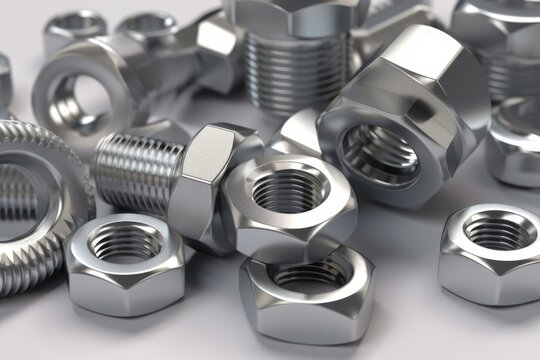
7 Key Features Of High-Quality Fasteners
The seven key features of high-quality fasteners include precise material composition, stringent manufacturing processes, superior coatings, exact dimensional accuracy, robust mechanical properties, compliance with certifications and standards, and reliable traceability and batch testing.
Material Composition
Due to the nature of the product, the quality of fasteners is almost entirely determined by the composition of the materials from which they are made, which in turn affects such performance indicators as tensile strength, durability, and corrosion resistance.
Stainless Steel Fasteners
Since stainless steel fasteners are completely corrosion resistant they are popular choices. A common composition of 18% chromium and 8% nickel, but the most popular stainless steel are the austenitic types, i.e..They contain a minimum of 10.5 percent chromium, which produces a scaly film of chromium oxide on the surface, thus preventing surface corrosion. Sometimes nickel is added to improve resistance to stress corrosion and enhance mechanical properties. Stainless steel bolts are so designated and categorized according to ASTM standards (ASTM A193 Grade B8) to ensure that they are suited to the harsh conditions of high pressure, high-temperature surroundings that can be found in places such as steam turbines in power plants.
High-Strength Steel Fasteners
High-tensile steel fasteners are usually carbon steel or alloy steel made fasteners. Higher load-bearing capacity material, this material is selected for its capacity to be hardened by the use of heat treatment. For the grade 8 bolt, for instance, are constructed using medium carbon alloy steel which is known to have a high tensile strength, hence they can withstand more pressure and tension compared to the average bolt. In automotive applications, these are widely used due the high torque and stress involved.
Specialty Alloys
For example, aircraft and other high-stress or safety applications will often use fastener materials such as titanium or Inconel (a family of austenitic nickel-chromium-based superalloys). The combination of high strength-to-weight and excellent corrosion resistance makes titanium ideal for aircraft applications, including those used by NASA for the Mars rovers. Inconel, meanwhile, boasts much higher temperature strength, and is therefore a major component in things like jet engines and turbine blades where high temperature resistance is key.
Standards and Specifications of Materials
A number of international standards define the chemical composition of the material which is defined within a range and is relevant for the mechanical properties required for the application. These compliance standards are used to ensure compatibility with the operational environment and mechanical requirement. Periodic tests including spectral analysis and tensile checking are carried out to make sure that the components have matching features. This series of testing ensures bigger things such as metal fatigue, corrosion and loading failure are avoided, protecting the whole assembly from issues, and more importantly keeping it safe.
Manufacturing Process
However, the production method of high-quality fasteners is a key factor to their performance and requires exacting methods and rigorous quality control processes to supply large quantities of identical and dependable fastening solutions.
Cold and Hot Forging
Absolutely, the majority of high-quality fasteners are produced by one type of forging process, cold or hot forging. It is commonly used with standard fasteners by shaping the metal at room temperature through cold forging. This not only work hardens the metal but also permits high yields and excellent surface finish. For instance, cold forging of steel bolts improve the yield and tensile strength making these essential for automotive and construction uses.
In contrast hot forging is generally used when low form forces are required, if the part is indenting, if the part has shallow sections, or if the part is of a larger size. This work process includes the preheating of the metal before shaping work which also ensures greater malleability as well as decreases the energy demanded in shape-making of fasteners. Aerospace fasteners are commonly made of light alloy produced by hot forging to precise tolerances, and capable to withstand large stress and temperatures.
