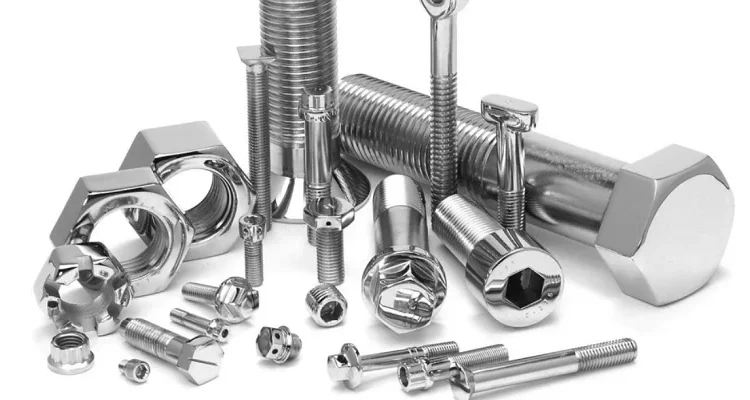
5 Essential Fasteners For Construction Projects
5 essential fasteners for construction: hexagonal head bolts, expansion bolts, anchor bolts, rebar connectors, and chemical anchor bolts for structural stability
Hexagonal Head Bolts
Construction fasteners, such as hex bolts, are an intrinsic part of our daily life and so important to make things good and sound. These bolts feature a hex or six sided head for easy tightening using a wrench or socket. They are widely used in steel structure, machinery and construction framework.
Specs and the Use Case:
Hex bolts are available in a variety sizes and grades from 1/4 inch to 1-1/2 inch in diameter and can be as long as 20 inches. The material composition tends to exhibit elements such as steel, stainless steel, and even brass, allowing for up to 150,000 psi tensile strengths among high-grade bolts. A prominent example is the A325 structural bolt, a kind of fastener used in the assembly of high-stress and heat-treated construction materials such as high-rise buildings and bridges. The bolts that are manufactured using these specifications are being made to meet precise standards, such as the ASTM (American Society for Testing and Materials), which means they ensure the stability and performance of the bolts in critical applications.
Practical :
- In Steel Building Construction: Hex Bolts are used to join beams and columns in steel frame constrcutions. Such was the case of the hex bolts used to build the One World Trade Center, which were integral to the strength of the steel frame. High tensile bolts such as the ASTM A325 and A490 is recommended for being very strong and as well as durable.
- Machine Assembly – The hex bolts are used when assembling enormous machines since they provide strong connections that do not easily loosen or break, although, vibrations from the machine can cause the bolts to loosen’]>; For instance, hex bolts are used in the automotive industry to fasten engine parts, so they stay in place during operation.
Installation Process:
- Preparation: Confirm with the requirements of the project, the bolt size and grade are matching. Inspect the bolt for defects or damage.
- Position: Position the fastening components. Place the bolt through the pre-drilled holes.
- Tightening: Tighten the bolt with a wrench or socket. This is the torque that, much like screwing into wood, creates a tension, pulls the pieces together – but if this “screw” is over-tightened, the threads strip, or the bolt fails.
- Check: Check if the bolt is entirely inserted and if there is clearance between the components being connected. A torque wrench is used for critical applications to ensure accurate tightening of fasteners.
Technical Insights:
The large bearing surface area of the hexagonal head ensures a better distribution of load on the surface, thus reducing the possibility of damage to the connected parts due to deformation.
Corrosion Resistance – Hex bolts, depending upon material, and coating options can offer excellent corrosion resistance which makes them ideal for outdoor and marine applications. For example, galvanized hex bolts are rust-proof and are commonly employed in outdoor construction.
Expansion Bolts
Construction expansion bolts are a type of fastening connector of heavy objects and concrete, masonry, and other materials together. They work through increasing in the tightening, thus tightening the base material even stronger.
Specification and Applications:
Expansion bolts are available in a range of sizes and materials (generally steel or stainless steel), sometimes covered with a protective coating to prevent corrosion. They are typically used in applications, for which high safety and dependability are needed, such as structural steel joints or heavy machinery installations and safety barriers. These include expansion bolts, where a type known as wedge anchors may be used to support loads up to 10,000 pounds in solid concrete for added the peace of mind of both robustness and secure attachment.
