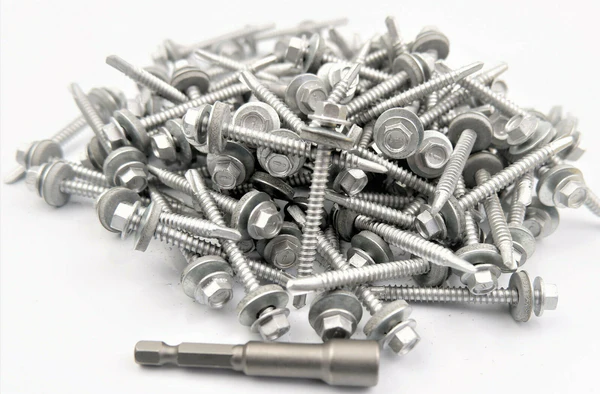
5 Steps In The Cold Forging Process Of Bolts
The cold forging process of bolts includes material selection, die molding, shaping adjustments, quality testing, and final packaging. This method ensures strength and uniformity in production
Material Selection and Preparation
The cold forging process of bolts starts at the initial stage, determinative of the quality and characteristics of the final product. The choice of the raw material and its detailed preparation set a strong foundation for the sequence of further steps in the process of forging.
Steel Grade Determination
The steel grade chosen for the cold forging has a notable influence on the strength, durability, and applicability of the final product. Some of the most typical steel grades used for bolt manufacturing include AISI 1018, AISI 1045, and AISI 4037, offering different properties. For example, AISI 1045 provides a good balance between the machine ability and mechanical performance, usually having a tensile strength of 570 to 700 MPa.
Wire Rod Acquisition and Inspection
The initial step of the next-level preparation of the cold forging process of bolts includes the purchase of massive coils of wire rod, which must correspond to precise specifications in terms of chemical composition and physical qualities. The quality of this rod must also pass inspection for any defects, including cracks or inclusions that could hamper the bolting process or damage the final product’s quality.
Drawing
The wire rod is then drawn, passing through a series of dies that help reduce the diameter and increase the length of the wire. In the process, the grain structure of the steel is aligned longitudinally, providing additional strength to the future bolt. The diameter reduction is precise, with tolerance as low as ±0.01 mm.
Cleaning and Coating
The wire is then cleaned from any scale, rust, or dirt that may have acquired during the process of production or storage. The cleaning may be performed by brushing or by submerging the wire in a special chemical bath. After the cleaning, the wire may be coated with phosphate to help it move through the dies more easily and to prevent rusting in the future.
Cutting to Length
Finally, after cleaning and coating, the wire is cut into uniform-sized segments. The cutting is precise and must ensure the length of each individual wire segment corresponds to the size of the bolt to be forged. The precision is paramount, as the cut determines the weight and quality of the final cold forged bolt.
Molding the Steel Through Dies
Molding steel through dies in cold forging is a crucial part of bolt production. It is the phase of production that transforms the prepared steel wire into the preliminary shape of a bolt. The step is a production of a several die impressions.
Die Design and Setup
The bolts are created through dies, which are planned to fit their shapes. The dies in the cold forging process are massive pieces, made either from high carbon steel or tungsten carbide. Both materials are shock-resistant and strong enough to endure the pressure of forging within the forging press. In a set-up to produce bolts, there will be a couple of such progressive dies. The first die shapes the steel wire according to the design of the head. Each consecutive die is used to deform the steel wire further to resemble the final shape of the bolt. The progressive design means that each die makes a specific impression, and the following one will secure previous shapes while adding the next ones. Typically, the first impression will be “on the left side” and the second “on the right side” or “in the middle.”
Forging Process
The cut lengths of steel wire are the poured or fed into the cylindrical part of the forging press, the actual forging being cold forging. The forging press operates at room temperature. It also generates a big force that covers a different range, depending on the size and the complexity of the created bolt. In the case of a medium bolt, it ranges from 100 tons to 250 tons. The force is applied with a quick punch to make sure that the steel fits the shape of the die. The stampers provide from a few to a dozen such strokes, and the bolt, in this case the head at its first impression, is ready. For a standard 6mm bolt, about 150 tons are used.
Dimensionality and Tolerances
The forcing also means that each detail anymore of the bolt design is now clearly impressed. The toleration for each bolt in cold forging is often very tight, with measures counting with a few hundredths of a millimeter.
Rate of Production
In addition, the rate of production is high. In modern cold forging, a machine with a rate of a few thousand bolts per hour is common. For example, a regular producing set would at a rate of about 5,000 to 10,000 bolts make the shift of eight hours.
Energy and Material Efficiency
This step is not only crucial for shaping the bolt but also for its material efficiency. Cold forging is, first and foremost, one of the most resource-using forms of metallurgy. The process has very clear waste rates, as the entire force is, in this case, used for production. A bolt uses about up to 90% of input material as it is only deformed completely into the final desirable shape by the end of the series.
Complex Shape Adjustments
While cold forging defines the shapes and sizes of the bolts at the preliminary casting phase, this process is insufficient to meet the requirements of the specific and often complex designs and mechanical properties. The shapes of most bolts therefore undergo additional processes specifically designed to fine-tune and adjust the preliminary shapes developed by the dies.
Additional Machining Processes
The preliminary shapes developed by dies are subsequently cast to develop specific designs and geometries of the bolt or address other requirements that the forging process cannot address. The processes of turning, milling, and drilling can be used to develop feature of the bolt that meet the requirements. For instance, heads of bolts are frequently produced or adjusted in this phase to secure the locks or mounting. Grooves are typically added to the bolts as well, especially when they must be locked with other mechanisms. Another example is the undercut provided by the bolt in the pictures.
