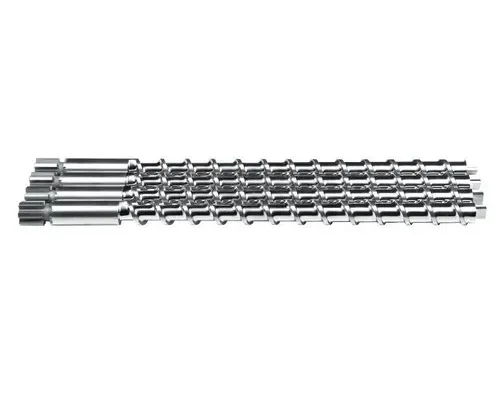
5 Key Principles Of Twin-Screw Extrusion
Twin-screw extrusion relies on five key principles: screw configuration, barrel temperature control, screw speed, feed rate, and material properties, ensuring efficient and precise processing of various materials.
Explore different types of screws
Twin-screw extrusion is based on the interaction of the screws with the material processed. Thus, the selection of screw type is crucial to get desired product properties and production efficiency. There are several key types of screws utilized in twin-screw extrusion:
Co-rotating intermeshing screws. The screws mesh closely and rotate both in the same direction. These screws are the most efficient in material conveyance and mixing and are widely used in compounding and reactive processes. The intermeshing design ensures the best self-wiping of the screw and distributive mixing, which results in uniform properties of the product.
Co-rotating non-intermeshing screws. This screw type also rotates in the same direction and is suitable to delicate material and material causing for minimum shear. The screws provide conveying in a more gentle way since they do not mesh but have a small clearance between them.
Counter-rotating non-intermeshing screws. These screws rotate in the opposite direction, do not mesh, have a clearance, and are utilized in the devolatilization processes that require removing volatile substances. The opposite rotation causes kneading and has excellent mixing and devolatilization efficiency.
Twin-screw extrusion with a barrier flight. In this type assembly, one screw has a barrier flight, which extends radially into the channel of the other screw. Such a configuration results in a restricted channel and screw relative motion, which increases the material residence time and mixing. The assemblies are widely used in reactive processes where intimate mixing is required to start a chemical reaction.
Single-screw extrusion with twin-screw elements. The setup has a single-screw extruder with twin-screw elements in the screw. Such a setup allows getting some advantages of a twin-screw setup, increased mixing efficiency, and improved material conveyance, and retains the simplicity of a single-screw setup.
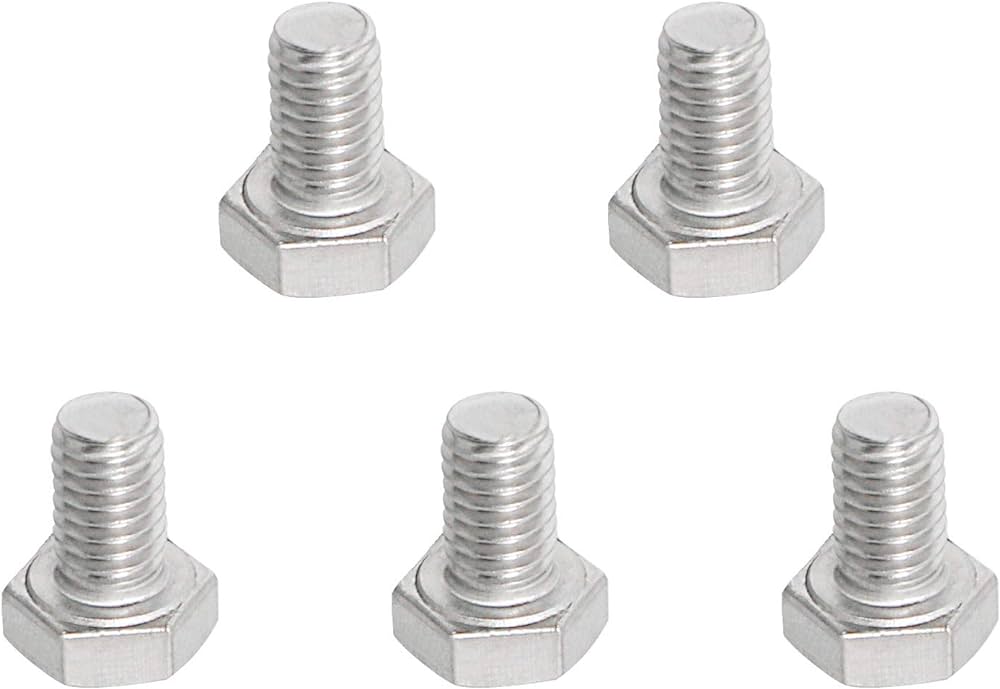
61LMWjIuheL._AC_UF1000,1000_QL80_
Cross-industry applications
Twin-screw extrusion is a highly flexible process with applications in various industries. The following examples of cross-industry applications illustrate that its key principles are applicable in many different settings.