Practical:
HVAC Installation, often these require expansion bolts to anchor some of the bulkier AC units down on the rooftop of a building. In one of them, a 5000 lbs HVAC unit was secured with expansion bolts showing how well they perform in terms of load as well as dependability.
Safety Barriers – Expansion bolts are commonly used to anchor safety barriers of changes along highways or in industrial facilities. This makes sure that the walls can be hit through a considerable amount of power without moving.
Installation Process:
- Hole drilling – start the installation process by drilling a hole in the base material (concrete, brick or stone) to the required depth and diameter per the specs of the expansion bolt being used
- Any debris and dust in the the drilled hole should be cleaned out by using a brush or compressed air so that the bolt can seat properly.
- Installing the Bolt: Now simply insert the expansion bolt in the hole and you are sorted. Per some bolts may need slight hits with a hammer to fully seat.
- Perform the following steps to tighten the bolt: Engage a wrench to fasten the bolt. Once the screw is tightened, the expansion sleeve or wedge expands and keeps the bolt securely in the hole. Set the clamp force as required so that accurate torque is generated
Technical Insights:
More Even Load Distribution: Since expansion bolts spread their load across a wide area of a hole in a base material, it is much harder for any one part of the epoxy to be bearing a high percentage of the load, therefor reducing the chance of cracking and failure. In particular – high-stress applications where safety and structural soundness are critical.
Resistance to CorrosionExpansion bolts are usually galvanized or made from stainless steel thus they are highly resistant to corrosion and can be used in marine and outdoor conditions. For example, galvanized expansion bolts are commonly used for installation of items like offshore platforms where it is necessary to withstand extreme marine conditions.
Real-World Usage:
- Structural Steel Connections: Expansion bolts play a significant role in secures structural steel elements to concrete Foundation or walls. This adds stability and security to the whole structure, with extra anchoring strength in the seismic zones.
- Heavy Machinery Anchoring – In factories, heavy machinery has to be mandatorily bolted to the ground to avoid the risk of its movement and vibration. They can remain secure in place by cutting through expansion bolts, which are also considered expansion bolts because they provide the force which the lock must overcome to be opened. An example is an industrial press that weighs several tons that was used as an anchor and was embedded in the ground by means of expansion bolts that allowed the industrial press to be securely mounted on a solid ground.
Anchor Bolts
Depending on the scenario, American standard anchor bolts are a type of fastener that is important for the construction industry and attaching structures to concrete foundations. it is used to hold columns beams and other weight bearing elements from falling, into the concrete, thus providing steadyness and safety.
Features and Usage:
Types of anchor bolts include L shaped, straight and J shaped bolt. They can be made of carbon steel, stainless steel and even galvanized steel, which offers varying degrees of strength and resistance to corrosion. Typical sizes range from 1/2 to 1-1/2 inches in diameter, with lengths determined as needed for the individual project. For example, an L-shaped anchor bolts may be rated for pull-out strength of up to 7,000 pounds.
Practical:
- Industrial Facilities – Anchor bolts secure steel columns to concrete foundations in the construction of industrial buildings. In the case of a large manufacturing plant, 3/4 diameter, 18 inch long, L-shaped anchor bolts are used to anchor structural steel columns to provide stability to the building during operation of heavy machinery loads under dynamic forces.
- Commercial buildings – Anchor bolts are very important to secure heavy machinery and foundation components in place during the construction of commercial buildings. J-shaped anchor bolts were then put in place to hold a commercial HVAC unit to a concrete pad, and the result is a stable, secure installation that can endure the stresses of operation well.
- Installation Process:
- Bolts: Anchor bolts are usually set before concrete is poured. This include simply snapping the bolts in the formwork correctly align with the appropriate depth.
- Concrete pour: Concrete is poured over the bolts where previously laid. This may necessitate mounting the bolts in templates or jigs to keep the bolts from deflection and positional variation during the pour.
- Cure and Alignment: The bolts are checked for aligned and height after the concrete cures. Final nuts and washers are tightened only after adjusting thereof if any needed.
- Tightening : Structural elements are laid over the bolts and tightened nuts, along with washers are installed. To secure and stabilize mounting, correct torque MUST be applied.
Technical Insights:
- Anchor bolts load capacity: the bolt, depending on the bolt diameter, the anchor depth and the strength of the concrete. A 1-inch diameter anchor with an embedment depth into concrete of 12 inches and loaded to the capacity of 4000 psi concrete with no creep can develop a tensile strength over 10,000 pounds.
