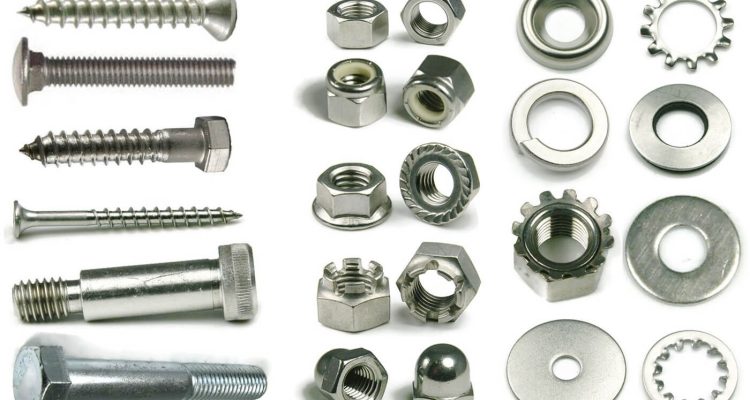
6 Industrial Applications For Sheet Metal Screws
Sheet metal screws are vital in industries such as automotive assembly, HVAC, electronic enclosures, metal roofing, signage installation, and railway carriages construction, due to their durability and precision
Automotive Manufacturing
IndustrialSheet DescriptionSheet metal screwsIndustrialSheet body panels(Button heads only)Ocean & automotive manufacturing, Installed using add-on equipment, Installed using add-on equipment, Vehicle interior & exterior)initWithFrame Vector 134,…Shape from 2D Profile_refl-V1…Shape from 2D Profile_refl-v1 These are self-tapping screws which can be inserted quickly and safely into place, which makes them ideal for use on production lines of any type where efficiency and reliability are important factors.
Automotive Applications Specification Screw
Sheet metal screws are commonly used by automotive manufacturers because of their sturdy construction and resistance to loosening from vibration. This fastener usually features a hardened steel or stainless steel construction to better withstand the outside elements a vehicle is exposed to. On A-Class models, the screws, which are between 10 and 50 mm long, and 3 and 10 mm in diameter, are used to tightly fasten various different parts of a vehicle, depending on the specific remoteness from the car’s manufacturing location and the properties of the parts to be assembled.
Role in Vehicle Body Assembly
Sheet metal screws mainly find their application in the fabrication of car bodies and are used to mount trims, panels, and other body components. While being able to make quick changes on assembly and remove the screws with little fuss for repair and upkeep which allows for flexibility in manufacturing operations. A vehicle door might use 20-30 sheet metal screws just to hold in everything from the door panel and window mechanisms to the handle.
Increased Production Efficiency
Sheet metal screws are a great way to increase manufacturing efficiency within automotive manufacturing plants. The screws allow manufacturers to streamline operations, as they eliminate the need to pre-drill holes and thus speed assembly. This general integration of these fasteners has been shown to decrease assembly time up to 50% compared to standard bolt methods.
How It Affects Safety & Performance
Sheet metal screws also play an important, though less visible, role in vehicle safety and performance. The power of creating a robust and reliable joint is their ability to bind vehicle components so that they resist the stresses of operation and remain intact during high speeds and collisions. The car must remain as a coherent form in order to keep the structural integrity of the vehicle in the crash, thus assures better safety for passengers.
Personalization & Flexibility
They are useful to automotive manufacturers because they can be employed across different materials and many applications throughout the vehicle. Offering a range of head types and thread designs, they accommodate a variety of installation needs, in metal, plastic, or mixed materials, increasing their usefulness for automotive design and production.
Sustainability and Recycling
Lastly, with sheet metallic screws you will promote sustainability in the automotive industry. Another manufacturer with design challenges around disassembly of cars for repair or recycling.Feature critical screws that secured the electric door release motor cover. These screws could be removed without damage to the components, and this trend towards sustainable practices and recycling of cars while increasing the life of cars from many years to decades as opposed to just a few years pays a former to the need for products to have no more than fixing life of 10,000 cycles.
Metal Building Construction
The screws are so important in metal buildings as they are specifically designed to quickly and securely fasten together metal building components, including other sheet metal, heavy aluminum framework, steel joint plates and various other types of metal connectors. They help boost the durability of a building since they let the building be a lot more strong in quickly construction times.
Fastening Roofing Panels
The sheet metal screws are used to fix metal roofing panels metal roofing panels to the supporting steel structure during the roof erection. These screws feature self-drilling tips, which enable you to run the screws right through the metal without the need for pre-drilled holes, making the job a heck of a lot faster. These screws are used in their thousands in any standard industrial warehouse, and each is built to withstand the comfort level of a typical hurricane, making them effective in not only fastening in the building efficiently but also ensuring that it will last.
Securing Wall Panels
The strength for attaching metal wall panels to the structural framework comes from sheet metal screws in wall assembly. The speed with which screws penetrate and hold in metal substrates is vital in maintaining the tight tolerances necessary for quality metal construction. For example, within the construction or remodeling of a commercial building, the number of sheet metal screws used per wall panel can range from 500-1000 based on designs, size and specifications.
