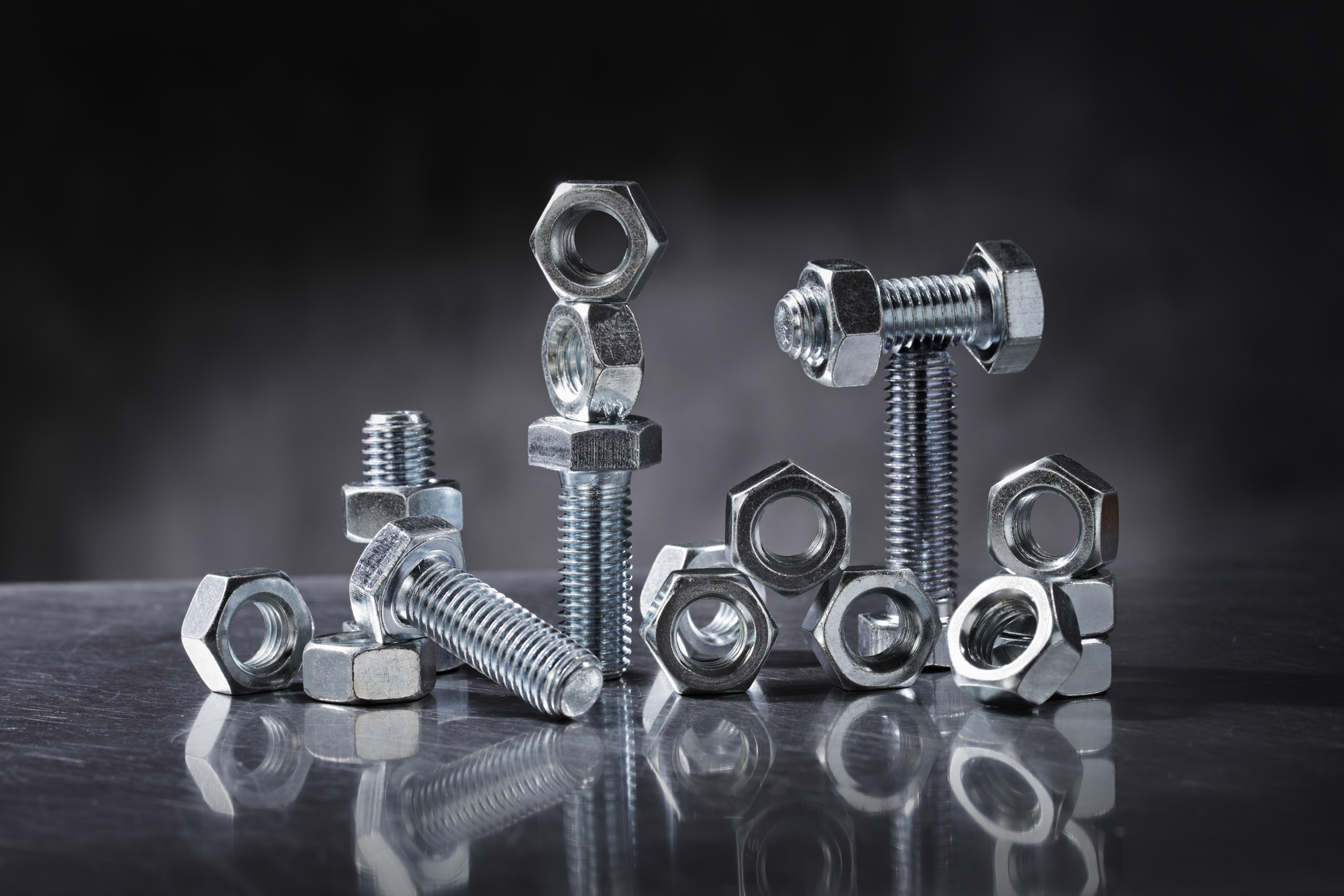
An Overview Of Nut And Bolt Compatibility
Disassembly and Adjustment of Set Screws and Bolts
Set Screws: Disassembly and Adjustment
Set screws are designed in a way that allows frequent adjustments or disassembly of the objects. It is not surprising that they are so widely used since this feature is very convenient and makes screwing easy and quick.
-
Ease of Adjustment. Set screws can be adjusted with a hex key. Usually, it is necessary to rotate the screws very precisely, otherwise the component may be damaged or not tightened enough. It is very convenient when the precise position of an object is of paramount importance. In woodworking, set screws are used to adjust the parts of a router or saw so that they are firmly held in place. If a worker wants to reposition a part, they just loosen the screw and shift the tools’ components in the required place. The final touch is once again tightening the set screw.
-
Frequent Disassembly. In the examples from practice, set screws were also used in machinery that often requires maintenance. In a printing press, parts move continuously, and gears and rollers keep rolling. However, even if there was no need to replace a defective part, sometimes there is a need for routine cleaning. In this case, the set screws need to be loosened, after which the bearing and shaft can be easily removed for cleaning. Later, the technician needs to reassemble and secure the parts by firmly tightening the set screws.
Example in Action: Set screws are used in the robotics industry to secure gears and pulleys to the motor’s shaft. When the robot is recalibrated or a part is changed, the technician needs to adjust the position of a tool and therefore adjust the set screw. This is a very quick and easy process and it does not require many resources and time, which is of the utmost importance in the factory.
Bolts: Disassembly and Adjustment
Bolts also create a strong connection, but usually, they require more effort to disassemble it and tighten the component again. Similarly to set screws, they are also used in objects for which frequent disassembly and adjustment are necessary.
-
Secure Connections with Easy Disassembly. Bolts are required to assemble a connection that will be used only for some time. However, the strength of the object is also important, as vehicles and photo tripods are long-lasting, but their component needs to be disassembled for maintenance from time to time. In such cases, an operator usually calculates how much clamping force they need to exert to create a reliable solid, and long-lasting joint. Disassembly of such a joint is facilitated by the fact that one only needs to unscrew the stabilizing nut.
-
Adjustment with Precision. Bolts can be adjusted, but the process is much longer than in the case of set screws. The scaffold’s parts are assembled in a way that is suitable for a specific structure. However, from time to time, it is necessary to change the height or position of the scaffold. To achieve that, an operator needs to loosen the bolts’ nuts before making any adjustment. When the right height is reached, the nuts need to be firmly twisted together with the bolt.