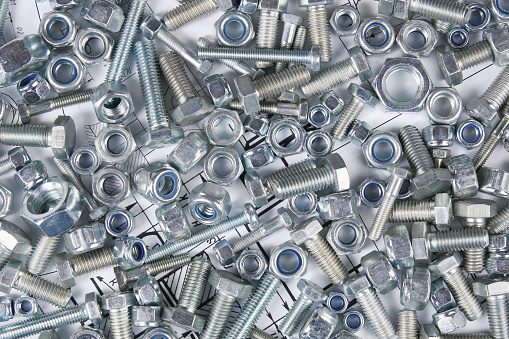
5 Types Of Bolt Surface Treatments
Zinc plating, galvanizing, black oxide coating, phosphate coating, and anodizing are significant for corrosion resistance and enhancing durability.
Galvanized Bolts
Galvanized bolts go through a somewhat intricate process in which they are coated with zinc to prevent corrosion. There are a few types of galvanized bolts, all of which are created by immersing or spraying them with molten zinc. The main goal of coating the bolts with zinc is to make them more corrosion-resistant. The process of galvanization helps to ensure the zinc bonds in both the structure and the surface of the bolts. Here are a few methods which are commonly used, such as:
Zinc Plating
Galvanizing
Black Oxide Coating
Phosphate Coating
Anodizing
A common method used to prevent rust and erosion, production methods have improved and zinc is now typically sprayed on rather than submerged.def. Some benefits of this method include only applying a thin layer of zinc. When under an electrical charge, that layer is applied to the screw. One of the other benefits of this practice is that when it bonds it creates a seal against moisture that is quite effective. Another benefit is that this method only requires the use of a few easily accessible chemicals. The primary downside to this procedure, though, is that the gains in longevity are minimal overall. One of the more effective ways of managing this problem is to coat the bolts in a solution containing not just zinc but nickel as well. The only disadvantage of this particular solution is that it is somewhat more expensive than some other alternatives.
Galvanizing
Galvanizing is another method of coating bolts in zinc. This method is longer-lasting and more durable than simple zinc plating. The coating process involves submerging the bolts in a bath of molten zinc. These baths are typically 460° C. At that temperature, the zinc bond adapts a structure which bonds with the bolts at the molecular level. The process incurs further benefits in that it also bonds with the iron that makes up much of the structure of the bolts. However, when the cost is considered the overall benefit is relatively minimal. There are further varieties of this method which result in slightly better results. One of these involves submerging the bolts in a bath of molten aluminum with small amounts of silicon. This results in a stronger, if slightly more expensive, bond. In any case, whether it is aluminum or zinc which is being applied, this process is non-toxic.
Black Oxide Coating
Black oxide coating is a technique by which bolts are coated to create a aethstetic. The bolts are submerged in a caustic soda, with other nitrates, chemicals and solutions added. The result is chemical cannot only coat the bolts in a black oxide but also offer a coat that is every bit as effective as zinc in terms of corrosion. One might be concerned that with strength comes a lack of malleability; in this case, the oxide coating leaves the bolts looking more refined than alternatives. Submerging the bolts in other acids in the coating process enables further and ongoing protection against decay. This would not only eliminate the possibility of the bolts slowly becoming more prone to rusting with age but perhaps extend their lifespan to an at this point undetermined limit.
Phosphate Coating
The phosphate coating method is another one designed to protect the bolts from weathering and erosion. This method involves submerging them in a solution that contains phosphoric acid. The coating process involves the acid reacting with the surface of the bolts and producing a layer of phosphate crystal. While their aesthetic may be a draw for some, others who take issue with the quality of their sheen and finish will likely be less enthused. Overall, when it comes to drawing consumers in with the visual nature of a product, the smaller details can have significant ramifications.
Anodizing
The final method we will discuss is a method of resistence preservation used on alluminum bolts. One environment where alluminum bolts will have a substantial prescence is the interior of a vehicle but overall, this method is the most resistant to weather damage and holds the longest lifespan. This process involves stripping the atoms on the surface of the bolys bolts off and placing them in a solution which both contains an electrolyte and is electrical charged, which causes the creation of O2 that coats the bolt with an oxide. This can then be dyed, resulting in a more decorative finish. In Conclusion – Overall, galvanized bolts and the process of zinc plating and other solutions such as black oxide coating, phosphate coating, and anodizing are necessary for keeping bolts from deteriorating and cracking over a course of time. Their products are necessary for keeping metal objects of any scale structurally sound and safe.