Drilling and Threading
Most bolts must also be drilled to accommodate the locks or the bolts to which they are mounted. In most cases, holes are drilled by CNC machines, and the tolerances of the drill can reach the magnitudes of ± 0.05 mm depending on the bolt. The new thread development needs to be done post-forging. The thread is typically cut, although the rolling is increasingly popular due to improved strength reached through work hardening.
Heat Treatment
Heat treatment is applied to achieve specific mechanical properties of the bolt if the constructed isolate does not require it. If the bolt requires the changes in hardness or fatigue resistance, the temperatures from the tempering operation are applied to change the microstructure of the steel. The steel is tempered at 150°C-700°C for different levels of hardness and toughness.
Addition of a Surface Finishing
Finally, numerous bolts are adapted with precision machining than ground or polished in order to secure improved smoothness and wear of the mechanism. They are typically coated to improve life and resistance to the surrounding, such as corrosion. Standard coatings include zinc coating and black oxide.
Inspection and Testing
The process of bolts cold forging and preparation for this stage are followed by inspection and testing to ensure that each batch is up to the mark. At the same time, such inspection and testing consists of several steps, which will also be considered in details below. Exact follow-up of all these steps is especially crucial as the final production meets the established standards of quality and is ready for specific work.
Dimensional Accuracy Testing
Pre- and post-forging outputs are further subjected to consideration of their dimensions. In other words, during this phase inspectors check whether such parameters as length, diameter, and thread pitch meet the requirements of such products. This is usually done by special devices, which either measure these parameters, such as calipers and micrometers, or consider their sizes in comparison with the required values. These may also be coordinate measuring machines, which are especially effective in measuring multidimensional objects and their parameters in comparison with CAD model constructions to estimate manufacturing accuracy.
Mechanical Property Testing
Inspection experts also test whether bolts in question are strong enough to resist all the stipulated forces they may meet when serving their purposes. For example, such forces may include tensile load, when the bolt is pulled until it stretches to maximum. Requirements for it usually depend on bolt sizes and grades, but high strength bolts usually have a tensile strength of 400 to 1,040 MPa. Hardness of bolts is also tested by Rockwell or Brinell hardness testers, and its orders correlate with exact tensile properties. In fact, tensile properties depend on exact grades and sizes, so orders may vary, but certain hardness requirements should be consistent for the neat materials correlating to exact tensile strength values.
Surface and Metallurgical Inspection
During surface inspection, experts concentrate on the condition of the object’s surface to reveal cracks, burrs, or signs of coating properties. In addition, they may also conduct metallurgical inspection, which ensures how well grains are structured. For all tested outputs, their microscoping is also done to check whether inclusions or segregations are present inside the bolt. This is crucial for ensuring the absence of microcracks and defects by determining proper grain structure by scanning electron microscopy.
Corrosion Resistance Testing
For bolts used outside, these are also tested for their abilities to resist corrosion. For example, salt spray tests are conducted to test bolts’ resistance against salty spray for the same time that is equal to a number of the examinational years. In this case, manufacturers must ensure that after 500 hours no more than 5% of the examined bolts may demonstrate exact red rust with the naked eye.
Final Compliance Check
The other condition of the bolts production meeting all the standards is their confirmation in documents reflecting compliance with ISO, ASTM, or, for example, GMW standards. Only balls with such information may be taken as funal products for their further selling.
Final Modifications and Packaging
In the cold forging process, the final steps for bolts include essential modifications and preparing the bolts for shipping. This stage guarantees that the bolts are in the state of readiness upon delivery, meeting all requirements set by the customer. Throughout the final steps, the use of threading, heat treatment refinement, application of protective coatings, and thorough quality control rechecks are necessary to guarantee the best quality possible.
Threading and Surface Finishing
When the bolts are shaped and the required modifications are made, the threading is usually necessary for the bolts to function. It is commonly completed with the use of a thread rolling machine, which deforms the material of the bolt to create the additional layer of strength and fatigue resistance. This way, threading with the thread rolling method is advantageous as it ensures thorough uniformity of threading throughout all batches. Additionally, surface finishing is usually applied with the means of polishing or deburring to remove the sharp edges and burrs, which may potentially cause an injury or harm to people handling the bolts.
Heat Treatment Refinement
After threading, the additional heat treatment is necessary to improve the mechanical properties of some types of bolts. Depending on the requirements, the bolts may need, for example, tempering, or process of stress relieving. In the case of automotive bolts, tempering is usually applied with the use of a temperature of order of ^\circ C to achieve a uniform and superior level of strength and ductility.
Protective Coatings
Another element of the final steps of bolt development is the application of protective coatings to prevent the corrosion damage. The options for coatings for the exposed to the elements bolts are usually zinc plating, thorough application of cadmium plating, or the application of phosphate layer. Such a choice will depend on the customer’s requirements as well as the exposure environment of the bolt. For example, due to the high corrosion resistance and relatively low cost, zinc coating is one of the most commonly applied options.
Quality Control Rechecks
Before packaging, the final recheck of the completed modifications is performed to guarantee that all requirements of threading, uniformity of heat treatment, and application of protective coatings in specified levels are met.
Packaging for Shipment
The final part of the process of bolts’ development is the packaging for shipment. In this step, the most common approach involves the use of airtight bags with protective agents to prevent the rust damage and ensure that the bolts will not move during the transportation. Based on the size and quantity, the respective amount of bolt bags is boxed, or crated and filled with a necessary amount of packaging filler. The process of packaging also involves labeling, specifying the types and numbers of bolts, as well as their production batch numbers, and handling instructions not to damage the outer layer in bolt’s coating.