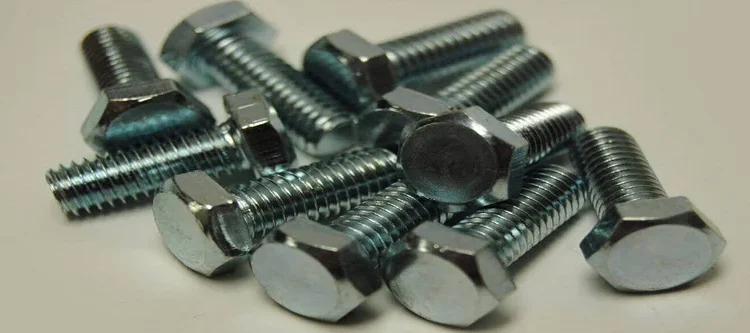
5 Steps To Identify Any Fastener
By accurately measuring diameter, length, thread pitch, identifying drive type, and assessing material grade, you can effectively identify any fastener
Getting Started With Fasteners
When identifying fasteners, the most important place to start is in understanding the key dimensions. Firstly, diameter is important as it is the width of the fastener across its threads. It is useful to know this for ensuring the fastener will fit whatever hole or nut it is intended for. For example, a common bolt might be labelled M6, which indicates a 6mm metric diameter. Length is also vital, as it is the length of the fastener from where the head places itself against a surface down to the end of the fastener. By knowing the length of a fastener, you may be sure it will properly screw into place to provide the necessary hold.
Threads need specifications to be compared
When dealing with threads of fasteners, the pitch is the distance between the tops of the threads and is important for correctly matching the fastener to its appropriate nut or tapped hole. In the metric system, the pitch is often included by a number after the diameter. For example, an M6x1 would have a pitch of 1mm. For fasteners measured in the United States customary system, pitch is referred to by TPI, threads per inch. Such a bolt might be a #10-24, with 24 TPI. This type of identification helps to avoid ruining a thread or ensuring an appropriately tight hold.
Drive type tells you what kind of tool to use
Drive is the kind of slot or recess on the head of the fastener. It is what the tool turns that drives the fastener into the desired surface or out of it if needed. Common examples include Phillips, flathead, Torx, Allen, among others. By recognising what kind of drive a fastener has, you can use the correct tool. For a Phillips, you would use a Phillips screwdriver. By using the correct drive, you maximise the efficiency of installation and reduce the chance you will strip off the head. Fasteners also come in various materials and grades, each suitable or not for various applications. For example, a Grade 2 bolt is standard hardware and is not good for very heavy loads. A Grade 8 bolt is an alloy of medium carbon steel which has been heat-treated and is exceptionally strong with great tensile strength. Steel fasteners are suitable for construction and vehicles, whereas stainless steel is resistant to rust and best for outdoor or marine applications. In real-world applications, it is important to remember that the choice of fastener is very important for ensuring the longevity and integrity of the assembly. A good example would be in construction. In such a scenario, using the wrong fastener could result in a critical failure leading to the collapse of whatever is under load. For instance, in the construction of a bridge, it is important to use very strong bolts made of Grade 8 steel, as they must resist rust and have very high tensile strength. This principle also extends to consumer electronics, where small precise screws are used for compactness and in order to allow easy repair or recycle.
Identify Fastener Types
First and foremost, any product must be accurately measured according to its key dimensions. For instance, diameter measurement across the outer threads is vital to ensure all compatible nuts or tapped holes are compatible with the fastener. If one was to come across a fastener listing, and it was designated as an M6 product, the latter happens to have a diameter in a metric system and would be equal to 6mm. The other crucial dimension supporting the weight of the fastener is its length, measured from the head being flush with a surface to the end of the bolt. It is vital in determining as to how deeply the fastener will go into the material.
Treading Characteristics Examination
The logical choice based on the previous examples would be the pitch in order to reveal the intended means of treading. For instance, fasteners with a pitch in the metric system might be designated as M6x1 wherein the “1” is the pitch measured in millimeters. Regarding the American thread standards, the length of an inch ranges at 24 threads, specifying the information as 24TPI. This information is crucial to test the fastener with a counterpart and ensure both are compatible without the threat of cross-threading.
Drive Type Examination
Different fasteners always operate on various drive types, a design developed to be handled by a corresponding tool. It is used to prevent users from using tools that are not suited to the fastener, such as flathead, Phillips, Allen, and Torx drives. Each is found in a multitude of devices and critical to prevent any accident related to the damage on both sides of the item
Materials and Grade Determination
Let’s imagine the fasteners were discovered in an outdoor vehicle repair. The best option would be to choose stainless steel to avoid corrosion and ensure the fastener is safe to use. Additionally, the best steel option would be a Grade 2 bolt, most suitable for light-duty applications. Hopefully, this information was useful, and all examples were accurate
Drives And Heads
Drive Types
Drive type of a fastener is the area of a fastener that interfaces between the fastener and the tool that either installs or removes the fastener. Common drive types include:
-
Phillips: a cross-shaped slot that allows better torque than flathead screws. The design reduces the slipping of the screwdriver.