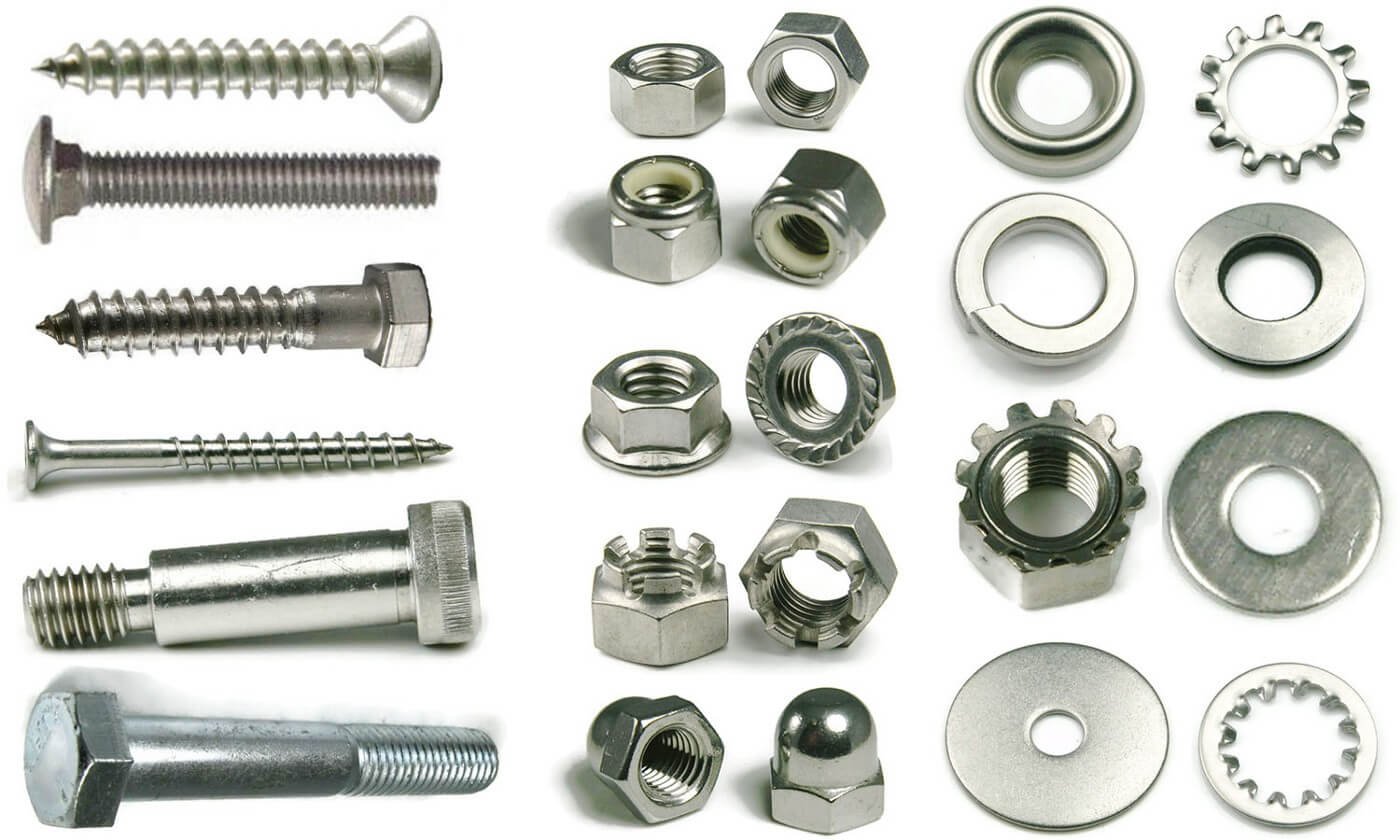
Different types of fasteners used in manufacturing Screws, bolts
Hot Dip Galvanized Bolts
Hot dip galvanizing is a process where bolts are immersed in a bath of molten zinc for superior corrosion protection. Thus, this method should be applied in harsh extremities, thanks to its strength and durability.
A general process outline
Before the start-up to be immersed in a zinc bath, the bolts require some preparation. Adjustments are initiated by cleaning them to make them adhesion free from any dirt, grease or other oxides. To increase bonding, it is better to immerse the bolts in diluted hydrochloric acid or free radical organic solution before embarking on the process.
Immersion in molten zinc
Having completed cleaning, the bolts are now ready for the first immersion in molten zinc to start the galvanizing process. The zinc bath to be used should be heated at very high temperatures, ranging from 450 ° C to 460 ° C. Then the bolts will remain sunk in the bath for a stipulated period. The high temperature of the zinc bath gives it energizing properties that will allow it to react with the surface of the bolts and form a strong metallurgical bond. Thus, the coat that will result from this bonding remains the perfect medium of keeping the bolts free from corrosion.