Food Industry
Principle: The formation of end-products is controlled by the configuration of screws and the ability to adjust process parameters.
Example: Production of breakfast cereals, snacks, and pet food. The precision of the twin screw technology enables control of mixing, cooking, and shaping for a wide variety of products which require specific textures and flavors.
Pharmaceutical Industry
Principle: The modular composition of twin-screw extruders and their capability to include feeding, conveying, mixing, and forming units
Example: Manufacturing of tablets and capsules, as well as various other forms of pharmaceutical drugs. The extrusion process enables continuous production of drugs, composition of which remains uniform, and with the release rate controlled.
Polymer Industry
Principle: Adjusting the screw speed and temperature control ensures mixing and heating of polymers, as well as cooling and solidification.
Example: Production of plastic compounds and masterbatches. This process allows for dispersing of additives and pigments, and create new properties of the final product.
Chemical Industry
Principle: The use of shear forces and mixing for chemical reactions and polymerization.
Example: Production of specialty polymers and compounds by conducting reactive extrusion. This allows including reactive components, and producing new chemical entities with specific properties.
Recycling Industry
Principle: The use of twin-screw extruders for compounding and processing recycled materials.
Example: Recycling of plastic waste. The extrusion process is used for blending of different types of plastic, and addition of various additives producing recycled materials.
Learn how it works
The twin-screw extrusion is not a simple process, but rather a combination of several key principles which influence the efficiency of material processing. Knowledge of these principles is vital for all operators to be able to optimize their extrusion processes and product quality. Here is a breakdown of them:
Screw Configuration
Principle: the arrangement of the screws determines the conveying, mixing, and shearing action on the material.
Example 1: Co-rotating intermeshing screws are basically identical versions of the same screw with flights that mesh very closely. Their design is especially efficient for mixing and conveying.
Example 2: When the flight profiles run counter to each other due to counter-rotation, there is a relatively large kneading action which is very suitable for devolatilization processes.
Barrel Temperature Control
Principle: the control over the temperature of the barrels can mostly determine the melt and processing conditions of the material.
Example: In case of the need to gradually cool down the material before processing or cooling it down after melting it, different zones of barrel temperature must be regulated.
Screw Speed
Principle: at what pace the screws rotate can determine the residence time and shear rate of what materials are being processed.
Example: Increasing the speed might increase the residence time and the throughput, as well as the dof the shear rate. However, it also negatively affects the properties of the processed material and the stability of the process.
Feed Rate
Principle: different rates of handling of the material determine the residence time and mixing efficiency.
Example: higher handling rates mean more output. However, they also influence the other rates that must be regulated, namely the screw speed and the barrel temperature.
Material Properties
Principle: the properties of the material, such as viscosity, melting point, and any additives, determine the proper values of all of the above.
Example: the higher the viscosity of the material the higher the mixing temperature and screw speed, if only for proper conveying.