Machining and Thread Rolling
Once an item as complex as a fastener has been forged, it then typically is machined to exacting dimensional and feature specifications. Each and every fastener is machined to the exact specification using advanced CNC Machines with tolerance as tight as +/- 0.01 mm. This process is critical simply because numerous purposes which require large wholesomeness for example gadgets and aeronautics use this operation.
Thread rolling is an equally important part of the manufacturing process. Rolling strengthens the thread by pushing the material into the shape rather than cutting it, improving the strength as it crimps the metal grain structure. It also gives a smooth contoured uncut part surface, which decreases its fatigue resistance and load-carrying capacity.
Heat Treatment
Heat treatment is one of the critical process to achieve desired mechanical properties of fasteners such as hardness, toughness and corrosion resistance. The two most widely used procedures are quenching and tempering, where the fastener is heated to a very high temperature and then rapidly quenched in a specific medium. This is a highly engineered process to obey the desired requirements. For example, Grade 8 bolts are heat-treated to a Rockwell C grade of 33-39, making them suitable for heavy-duty applications.
Surface Finishing
The last step of the manufacturing procedure is surface finishing in order to provide the fastener improved corrosion resistance and appealing aesthetics. A variety of finishing other methods exist like zinc plating, anodising, Teflon coating etc. Each of these finishes will provide different protective levels and need to be chosen based on the environment in which the fastener will be used. Stainless steel fasteners with a passive layer are commonly used in marine applications(as they are adapted to the corrosive saltwater environment)
Coating Quality
Fasteners are coated to provide a higher degree of ease, corrosion resistance and increase of fasteners life as well.
Types of Coatings
CoatingsFasteners are available with many types of coatings to extend the service life of the fastener in adverse environments or to increase its wearability in higher temperature and high-wear environments. Zinc plating is the most common because it offers very good corrosion resistance. It deposits a very small coating of zinc to the metal as plating which causes it to rust first instead of the base metal.
While galvanization is the process of applying a protective zinc coating to a different metal, galvanizing is largely an industrial process of DOING ZINC PLATING (top-left). Typically, the fasteners are submersed in molten zinc. This provides a thicker coating than standard zinc plating and is therefore better suited to use in outdoor applications where fasteners will be exposed to the elements for long periods of time. For example, Galvanized bolts are very common in construction and infrastructure work.
Advanced Coatings
For more high-demand environments, like those in aerospace and automotive, nickel coatings are also common. Nickel provides corrosion resistance and also works great where wear is a problem as well like parts that constantly rub against each other. An example of this is the case of aerospace fasteners that use nickel coatings to withstand the harsh environmental conditions.
They are also used because of their anti-galling and low friction properties, such as with Teflon and other polymer coatings. These coatings especially benefit applications that demand rapid assembly and disassembly of fasteners by reducing the torque needed to tighten fasteners and protecting the threads.
Quality Assurance and Testing
Stringent quality control procedures are adopted during manufacturing to guarantee the efficacy of these coatings. To evaluate the coating cold and hot tests, adhesion tests, and salt spray tests will be conducted. For instance, salt spray testing can replicate the corrosive conditions of any number of years the fastener is likely to be exposed to in service and determine how well the coating can protect the fastener through the same period.
The thickness of the layer must be accurately maintained during application. Automotive industry standards – such as those established by SAE (Society of Automotive Engineers) – typically require minimum coating thicknesses in order to meet certain performance specifications. The normal thickness of the zinc layer in an automotive fastener varies from 5 to 25 microns according to the degree of corrosion resistance which is necessitated.
