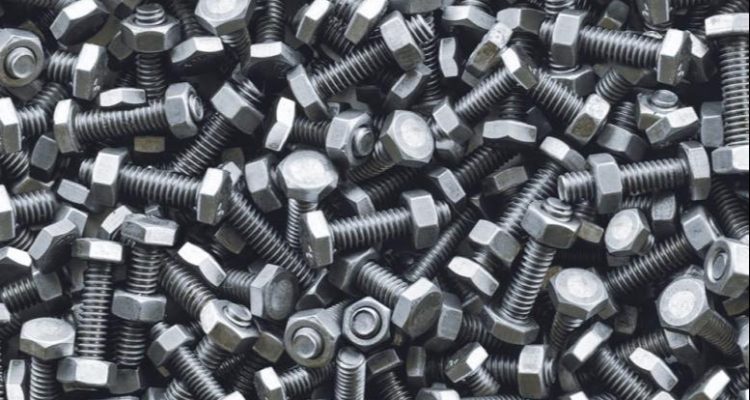
How to design and order custom nuts
Design custom nuts by specifying materials, dimensions, and coatings using CAD, obtaining quotes from manufacturers, and testing prototypes for ISO compliance.
目录
ToggleUnderstanding the Basics of Custom Fastener Design
Designing and Ordering Nuts
Designing and ordering custom nuts is not possible without understanding the materials, specifications, and a little about the engineering software. Custom fasteners are needed in any imaginable field of application from aerospace to consumer electronics for multiple reasons. Perhaps, standard nuts are not optimal for specific applications, or they want a specific performance from a newly developed nut. Several steps need to be followed to design such a fastening device.
Choosing the Material
It is essential to know the desired material for designing a custom nut. The current applications may demand a stainless steel, carbon steel, or an alloy such as brass, aluminum, or copper for their strength and corrosion resistance.
In the case of aerospace applications, designers often choose titanium as a material because of its outstanding strength-to-weight ratio. Marine applications require the material with the greater corrosion resistance; hence 2205 duplex stainless steel is a common choice.
Utilizing CAD Software
CAD is the abbreviation for Computer-Aided Design, and custom nuts need to be drawn with this type of software to become manufacturable. The vast majority of nuts and fasteners, in general, should fit precisely in their corresponding mechanical systems. The designers have to know how their products look before they make them with a detailed drawing. The CAD model will show which material is chosen, dimensions, tolerances, and fastener of such high performance must consider all these values before prototyping.
Specification of the Size and Thread
The nuts may be of any size, ranging from less than an inch in diameter to four inches in a larger machine. There is a broad range of thread designs, from fine threads often used in precision systems to coarse varieties facilitating quick assembly and greater tolerance to dirt and damage.
Development of Advanced Features
Locking teeth or contour designs are some of the advanced features that can be added to a custom nut. A nut with a self-locking feature will not become loose when vibrated and is ideal for use in the automotive or aerospace industries.
-
Engaging with Manufacturers for Production
Having the design finalized, the first step for product is to provide manufacturers with CAD files. It will allow them to access the feasibility and the cost of the production. Moreover, it is important to require offers from multiple manufacturers to have competitive pricing and find better conditions. Additionally, it is critical to ensure they meet the quality and production deadlines that have been set.
-
Prototyping and Testing
Before putting into mass production, it might be wise to create a prototype. In this case, it is possible to test whether any functional requirements are met. 3D printing is used in order to produce the prototype that is cheap and quick. Among the most common types of tests are stress ones, corrosion resistance, and fit checks.
-
Order Placement and Quality Assurance
Once the prototype successfully accomplishes all functionality tests, the next step it to place an order for the first time. However, even more important is to establish the order of quality assurance and control to make sure that every single batch produced meets the standards that have been put. It is possible via regular testing and those required toward meeting the standards such as ISO.
The design of a custom nut is more than just a piece of hardware, and it is an essential building block for engineering solutions. Manufactured precisely, it will meet any functional requirements in a specific project. Engaging with the custom nuts suppliers helps in making it a reality because the most challenging designs are inspired by simple things. Whether they are added in an advanced engineering project or make a standard application better, custom fasteners are about creating a the solution that cannot be purchased off the shelf .