Quenching
Thereafter, a time limit expires; the bolts will now be shifted to a quenching bath, where they are immersed to cool down in water or another chemical solution. This step will help to fuel the solidification and firming of the coat by enhancing it to adhere strictly to the surface of the bolts.
The final inspection
After quenching, the galvanized bolts are now worn for inspection, and a series of tests ensure uniform coating free from any defects. Those include visual inspection, coat thickness testing and adherence to ensure the new bolts meet the quality requirements of being free from corrosion and imperfection.
Advantages of using hot dip method
One of the benefits that will accrue to the firm that applies hot dipped method is the superior corrosion protection, perfect bonding of the coat, reliability and durability of the bolts and lowered maintenance. Thus, hot dip galvanized bolts may be best used to replace the existing ones when exposed to moisture, salt or other corrosion actors. They are suited for use in outdoor facilities like highways, marine nodes, power transmission systems, utility pole lines, etc.
Nickel Plated Bolts
Nickel plated bolts are bolts that undergo a plating process using nickel on the surface. Both the appearance and function of nickel plated bolts are improved since they are protected from corrosion and wearing.
This electroplating process begins with the cleaning of the dirt, oil, and other contaminants from the surface. Most of these can cause the outcome to have structural imperfections. The bolts are first cleaned to make way for the nickel metal to be added with proper adhesion. The plating is applied evenly on the surface.
Nickel Deposition
The bolts are transferred to a solution or another medium where nickel ions are also present. The mixture is composed of the chemical catalyst and an electrical current source. The current causes nickel ions from the solution to bond into the bolts. It forms a thin layer of nickel plating. It is usually taken control of the thickness of 5-25 microns depending on the use. The bolts may go through another process before buffing or polishing to make the finish appropriate for the application.
Corrosion Resistance
Nickel plated bolts are perfect for outdoor, marine, and industrial applications due to its excellent resistance against corrosion. It can be caused by the various environmental substances that invade it. Being the protective coating against wear and oxidation keeping the structural integrity of the bolt is preserved. It will be last long enough for it not to corrode easily.
Wearing Resistance
The wear resistance of the nickel plated bolts is explained by the fact that they are made out of relatively hard metals. They are not easily subjected to abrasion damaging its surface. They are applicable to an environment where they may be synthesised with other objects, making it a medium for friction and movement. Such nickels are also expected to have a longer time in being used.
Applications
Nickel Plated Bolts have vast uses in automobile, aviation, electrolytes, and building sectors. These are also used in non-corrosion related environments, such as at home and as tools.
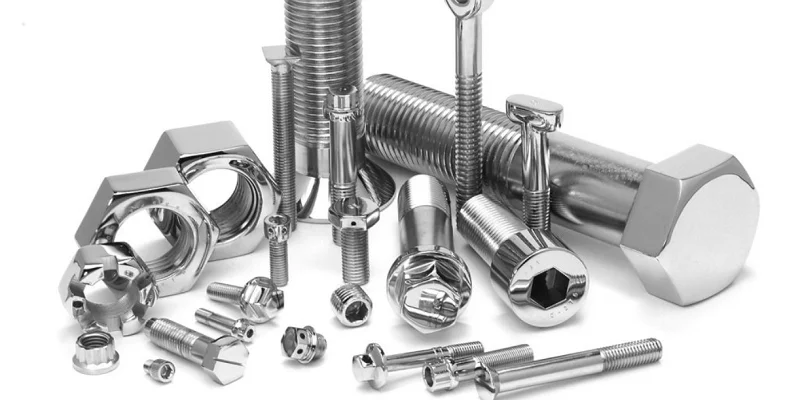
Types of Fasteners and Their Application – WayKen
Black Oxidized Bolts
Black oxidized bolts are coated with black oxide, which is a chemical conversion finish that offers both corrosion resistance and an appealing finish. The black oxidation process involves chemically treating the bolts and involves the immersion of the bolts in a chemical solution. The immersed material is acted upon by a chemical reaction between the surface of the material and the chemical solution to form a layer. The oxide layer formed is black and will typically measure 0.000020 inches thick. The layer is uniform, inert, and dense measuring tightly 76 Vickers in hardness. The black oxidation process also enhances the lubricity of the bolts. In such applications, the thickness of the coating is critical and can affect the texture of such materials.
Cleaning and Chemical Treatment
In the black oxidation process, the bolts are cleaned in order to remove all the available oil, debris, and other forms of contaminants to ready the material for treatment. The bolts are then immersed in specific chemicals and raised to appropriate temperatures for the formation of the new black oxide layer. The chemicals used in the black oxidation process include sodium hydroxide or nitrates, and other oxidizing agents. The metals will diffuse in the oxide layer and move to the surface.