Real-Life Examples In the real world, the durability and dependability of fasteners can be heavily influenced by the quality of the coating. For instance, marine environments prefer stainless steel fasteners with a sturdy chromium oxide layer, providing enhanced resistance to saltwater corrosion. Likewise in industrial applications exposed to chemicals, fasteners with a heavier protective coating will not only prevent premature failure from deterioration but will also prolong the life of the machinery.
Dimensional Accuracy
Fastener manufacturing requires very high dimensional accuracies that any fastener fits perfectly and does its job as it is calculated to be in the assembly. This precision is crucial to not only how the fasteners fit and work, but, also, to the life and dependability of those fasteners in their role within their applications.
Precision in Manufacturing
To ensure the fittings are accurately fitted in the pre-defined holes and with other parts, the fasteners have to be made within very close tolerances. Aerospace fasteners, which are running super loads and must withstand vibrations, for example, are manufactured at a tolerance of +/- 0.0005 inches. This accuracy also allows for the correct alignment and fit tolerances to work together to handle the structural loads imposed on the bearing without the bearing failing due to misalignment or poor fit.
Measurement and Inspection Practices
In order to achieve this next level of precision, manufacturing relies on best in class measurement and inspection techniques throughout the entire process. It can involve using digital calipers, micrometers and coordinate measuring machines (CMM). These instruments ensure that each batch of fasteners matches the design specifications, measuring to the thousandth of an inch.
SPC(Statistical Process Control
Manufacturers also use Statistical Process Control (SPC) to control, and monitor the production process. On identifying exceptions that could be possible out of set standards, SPC has statistical ways of inspection to observe the operation. These metrics allow manufacturers to monitor their fasteners’ dimensions to make real-time adjustments that keep the fasteners within the required specifications, in terms of their accuracy in dimension.
Importance and Applications
Within the automotive sector, for example, assembly fasteners must be precisely dimensioned to keep engines from failing outright. If the bolt is too large, additional stress on the part can result in failure, but if the bolt is too small and fails to secure parts properly, this could also result in engine malfunctions, or worse – accidents.
Mechanical Properties
Tensile strength, hardness and toughness are the most essential and necessary mechanical properties to evaluate the performance and reliability of high strength fasteners. These properties help fasteners to resist forces and adverse conditions without failing.
Tensile Strength
Tensile strength can be defined as the maximum amount of tensile stress that a fastener can resist before breaking. As an example, a Grade 8.8 bolt (an exceedingly common variety used in construction and automotive applications) has a ‘nominal’ tensile strength of 800 MPa, meaning it can theoretically withstand a load of 800 mega Pascals before shearing. Controlled additive and thermal processing produces this exceptional strength for application in high stress environments.
Hardness
It is the resistance of the metal to deformation under a load. An example of how to quantify the hardness of fasteners is the Rockwell Hardness Scale. Bolts for large machines such as cast iron with a tensile strength rating similar to a common steel grade being at Rockwell C15, to those used in mining and off-road equipment being at Rockwell C32, which is very hard and for applications such as high wear required.
Toughness
Toughness means the capability of a fastener to absorb energy and plastically deform without rupture. Fasteners working in challenging enviroments, e.g. in seismic zones or heavy industry would need to have specimens with higih toughness to prevent rapid failure when loaded with a shock load. In this case, allow steel fasteners are used, because they have a better toughness in comparison with common carbon steel fasteners.
Yield Strength
Another important mechanical property is yield strength, i.e.; the stress at which a material starts to deform plastically. Once this threshold is exceeded, the screw (clamp) will not return to its initial state. Automotive fasteners are classically utilized under relatively high dynamic load conditions to resist the forces generated by the internal combustion engine operating which have high yield strengths.
PercentageElongation and Percentage Reduction of Area
Elongation and reduction of area indicate a fastener’s ductility, or how well the fastener will deform when pulled in a direction by tensile stress. This is especially crucial for fastening components subject to movement or flexure, such as in a bridge or swiveling plant machinery. That may be OK ductility in a typical high quality bolt, the elongation is at nearly 12% and the reduction of area around 40%.