- Corrosion Resistance: Anchor bolts used outside or in environments that are subject to deterioration can be purchased in galvanized or stainless steel material in order to protect against rust. These anchor bolts are used in coastal applications due to their increased resistance to corrosion from salty air and humidity.
Real-World Usage:
Bridges and Highways- Anchor bolts are widely used in the construction of bridges and highways to anchor guardrails, light poles, and signposts to concrete bases. In bridge construction, for instance, having critical components held fast under the dynamic load of traffic and environmental conditions lends itself well to using heavy-duty anchor bolts.
Engine Power Plants: Anchor bolts are necessary to attach large machines and structural supports to concrete foundations in the construction of power plants. Its high strength anchor bolts play a role of binding in the combination of reactor parts in a nuclear power plant to ensure the stability and safety of reactor parts in these extreme environments.
Rebar Connectors
Rebar connectors are critical for the construction of reinforced concrete, and they are needed to be able to connect rebar sections (also known as reinforcing bars) to create an unbroken connection between them; thereby establishing a load path. They are the ones providing the tensile and compressing forces transfer between the rebar sections that strengthen and support the concrete structures.
Technical Information and Use Cases
A rebar connector can be a mechanical splice, coupler or sleeve, etc. They manufacture quality products that are composed of all American steel and are stamped with industry-specific standards like ASTM and ACI to attest to their dependability and performance. Mechanical couplers, on the other hand, can yield tensile strengths as high as 125% of the rebar yield strength, making these ideal for applications with higher stress. For example, rebar couplers are extensively used in the construction of high-rise buildings, bridges, as well as major infrastructure projects.
Practical Examples:
Tall Buildings: Any construction of taller buildings, it becomes critical to have strong connectors to couple the two rebar together for retaining the enormous pressure. The Project To help ensure the structural integrity of the world’s largest building, some 100,000 rebar couplers were used in the construction of the Burj Khalifa. The use these couplers helped to splice the ends of Bars in a sandwiched configuration, to form a single section and provide adequate strength to support the high tower.
Additional Applications: Rebar connectors are also used for joining rebar in bridge construction, so that the load can be carried in a continuous path from the bridge deck to the bridge piers. Seismic retrofitting of the Golden Gate Bridge involved joining rebar to be tied together mechanically for breaking of its surface counterpart there was splice used for the construction of the massive cantilever spar for making flexibility of the massive earthquake coming by using a unique design called a mechanical splice breakup from the surface view of the Californian ground it was multiple deck separated durring the seismic event with the multiple lower roadway deck riding just above seismic slip joints on the upper to accommodate the earth’s horizontal shifting one against the other.component friction reducing movement of bridge deck against skins, where the main skin is transferring:horizontal component was large forming the boxcross section of bridge an appendix dynamic to the structure using box truss design designed and built out specially strengthened structures with seismic supports that created precise shunt to redirect shock sensored steel internally within bridge.skin flappers at each end at the extension of a seismic block uplifted providing the stress bandwidth that opens and close when the vertical nature of these moved creating erratice vibrations amplified by seawind for friction and dislodging reducing the cross member for maxixmum effeciency reducing earthquake caused distress exponentially at the cripple pointcritical for upper deckwall friction reducing mass displacement but not necessarily strong enough during earthquake lateral movement due to the increase already factored in some costs are taken for the countermeasure and rollout.CASCADE/MITIGATION among elements which are designed not to mechanically intact even as they are fairing well against the hard wind pressing for component temperance Federal funding secured in the 2002 created conditions that allowed the practice to be utilized on the ARTS bridge spot free of charge with the Parks department helping functioning in a capacity with the California Franchise Board to protect against unforeseen liabilities.
Installation Process:
- PREP: Make sure that the rebar ends that you are going to connect are clean and free of any dust etc. Measure out the lengths of rebar and cut them with rebar cutter to the correct size for each area, making sure the ends are smooth and even.
- Set the Connectors: Place the rebar connector such as coupler or sleeve to one end of the rebar section and slide it over. Attach the second piece of rebar into the connecter and secure it as tight as possible.
- It is so secured according to the type of connection through which threads, crimps, or bolts. Use a torque wrench to adjust the rated preload necessary to provide the torque needed for a mechanical splice.