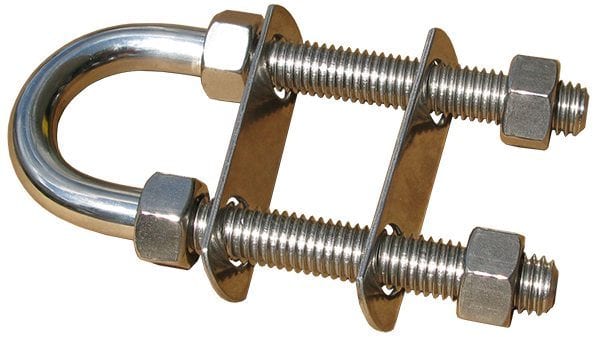
U-Bolt for pulley block – Custom Chutes
Efficiency optimization technology
Twin-screw extrusion is associated with a variety of efficiency optimization technologies designed to focus on process performance and versatility. Generally, these principles focus on the efficiency of mixing, energy consumption, and productivity of the produced materials. Various efficiency optimization technologies can be highlighted throughout the process: process intensification – focusing on throughput, efficient heating and cooling – associated with energy consumption, and various smart control systems and material handling systems. Some of the examples of such technologies are listed below.
Process Intensification
The principle of intensification is aimed at maximizing the throughput of the extruder without having a negative impact on the product quality. The example of such a practice is screw speed, which can be significantly elevated given the developed screw design, allow for substantially higher output rates, and maintain the necessary mixing and homogenization.
Energy-efficient Heating and Cooling
The principle of reduced energy consumption results from more efficient heating and cooling systems. Advanced insulation materials are used, and the heating elements are of higher efficiency to reduce heat loss and improve energy efficiency. Notably, there is a lower rate heating and cooling screw design, which is used to achieve product tempering and pasteurization almost without any consumption of heating or cooling energy.
Smart Control Systems
This principle involves the application of advanced control algorithms. The example is given by focusing on closed-loop control systems, which continuously monitor and adjust the screw speed, barrel temperature, and feed rate to maintain the optimal conditions of the process.
Material Handling Systems
The principle is linked to improved material handling. Automated feeding systems commonly result in more accurate control of the feed rate, with less material being wasted.
Integrated Process Monitoring
This principle focuses on the system of monitoring sensors that help detect and correct deviations in key process parameters. The example of such sensors is those used to monitor the melt temperature, pressure, and torque properly.
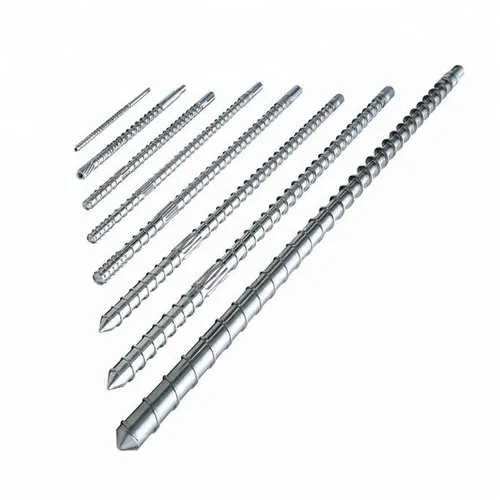
Plastic Extrusion Screw
Mastering twin-screw extrusion
Principle: Correct understanding of material properties is essential.
Example: High viscosity material will require higher screw speeds and temperatures in order to be properly mixed and conveyed.
Optimizing screw configuration:
Principle: Screws are a major part of many material processing systems and are essential for mixing, conveying, and shearing applications; some materials require more intensive mixing than other while others need to be devolatilized.
Example: Co-rotating intermeshing screws are better for high-intensity mixing conditions, while counter-rotating screws are better for devolatilization processes.
Controlling barrel temperature:
Principle: The barrel needs to control the temperature of the material in order to keep it molten and properly process it.
Example: Optimal processing temperature can be achieved by changing the temperature of certain zones of the barrel over time.
Changing screw speed and feed rate:
Principle: The residence time of the material and the shear rate is a determinant of the screw speed and feed rate.
Example: Higher screw speed and feed rate results in higher residence time and shear rate, but will cause stabilization problems.
Monitoring process parameters:
Principle: Process control is only possible through the utilization of various sensors and monitors.
Example: A sensor can be added to the machine to monitor melt temperature and pressure.
Utilizing advanced control systems:
Principle: Systems can be automated which would result in optimal processing conditions and higher efficiency.
Example: Feedback closed loop control can change the screw speed, temperature, and feed rate in accordance with melt temperature and pressure to provide optimal processing conditions and get consistent product quality with low wastage.