-
Flat Head : single horizontal indentation. Flat heads are not ideal for precision application.
-
Torx: star-shaped and has six rounded points. Torx provides high torque transfer and reduces cam-out on the screwdriver.
-
Allen: boyshexagon recess that requires a hex key. Example include M5 Allen bolt. The forces of the fasteners are accessed beyond direct visibility in the case of recesses. The drive types of fasteners are selected based on the tools and application. The Torx is often used in automotive and electronics because they can withstand high torque without slipping.
Head Types
The head type of a fastener determines how the fastener sits in or on the material it is securing. Common head styles include:
-
Flat Head: is designed to sit flush on the surface. They are ideal for any application where the entirety of the object is required.
-
Pan Head: The outer edge of the head is rounded to afford a larger contact area.
-
Button Head: similar to pan head but is comparatively low in profile.
-
Socket head, cap screw: look like a small cylindrical head with a recessed drive.
Selecting the right head type is important because each head type serves a function. The sockets head is commonly used in the machines because the head is strong and can handle high torque while the type is neat. Fasteners are selected based on desired torque, the strength of drive type, and with aesthetic in mind. In the aerospace, flush and countersunk are chosen because they produce a fastener head that is flush and avoids air resistance.
Measurements Fit Perfectly
To ensure a bolt fits as required, it is necessary to perform accurate dimensional analysis. The two fundamental measurements are diameter and length. Diameter is typically measured across the threads with a caliper to find the nominal size. For instance, a M8 bolt implies a diameter of 8mm. Length is measured from the point where the bolt’s head rests against the surface it will be fastened against to the other end of the fastener. This last measurement is crucial because it will need to be deep and long enough to penetrate the material and engage with it properly, but not so much that it sticks out and becomes a risk for the bolt and the persons working with it.
Checking the thread
First, thread compatibility must be checked with the use of a thread gauge. At this point, the thread gauge will be used to measure the pitch, or threads per inch. If a bolt being analyzed had a representation of M8x1.25, it would imply that the pitch of the thread is 1.25mm. Another common inconsistency that could result in failure would be installing a left-hand thread into a right-turning nut.
Tolerances of the gauge
To ensure functionality, the model of gauge being analyzed must be within safe tolerances for the specified fastener. Naturally, different applications will require more or less tight tolerances. For instance, an aerospace-quality fastener will likely have any specific tolerances for best application. This matters not only for the fit of the fastener but also its actual properties. A bolt that is out of tolerance will not apply a predictable torque, and its load-bearing capabilities can vary.
Non-generic measurements
Depending on the application of the fastener, other measurements, such as the head height or the diameter of any washers being used, could be just as important. For instance, in an automotive use-case, the right head size and bolt length will make the difference between a smoothly run operation and interference with moving or turning parts.
Materials and Threads
Selecting the appropriate material to use in a fastening application is crucial to the fastener’s performance under specific environmental and mechanical strenuous conditions over time. The most common materials include:
-
Carbon steel – used for its strength and versatility. However, this material corrodes readily and should be either protected or used in dry environments. Other materials should be used in high humidity conditions.
-
Stainless steel – is very versatile and corrosion-resistant and is hence used in harsh environments, such as in marine or with chemical exposure.
-
Aluminum – this lightweight non-ferrous metal material is corrosion-resistant and is appropriate in applications where minimal weight and moderate strength is critical.
-
Titanium – exhibits high strength, is lightweight and has superb corrosion resistance. It is mainly used in aerospace and medical applications.
It is important to identify the appropriate thread type to use as they are paramount to enabling mechanical functionality of the fasteners and to properly attaching to the accommodation part. The thread types include:
-
Metric thread – is denoted by its pitch in millimeters e.g. M10x1.5. Here, 10 mm denotes the nominal diameter and 1.5mm the thread pitch.
-
Unified national thread – is commonly used and its value is given in threads per inch, tpi, in the United States of America. For instance, a ¼-20 denotes a ¼ inch outside diameter and 20 threads’ per inch.
-
Fine and coarse threads – fine threads have a smaller pitch and offer higher strength and better load distribution. However, they form more friction than coarse threads on tightening may gall. The fasteners are used in cases where loosening from vibrations or thermal cycling exposure is very likely.
In conclusion, the category of materials to use in fastening and the thread type are both applicable in industry. For example, automotive manufacturers use high-grade alloy steel for their work-hardened fasteners for fastening engine components. Their fine threads allow the fasteners to hold up under higher temperatures and pressures.