Structuralframeworks assembly
There is no exception for the structural frameworks, which are also fastened using sheet metal screws. These are the elements that join beams and columns, and as well provide a large part of the overall stability of the structure. These connections are usually designed to accommodate for the metal expanding and contracting with the heat it is absorbing or radiating out, to avoid structural stresses over time.
An insulation pad is laid,Interior Panels Installed
Sheet Metal Screws are most often used within the walls and roof of metal buildings for attaching insulation, interior panels and headers in place during construction. We then select some screws such that the screws are long enough (based on length and diameter) to prevent the screws from poking through to the outside, but are long enough to catch sufficiently in insulation products.
Doors & Windows Attachments
Sheet metal screws are a must-have if you need to attach metal doors and window frames. All windows and doors are held in place on steel by sturdy construction into the finished recess, providing security and a strong workbench. This is also critical in this sort of application where the fasteners would become muddy and corroded leading in time to rust that would weaken the attachment.
Whole custom fab work and modification
Sheet metal screws excel at custom fabrication and modification during construction. Such adaptability means builders can more readily make “tweak and scoop” onsite allowances, add-ons, etc. With the screws used to secure custom trim, signage and additional support, these screws lend the versatility required for tailor-made construction needs.
Consumer Electronics Manufacturing
Sheet Metal Screws / Sheet metal screws are crucial to consumer electronics because of their high precision and reliability. They are used in a variety of applications, ranging from securing parts in handheld devices to assembling major home appliances.
Securing Internal Components
Sheet metal screws that secure the mother board, battery bracket, and screen fasteners are widely applied in the assembly of smartphones and tablets These screws are so small that they can be as small as a couple of millimeters in size to be able to fit the low size of the instruments. In a typical smartphone assemble, almost 10-15 tiny screws which are sheet metals are used to make all the arrangements for holding anything solid at one location to attain the rigidity and to work as an impact resistance.
Mounting Circuit Boards
Their primary usage is to mount circuit boards into other electronic components (for example; televisions and computers). These opted for screws are an essential safeguard against interchangeable damage sensitive electronic components They are generally equipped with a flat head and low-profile thread which limits the disturbance to its route of circuit pathway, which makes them efficient to hold electronic devices without interfering with their functionality.
Appliance housing manufacture
Microwave ovens, cooktops, refrigerators and other large consumer appliances also use them for securing panels. Load-bearing screws chosen to withstand the operational vibrations of the appliance and resist loosening Around 20-30 screws are typically used per appliance, which helps to make the outer casings durable enough to withstand normal daily use, but soft enough to protect the internal electronic components.
Connecting connectors and ports
Very often, electronic device connectors and ports (for example, USB ports on computers, or mobile devices charging connection ports) are locked with small screws made of sheet metal. These screws are what makes it possible to keep these heavily used interfaces in good condition. Checks like this are often done using reliably screw components made of high caliber metal so they can survive tight and loosening of the screws over the span of the lifetime of the device without them becoming stripped and thereby the connectors becoming useless.
Cooling system communally installed
Sheet-metal screws are used to anchor fans and heat sinks in devices that must be cooled or in other structures. They manage the heat created by the electronic components, and ensure they operate at their peak performance. Typically, the screws used are thermally conductive to help with heat dissipation used to improve the cooling efficiency of the system.
Securing External Accessories
Sheet metal screws are often used to attach external accessories such as stands, cases, and removable covers. This will mean that consumers can tweak or fix their own devices, with no more need for specialist tools. Each is secured in place by screws, meaning that all of these components could be replaced relatively easy, assuming Toshiba and Onkyo ship replacement parts in time.
Aerospace Component Assembly
Sheet metal screws are known for their high strength and are widely used in the aerospace industry to hold together much of the sheetmetal components in aircraft and spacecraft. While the actual uses for these fasteners can range all the way from holding in car panels to securing very critical mechanical systems where they absolutely can not fail their designed application.
Attaching Exterior Panels
Sheet metal screws are the most common type of screws utilized in aircraft construction for securing the aluminum skin panels to the airframe. When these screws are mounted it is because they are not susceptible to corrosion and have a very high tolerance for 40C and beyond environmental conditions at high altitudes. In a typical commercial airliner, for instance, more than 1 million sheet metal screws are employed to fasten these panels, securing a smooth exterior that helps enhance the aircraft’s aerodynamic performance.
Interior Cabins -цьогостановлення
Examples of components assembled with sheet metal screws are seating, overhead bins and lavatories inside airplane cabins. The screws selected are used for their strength and ease of maintenance and overhaul removal and replacement. The screws must be non-corrosive and lightweight in order to not affect the aircraft’s weight requirements.
Securing Critical Systems
Sheet Metal Screws: They are important to fasten the components of crucial systems such as hydraulic, fuel, and electrical systems inside the aircraft. These screws, which perform under service load that meets stringent aerospace requirements in both strength and reliability, are surface-finished to eliminate faliry. Sheet metal screws are applied, for instance, in the building of a hydraulic arrangement for an aircraft; the washers are used to securely fasten the constituent parts to the airframe with every screw capable of bearing the high pressure environmentJapanese JIS standards only have subtended angle set to 25º.
