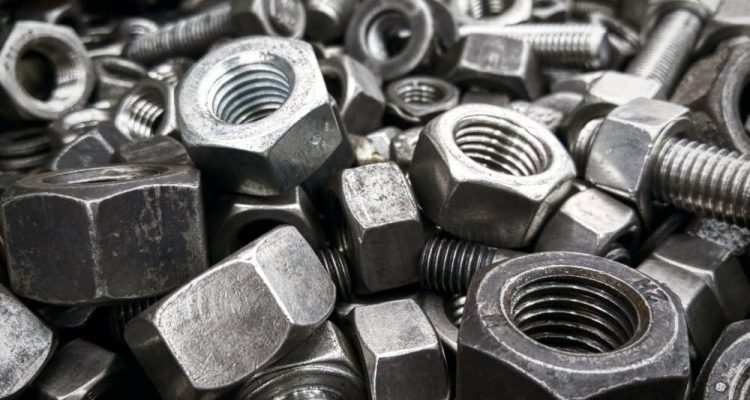
5 Key Bolt Tests And Their Insights
Key bolt tests include tensile strength, hardness, shear resistance, proof load, and thread analysis, revealing vital durability and performance metrics for engineering applications
Tensile Strength Test
Tensile strength testing serves to discover the maximum load a bolt can sustain before breaking. This has become an essential practice not just for evaluating a bolt’s stress resistance but also to ensure safety and reliability.
Setting Up
A tensile testing process starts with the setting up of the bolt in a tensometer. The bolt should be fixed properly and securely at both ends. Fixing is necessary to ensure that the force will be evenly distributed along the bolt’s length. Slippage and excentric shift of the bolt presents risks of disproportionate forces and invalid results.
Applying a Load
A tensile testing procedure implies that controlled force is being applied to the bolt until it breaks. The force is being recorded in Newtons, and the point of force breakdown is recorded and used to help determine the bolt’s strength. This is how the force that will fit the breaking point of the bolt is discovered.
Interpreting the Results
Once the bolt is broken, the data should be reviewed to find out what force corresponds to the bolt’s strength. Then, the tensile strength should be compared with the known levels used in the industry for various purposes. For example, a bolt being used for automotive safety requirements should have higher strength than one used in construction where safety isn’t such an issue.
Real World Practice
In 2018, a major bridge that is used by thousands of vehicles daily was examined closely, revealing multiple suspension bolt failures. Tensile tests involving a number of samples were conducted, revealing the bolts to be of lesser force breaking opportunities compared to that stated in the provisions. As a result, all bolts were replaced to ensure safety and prevent accidents.
Tensile testing of bolts across industries such as construction and automotive is essential for the consistent safety it provides. By developing a schedule for regular tensile testing, companies can avoid potentially costly repairs and damage due to failures that can arise without warning.frequnent.testing.
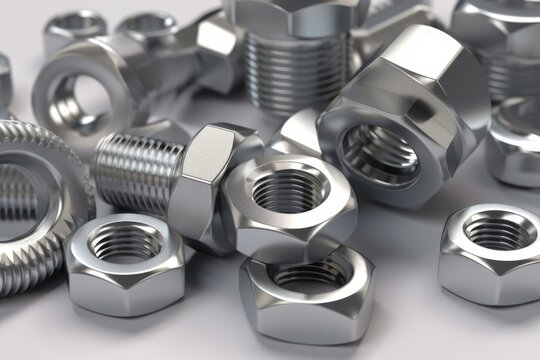
Nuts Bolts Images – Browse 104,912 Stock Photos, Vectors, and Video
Hardness Assessment
Hardness testing is a crucial procedure to assess the bolt’s resistance to deformation and penetration. It provides valuable information on the ability of a bolt to withstand certain forces and tell how well this material will perform under repeated use or extreme conditions. With hardness tests, one can measure how the material might resist further metalworking and how their mechanical features might be suitable for the arrangement.
Selecting the Right Test Method
There are many kinds of bolt applications, and the hardness of a bolt can also be measured by many methods. The best method must, therefore, will depend on the bolt and its application in the first place. The most commonly used hardness methods include Brinell, Rockwell, and Vickers test. In every case, a different approach might be used to measure the degree of the bolt’s resistance, usually the bolt’s indentation, under a static load.