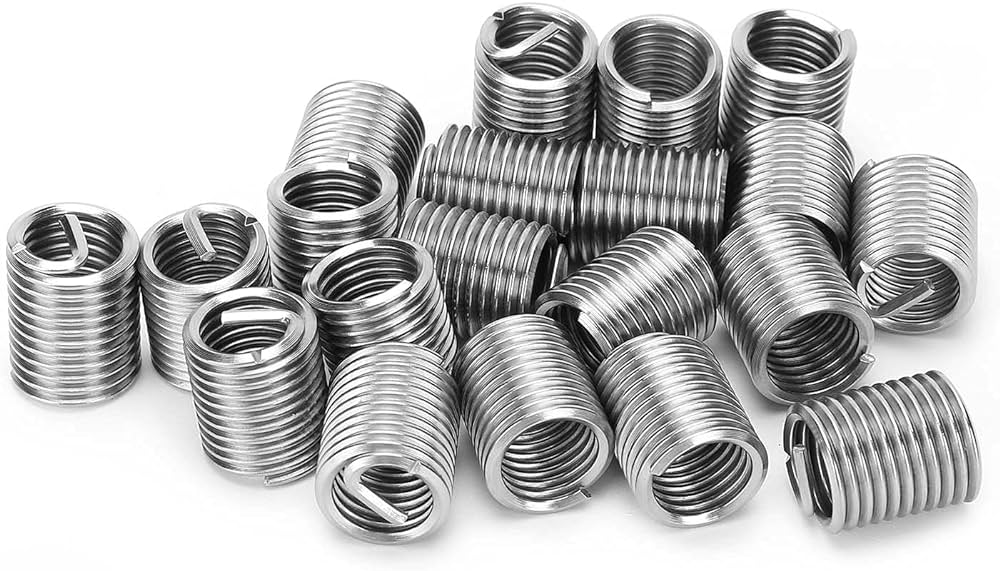
Thread Reducing Nut
Key Dimensions and Specifications
One of the key factors that should be properly understood and accounted for to achieve the successful design and manufacturing of custom nuts is understanding their dimensions and specifications. Not only do these specify the physical size of the constitutional piece, but they also define its application and performance in the environment it is used in. Below is a list of the key examples of nut dimensions and specifications.
Material
The major determinant of the piece of nut’s performance is the choice of material. Strong materials like stainless steel or alloy steel guarantee the piece’s durability and strength, with the former acting as corrosion-resistant and the latter as having the tensile strength necessary for industrial applications. The use of aluminum or its alloys is required in the case of a lower load or worry about the weight, as is the case with automotive or aerospace industrial applications.
Defining the dimension
There are two key dimensions that need to be defined: the inner diameter and the outer diameter of a nut. The dimension of well-known consumer electronics having a size of 2 mm inner diameter and 5 mm outer diameter is used as a small example. A food processing machine may need a nut with 20 mm inner diameters and 50 mm outer diameters to provide an example on the larger side. The thickness or height of the nut is rarely used as an indicator as is not always of importance.
Thread specification
Thread specification is usually defined according to ISO, ANSI, DIN, or other similar standards to avoid confusion and non-fit. The specification itself holds the link or a clue to each piece’s constituting dimensions and size. M8x1.25, for instance, defines a metric nut (M), with an 8mm diameter, and a 1.25 mm pitch specification. The respective English (imperial) nut would be expressed in 0.47 inches with a pitch of 0.04 inches.
Surface finish and coating
The last characteristic used to produce properly working custom nuts is the end surface finish and a coating it. The final layer may be a zinc plating to provide the piece with a corrosion-resistant layer, a PTFE coating to change its functionality in the case of food process equipment where the non-stick capacity of Teflon is desirable. The black oxide surface finish to avoid reflection or another similar finish, with most having further underlying effects, in the case of the black oxide finish the coating also serves to reduce corrosion. The tolerance often serves as a crucial end specification, with the required performance expressed as ±0.01 mm for the diameter and ±0.1 mm for thread pitch, while checking is expressed in the form of dimensional checks for ID, OD, and thickness; material inspection for stainless steel; and the mechanical testing of load and tensile strength to ensure the piece is not of an insufficiently low quality.
Choosing the Right Material and Finish
The choice for the right material and finish for custom nuts is the most essential task that should be done to ensure their proper work in the environment and in the application . To perform this task properly, both environmental conditions and mechanical requirements for a particular material should be evaluated.
Choosing the Right Material
The initial step to be done in choosing the right material is to identify its mechanical properties like tensile strength, the hardness of the material, and the resistance of the material to corrosion. Carbon steel that is famous for its high tensile strength is cheap and used in construction and the automotive industry. However, it needs to be coated to be protected from corrosion. A stainless steel nut resistant to corrosion is corrosion better but is more expensive and not allowed to be used in elevated temperature. In weak conditions but high temperatures and stress. Another material that has an excellent resistance to corrosion and is allowed to be used in clinical and food processing industry is stainless steel AISI 316. Aluminum is known to be light and resistant to corrosion and can be used in aerospace and automotive applications. Brass is resistant to corrosion and is a good conductor of electricity used for electrical and plumbing applications. However, none of these materials meet the requirements of every application and should be chosen based on the use case.