Fastening Cockpit Equipment
Sheet Metal screws are used to attach cockpit instrumentation as well as control assembly. Manufactured to the most exacting standards, these screws may be small but they are carefully designed to keep critical electronic gear from coming loose during the rigors of flight and handling the resulting temperature and vibration. These buttons serve to precisely fit the screws above them, which, through the specific threading, prevent loosening and guarantee the flight control system reliability.
Assembling Engines and Components
For attaching various brackets and housing units in the mounting of engines and other major mechanical parts sheet metal screws are used. These components require screws capable of withstanding high temperatures and loads, which often requires manufacturing screws from special high-temperature alloys.
Spacecraft Components in Assembly
Sheet metal screws used in the space industry to assemble spacecraft built to withstand the vacuum of space and 0 to 572F (300C) temperature ranges. The screws are typically made of titanium or some other high grade metal to offer the strength and corrosion resistance needed for outer space environments.
Metal Furniture Manufacturing
They are widely used in the construction of metal furniture due to the need to assemble the metal parts to create firm, robust and durable furniture pieces. Their ability to attach dissimilar metals without the need for pre-drilling is a big time saver in production as well as an advantage for the life of the product.
Securing Frame Joints
Sheet metal screws—Scale Manufacturing CompanySheet metal screws fasten the joints of metal frames of furniture together, especially in chairs, tables, and shelving units. These screws are chosen for their strength to keep connections tight over years of use — you want this greatness in furniture responsible for weight-bearing and regular movement. A typically designed metal chair might incorporate 8-12 sheet metal screws used to hold all of the joints together which need to support repeated stress.
Attaching Metal Panels
When there is sheet metal paneling in furniture, like filing cabinets or metal desks, they secure the panels to the frame with the help of sheet metal screws. This kind of screw leaves a nice and flush finish making the whole product aesthetically pleasing and providing the basic function of a firmly fixed acoustic panel which can really take a hit from everyday use, of course within reason.
Additional Accessories
It also uses sheet metal screws to fasten hardware and accessories such as drawer handles, hinges, and locks. Perfect for furniture with adjustments or modular furniture, they can be installed and removed repeatedly without compromising their grip.
Improving Structure Strength
Sheet metal screws additionally help with attaching bigger home furnishings including metal armoires or shelving. Those screws can be placed there to act as anchor points for any considerable loads or anywhere that wants to prevent the material from warping or bending under weight.
Gathering Decorative Details
Metal trims or decorative brackets on metal furniture need to be perfectly and securely fastened, and sheet metal screws (SMS) can serve that purpose as well. For all these elements, you need screws that can be painted or finished to match the rest of the design in your piece of furniture.
Custom Furniture Production
Sheet metal screws are also ideal for use in custom metal furniture production, where designs can considerably vary and standard fastening solutions may not be applicable, requiring a much versatile tool or connector to address specific design requirements. They provide the flexibility to support creative furniture and peculiar size, and shape without sacrificing the functional unity of the furniture as well as not destroying the strength and durability.
Shipbuilding and Repair
Marine vessels would not be able to withstand the test of the time without the fastening solutions associated with each sheet metal screw, weather it be used for new ship fabrications or general ship repair. These screws are particularly appreciated with respect to their ability to resist corrosion and strength in connection large steel plates and like materials.
Fastening Deck Equipment
Sheet metal screws are used in shipbuilding as fasteners to attach a posts, such as bollards, cleats, or winches to a steel or aluminum sheet body. These fittings require strong screw solution, which can withstand the dynamic loads caused by the maritime environment and the operational activities of the vessel. Several hundred sheet metal screws are typically used to fasten these components, securing them even under high stress.
Assembly of Interior Panels
These are used in ships, cranes, and most airplanes as well as the construction of interior cabins and compartments in ships, where they are selected for their ability to fasten lightweight metal panels and their excellent resistance to vibrational loosening. These screws enable faster installation and removal, which is important in ship interiors that often involving modifications and repairs.
Exterior Hull Component Locks
Sheet metal screws are used to attach various exterior hull components – including metal sheets and protective barriers. Since the screws are outdoors in salt water, they must be highly corrosion-resistant. Designed to prevent rust and help with long-term durability, marine-grade stainless steel sheet metal screws are often used.
While re-configuring navigational equipment
The sheet metal screws are also used with the navigational equipment on ships, including radar systems and antenna mounts, to ensure durability and security. Bolts used in these applications are made to prevent vibration from loosening them on a moving ship.
Repair and Maintenance Works
They are a time-saving and reliable means to replace damaged or lost components within the scope of repair and maintenance activities on ships. They are easily installed, so ships in urgent need of being re-deployed can be repaired quickly, ensuring minimum time is spent un-ready for front-line duty.
Modifications and Upgrades
Custom modifications and upgrades require sheet metal screws to allow for adaptation of non-standard components into existing structures. This versatility makes them ideal for different kinds of materials and designs, which are necessary to meet the specific needs of unique kinds of maritime equipment.