Formation of Black Oxide Layer
On immersion of the bolts in an appropriate chemical solution, which is the black oxide solution, a chemical happens between the surface of the bolts and the chemical formula. This results in the formation of a black oxide layer. The black oxide layer is beneficial since it prevents corrosion, and the formation of the black oxide layer is driven by the immersion of the material in the chemical solution. Therefore, it does not shop the bolts and is always a vital black oxidation process step.
Formation of Black Oxide Layer
The black oxide layer formation on black oxidized bolts extends protection to the bolts. It serves as a barrier to moisture, ambient air that contains oxygen, and other available environmental corrosion-related materials from rusting the underlying bolt material. The black oxidized bolts are always recommended for outdoor applications since the material used is tough enough and resistant to corrosion. The bolts are ideal for outdoor use and in operation because of the capacity to resist rust and wear. They are long-lasting and can work efficiently for more extended periods. The material oxidized black bolts are also available in the automotive industry. They are used as engine components such as engine critical engine components, oil valves, and nitrous systems. They are also available in the construction industry and the business and industrial industry. They are also used in the tools industry.
Cleanup
On completion of the black oxidation process, the bolts will not be exposed to any contamination. The material is cleaned after every application by the cleaning agent. The material is cleaned on completion of the chemical process. The chemical solution available in the above discussion is also removed.
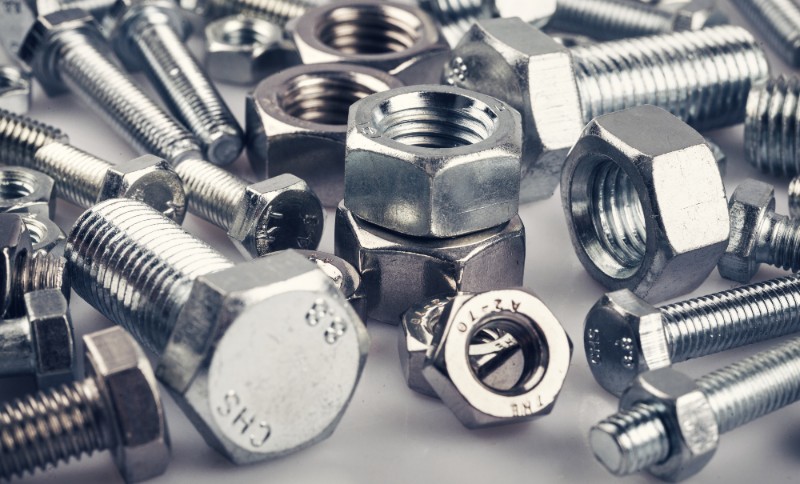
Types of Fasteners Recommended in Industrial Settings
Anti-corrosion Coated Bolts
Anti-corrosion coated bolts are specially treated not to corrode and rust in a wide range of conditions. Types of coating include zinc plating, galvanizing, black oxide coating, phosphate coating, anodizing, and polymer coatings. Regular or chromate passivation can also be used to provide basic corrosion protection. The most widely used ones are galvanizing, zinc plating, black oxide coating, and phosphate coating. There are also thick coatings applied to protect bolts from extreme exposure to wet conditions. They still rely on the zinc plating or galvanizing technology but are of a bigger thickness. Each coating type has unique advantages providing a different level of protection from corrosion.
Zinc Plating
Zinc plating involves covering bolts with a sacrificial layer of zinc. This technology is electrolytic coating on pre-cleaning bolts. Regular thickness varies from 5 to 25 microns, depending on the industry and conditions of exploitation.
Galvanizing
Galvanization is a process of treating bolts by immersing them in a bath of molten zinc. Due to metallurgical bound between coatings and basic metals, such coverage is highly durable and can withstand severe exposure. Regular thickness is from 50 to 150 microns. It cannot be used for small products and is only applied to subassemblies.
Black Oxide Coating
Black oxide coating is a conversion chemical process, which forms the black oxide on the surface of the bolts. It additionally protects the coating from corrosion and creates an appealing black color. Normally, the thickness of the coating can be controlled within 0.5-2 microns.
Phosphate Coating
Phosphate coating is a process of immersion of the details in a solution of phosphoric acids and special ingredients. The coating consists of numerous small crystals. The most important part is crystalline basic phosphate, which provides not only protection and toughness to the coating but also helps to bind other coatings and secondary treatments. Anodizing is typically applied for aluminum bolts. It is the most advanced technology of creating a protective oxide layer using electrolytic coating of aluminium. Regular thickness is 5-25 microns. Acrylic or nylon are often used for polymer coatings. They can be sprayed, and bolts can be dipped in the solution. These coatings artificially create a barrier for moisture or corrosive substances. Regular thickness is 5-100 microns.