Choosing the Right Finish
The finishing touches for nuts can be vital for its enhanced properties like environmental resistance or reduced friction. Zinc plating that is cheap and corrosion-resistant might be used for the automotive and electronics industry. Nickel plating that has an excellent resistance to corrosion and has a shiny finish should be used in a decorative application and harsh environment. Anodizing that is used for aluminum details enhances the resistance of aluminum to corrosion and wearing out coating and can be also anodized to have a color for coding and aesthetic purposes. Hot-dip galvanizing that is mostly used for the outdoor construction details applies a thick zinc layer to ensure the highest level of resistance to corrosion. For instance, a nut that is planned to be used for outdoor construction is a hot-dipped galvanized nut.
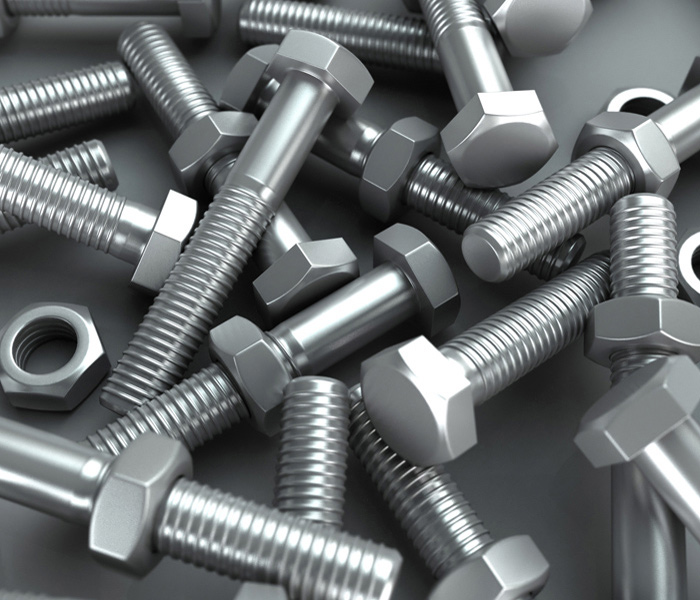
BICT-QATAR
Steps to Ordering Custom Nuts
Ordering custom nuts is a complex process that ensures the final product fully meets all requirements to a specific project. Depending on the design complexity and application, the main stage might change, but in general, it can be described as a path from conception to final delivery.
Define Performance Requirements
The first step is to identify the performance and environmental conditions. A customer should define the load the nut would face, what temperature range it would operate at, and what chemicals it might be exposed to. Correctly setting these parameters would allow selecting the relevant material and design.
Design With CAD Software
The second step involves designing the nut with CAD software. A computer model allows for creating accurate physical dimensions and understanding its sizing and finish. Exact inner diameter, outer diameter, length, thread pitch, and other parameters should be well established. The most commonly used program for this is SolidWorks, but less powerful tools, such as TinkerCAD, might also be helpful.
Choose a Manufacturer
The third step is to find a manufacturer. It should not only be able to realize the design but also work under the defined timeline and budget. Send the files to several companies proposing custom nut production and request a quote and timeline. Compare companies based on cost, technology, and reviews on previous customer experiences.
Produce a Prototype
Before massive production, a prototype should be produced. It allows physical testing to ensure that the nut fits all parameters. Sometimes, it can be tested by its fit in an assembly, sometimes it is exposed to stress testing, or the producer can define the environmental parameter in which the prototype would be tested.
Review and Modify
As a result of prototype testing, some modifications might be required. They can be the change in dimensions, material, or type of finish. The key aim is to ensure that the final product fits the application and works well.
Place an Order
An order is placed when the prototype is successfully made. A client should clearly define the number of nuts and ensure that all timelines and delivery details are set. After deciding on volume and delivery location, it is wise to discuss the post-delivery support to clarify the possible problems and their solutions.
Quality Control
A customer should remain in touch with the producer to ensure they are producing the product on time. Before shipping, products should be checked regarding quality issues, and after one batch is finished, a customer should perform the final review before dispatch.
Get and Check the Ordered Nuts
After receiving the nuts, they should be accepted, and they must be checked for compliance with requirements. Then, they are subjected to final use requirements, and if they pass, can be ordered again in the same company.