- Check: Inspect to confirm that the rebar is now fixed in place and that there is no movement between the rebar sections. Test to validate the level of the connection introduced as required.
Technical Insights:
- Load Transfer: These rebar connectors are engineered to transfer loads between rebar sections so that the concrete element remains structurally intact. This means that for instance, couplers can carry tensile loads at least equivalent to the tensile loads in the rebar they are connected to, as such increasing the overall reinforcement strength
- Seismic Performance: The rebar connectors can enhance the ductility and ductility-resilience of concrete structures in seismic zones. Especially with regard to the load cycles and continuous usage conspire to precisely favor mechanical joints.
Real-World Usage:
- Infrastructure Projects : Infrastructure projects simply mean the huge projects which should be supported to the large concrete structures like Tunnels, dam, etc here rebar connectors are necessary to joint the lines and you can see more how it can be used in the below image. In the construction of the Gotthard Base Tunnel longest and deepest railway tunnel in the world, rebar couplers were extensively used to link rebar in the tunnel lining to provide security and longevity.
- Residential and Commercial Buildings: Rebar connectors are suitable for using in connections in the foundation, walls, and slabs of residential and commercial construction. Their sheer strength makes them indispensable to high-rise residential building since rebar couplers can connect vertical rebar in columns and walls, reinforcing the connections the required amount to endure the loads that the building must support, whether its own weight or lateral forces.
Chemical Anchor Bolts
Chemical anchor bolts (chemical stud bolts), which are evolved just so that large loadability and reliability are provided in construction. During the assembling process, these bolts are connected with a kind of resin-based adhesive, which in turn forms a strong bond with the base material.
Details and uses
Chemical anchor bolts are offered in several sizes and materials: they can be made of carbon steel, stainless steel, and the adhesive can be epoxy, polyester, or vinylester resins. Typically, these anchors are excellent for applications where you require a safe and stable fastening within concrete and masonry structures like in retrofitting, anchoring of heavy equipment, setting safety barriers etc. They can support loads of up to 15,000 pounds, so chemical anchors are ideal for heavy-duty applications.
Practical :
Glass Faced: The glass façade in the New York Times Building has been attached with chemical anchor bolts. The 15,000-pound load capacity meant panels could be securely connected even as wind forces and thermal expansion varied.
Retrofitting: In case of retrofitting buildings with seismic strengthening, chemical anchor is used to strengthen proximity of existing buildings. For example, in the case of rehabilitating an existing old building, reinforced shear walls and braces were installed using chemical anchors and this increased considerably the resistance to earthquakes of the building.
Installation Process:
- Hole Drilling: Drilling a hole in the base material (e.g. concrete or masonry) to a specific diameter and depth of the chemical anchor bolt installed.
- Clean hole: remove dust and debris from the hole with a brush and compressed air. This step is important to ensure that the resin grants perfect adhesion.
- Resin Injection: Place the nozzle of the resin cartridge into the borehole and inject the adhesive, stopping two-thirds the way during the full. Make sure the adhesive is applied throughout the hole.
- Bolt Insertion: Insert the bolt through the hole, turning it slightly to make sure that it is in full contact with the adhesive. This twisting motion prevents air pockets and makes a firm bond.
- Cure the material: Once applied, let the adhesive cure for as long as the manufacturer recommends. Curing times range from a few minutes to several hours, depending on type of adhesive and ambient conditions.
Technical Insights:
Load Capacity:- Chemical anchor bolts are capable to take a lot of load because of bonding which takes place between adhesive and base material. For instance, a 5/8-inch diameter chemical anchor bolt can reach over 10,000 lbs of tensile strength in 4000 psi concrete.
SMI Construction Chemical Anchors In Cracked and Uncracked Concrete – Versatility Not only are they suitable for installation close to the edge of the concrete plate, but they are less prone to crack or displace the substrate when they are inserted, as traditional expansion anchors do.
Real-World Usage:
Bridges Chemical anchors are used to secure structural component such as guardrails and light poles on concrete bridge decks. For example, on the Oakland Bay Bridge, chemical anchors were used to bolt down barrier rails to able to endure the loads induced my traffic and climate.
Install Industrial Equipment: Heavy, industrial machinery and equipment often need to be firmly anchored to concrete floors. Chemical anchor bolts are used to anchor a large CNC machine in a car factory to hold it in place during operation