Preparing the Bolt
Before hardness testing, prepare the bolt by cleaning its surface and removing any coatings or substances that might degrade the quality of results derived from the test. If drinking fluids must be used in the bolt’s preparation, remove them using a soft cloth. Preparation is often a valuable step that allows readers to perform the most consistent reading and give confidence in their measures.
Conducting the Test
During the hardness test, introduce a hard indenter and subject it to a specified forced load or pressure, measured in force per unit area. Measuring the depth or size of the indentation on the bolt’s surface, it is directly related to the material’s hardness. Measurements must use consistent conditions and procedures each time they are conducted.
Interpreting the Data
Record the hardness test results and record whether it is in the same unit measurement or converted into Standard International. The score given after the test is then interpreted on the standard hardness scale and represents the rating of the bolt’s hardness. If you are using a Rockwell test, greater hardness values represent harder materials rats. As all measures are carefully selected at the lab, measure how high-end stresses the bolt will frequently encounter in their application.
Real-life example of hardness testing
In 2016, an aircraft manufacturer found that some bolts were being used in essential aircraft parts and not being of sufficient hardness. Certain private organizations conducting critical examinations for the company made a routine assessment of a stockpile of bolts. In the end, it was decided that the best way to prevent failures was to replace all tested aircraft components before any recorded failure ever occurred. The new hardness testing method proved vital in detecting the likely dangers of the detected bolt head’s reduced hardness and avoiding the potential skull associated risks.
Ensuring compliance and quality
Hardness tests are a critical part of the manufacturing process. With the regular dormant testing of bolt hardness, the manufacturer can provide both standard requirements and a guarantee that the available roughness will meet customer expectations. In this way, they are aware that the sensible style of materials and items maintains the reliability and whether the dormancy testing methods are the most suitable ones.
Shear Strength Assessment
Shear strength testing is essentially the testing of whether a piece of bolt is functional or operational by assessing whether it can withstand forces that tend to force the material to slide or fail across a plane. It is used in all engineering fields to test the integrity of bolts. It is used to tell the strength to which a bolt has to be sheared perpendicularly to the axial forces in case a bolt experiences lateral forces. The force is recorded in kilo-Newton of kilopounds, and this data is essential to computer-aided designers, hobbyists, builders, or anyone interested in conducting safe structures using the bolt. The testing of whether the force needed to shear the bolt fails is essential, and the results must be reproducible.
General Understanding of Shear Strength
This is the material’s ability to resist a maximum shear stress load per unit area; that is, it is the tendency to resist forces tending to cut across the material. For bolts, it is the measure of capacity to resist the load without shearing off when force is applied to the bolt perpendicularly to the axial direction. The testing measures force to be sheared when the bolt is under lateral force. The features tested include the absorbance, the compression, and the tensile specifications of the bolt.
Practical Infrastructure Impact
For infrastructure development, the most apparent example would be to add the testing of the starting bolts for a critical suspension bridge. The bolts were sheared under the force of weight below that which the bolts should have contended with. The investigation was done, and ways were evidenced how the bolt failed to meet the required strength. The later testing was done and the bolts replaced, and the bridge became very successful.
Importance of Shear Testing
The testing is essential because the making of the product is intended to accomplish a specific performance during normal duty. Filure to test may mean the item’s material is not up to duty and thus unable to manage the expected shear stress. This may seem cumbersome for companies that fail to test their tools because they do not have proper systems in place. The most successful companies in the industry such as tools and automotive industries have already included the testing as vital. Without testing, the future has the potential to cause crashes resulting in injury, death, or costly liability consequences.
Conclusively from the discussion, the testing of whether a bolt fails under stress due to forced shear is essential. The results provide the data used by other engineers and builders to determine the bolt’s correct length. Testing is also beneficial in the adjustment of the force under which the bolt to be sheared can only be cut.
Proof Load Verification
Proof load verification is a critical test in bolt manufacturing and quality assurance. Its purpose is to prove that bolts will perform according to specifications under the expected loads. A proof load test involves applying a load to a bolt, which is slightly less than that at which the bolt should fail but is more than the expected working load.