Certifications and Standards
The quality and safety of fasteners are the basic objects that certification and standardization need to consider. This is the standard against which manufacturers are judged in terms of product reliability and defined performance under the conditions it is typically used.
National and Local Standards
Fasteners in general are widely held to international or regional standards which define or restrict the intended usage of the fastening mechanism, including whether the fastener is allowed to go out of compliance during use: This is important because a localised failure of a fastener in service may be catastrophic. The International Organization for Standardization, popularly known as ISO, offers a wide range of standards for fasteners of various categories. For example, ISO 898-1 sets out the mechanical properties of bolts, screws and studs made of carbon steel and alloy steel when tested at an ambient temperature.
The ASTM(American Society for Testing and Materials) for example ASTM A490 which provide a standard specification for heavy hex structural bolts made from alloy steel in the United States. Grade 8.8 bolts are created to be used in structural connections like HT bolts and therefore will have been crafted to follow construction-grade standards.
Industry-Specific Certifications
In addition to universal standards, certain sectors may have their own certifications as well. In the aerospace sector fasteners are even required to deliver very high mechanical performance, likewise substances like NAS (National Aerospace Statndards) as well as MS (Military Standards) necessitate fasteners to be extremely accurate and solid to resist the very tough working hard environments.
Fasteners are often certified to IATF 16949, a global quality management standard for the automotive industry. The certification assures that the fasteners used for automobiles are able to withstand the pressure of an automotive environment such as vibrations, temperature extremes and chemical environmental exposures.
Compliance and Quality Assurance
This requires manufacturers to carry out extensive testing and quality assurance processes to meet these standards. This involves dimensional checks, mechanical tests, and material analysis that we do in accordance with the given standards. For example, the ASTM has a standard for tensile strength and toughness testing of fasteners to be used in the construction of bridges, to make sure they have the load and stress capabilities.
Traceability and Batch Testing
In the production of high quality fasteners, the traceability and batch testing are essential parts of quality assurance. These processes give manufacturers the ability to maintain uniformity, quickly identify and rectify defects, and guarantee that every lot of fasteners adheres to the required safety and quality standards.
Traceability Systems
Fastener manufacturers traceability is simply knowing where every fastener came from in the manufacturing process. Typically, UIDs that are engraved directly into each batch of fasteners are utilized by manufacturers. This information can include part of a material batch, date of production, or a particular manufacturing process. Simply put, parts like a fastener used in aerospace might have a traceability code that an engineer can trace from the manufacturing level in case of a failure or maintenance checks on scheduled intervals.
High-Risk Industry Significance
For safety critical sectors such as aerospace and automotive that require a high degree of safety, traceability means the ability to quickly and accurately work out any potential issues. In case of defect in the batch of fasteners, the traceability codes help to identify and recall only those working parts that have suffered from being produced, but not with all the parties. This was apparent in the automotive industry with a recall of a certain batch of bolts for use in critical automotive safety systems with very efficient recall notices in consequence with precise traceability, so that end consumers were minimally impacted tonight.
Batch Testing
While traceability enables more individualized transparency, batch testing works in tandem functioning as a systematic quality assurance approach. Every lot of fasteners is put through a wide variety of tests to prove that it matches the design measurements and also the industrial specifications.) Some of these tests may be mechanical property tests, corrosion resistance tests, and dimensional accuracy inspection. One example is stainless steel fasteners that may be tested with salt spray tests to assure they achieve the needed corrosion resistance levels for marine use.
Advanced Testing Techniques
For fasteners, manufacturers commonly use advanced technologies, like the X-ray fluorescence (XRF) analyzer, to provide totally non-destructive testing. With this technology, they can test the again and again but do not damage the product itself since there is no reason in the world for fasteners if they are not able to determine what you even go through proper composition methods so you waste time sending a batch and a product is not fit for use.