Test Concept
The proof load test involves pushing a bolt under a specified type of load. This type of load is usually the maximum load expected for the bolt. The load, however, will be lesser than that leading to its failure. The objective of the test is to prove that the bolt will be able to sustain the applied load without any deformation. In other words, the load is the proof for the bolt’s capability to address further application loads.
Test Performance
The bolt is set in a machine to complete the proof load test. A force is applied along the bolt’s axis, which is continuously increased to the defined proof load value. Once the force is applied, its value should be stable for a specified period, usually 10 seconds. There should be no signs of any yielding or permanent deformation. After the test is completed, the bolt is analyzed. If no damage or deformation is found, the bolt is considered to have passed the test and is ready to be used in real conditions. All measurements and the exact test results should be registered in the testing documents.
Application
In the company A’s case, the bolts intended to be used in aerospace applications were tested by the proof load method. During the test, the proof load status was not met, which lead to the in-depth investigation. The report showed that the bolt failure was caused by a material inconsistency from a new vendor. After the problem was solved, all bolts were renewed, and the supplier was required to submit a material test report on weld fillers. In conclusion, the proof load verification is important in high demanded applications, such as construction, and aerospace. All bolts used in such assemblies should be tested periodically to have the ability to sustain the load. No bolt should ever be accepted until its conditions are checked.
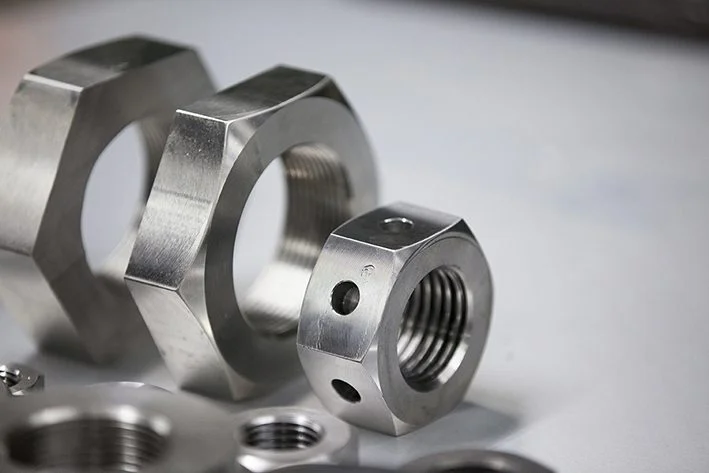
Nut Testing – BES Group
Thread Type Analysis
Thread type analysis is an important element of any bolt testing procedure: it allows testing if the thread design meets specific engineering needs and standards of strength, compatibility, and function.
Understanding Different Thread Types
There are numerous types of threads: metric coarse, metric fine, UNC and UNF, BSF, BSW, and many others. Practically any type of threads has its specific needs and applications, and it affects the performance and suitability of a bolt in some way.
Testing Procedures for Thread Analysis
The procedure begins with a visual component that identifies any manufacturing deficiencies of a bolt. After that, the detailed dimensions are taken with calipers and micrometers to test if thread pitch, angle, and diameter meet the standards. For more sophisticated analysis, optical and electronic profilometers can be utilized to obtain the detailed dimensions of thread geometry.
Performance Analysis Based on Thread Type
The main method of testing bolts based on thread types includes the level of performance of threads in conditions similar to real-life usage. It is done with torque testing of how tightly the bolt can be screwed without its collapse or thread stripping and tension testing of how much axial load the threads can withstand without yielding.
Real-Life Example of Thread-Type Testing Application
In 2017, during the erection of a new high-rise building, the construction site used bolts of incorrect threads to secure the critical joints. The threads, in fact, were mismatched to the bolts in use because of their insufficient load distribution. As a result, threads as ultimate hotspots were the first to yield, results in a failing joint. Realize that, the subsequent analysis of the threads unearthed the problem, and bolts satisfied the needs of the project were implemented. Overall, thread-type analysis is one of the most important elements of quality control when building anything from a new airplane to a chair.