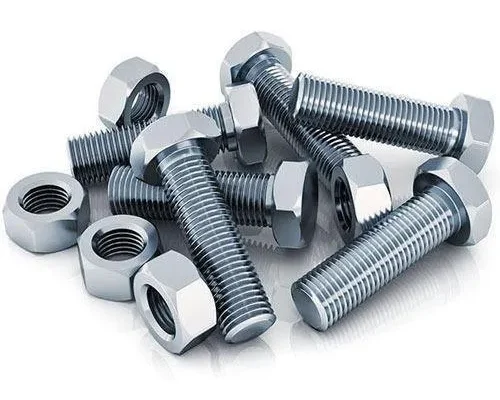
5 Classifications of Custom Bolt Material Types
Custom bolt materials, such as stainless steel, alloy steel, titanium, brass, and Inconel, profoundly impact durability and performance across various industries.
Table of Contents
ToggleStainless Steel Bolt
Stainless steel bolts are widely used across numerous industries due to their exceptional resistance to corrosion . As a rule, they contain chromium, which forms a thin and protective oxide laye r on their surface, preventing rust and ensuring lasting. The main advantages of stainless steel bolts are the following:
-
Durability. Stainless steel bolts are resistant to extreme temperatures and can be used in conditions ranging from -200°C to 1100°C . Hence, they are perfect for construction, where the build quality is of utmost importance.
-
Resistant to corrosion. The quality that distinguishes the stainless steel bolts from other types is their unique corrosion resistance . High chromium content that varies from 10% to 20% prevents rust, meaning they do not have seat in such aggressive environments as chemical plants or marine.
-
A wide range of grades. Stainless steel bolts come in various types, and each is designed for use in specific fields. For example: Food processing and chemical industries use 304 stainless steel bolts for a broad application range ;
For heavily salty water, 316 grade of stainless steel bolts is more resistant to corrosion, so is well-suited for large vessels .
-
Versatility. Almost all possible-fields industries use stainless steel bolts. Their wide application can be explained not only by their high resistance to rust but also by their strength, presentability and no-to-low-cost maintenance.
-
Cost-effectiveness. Given the bolt characteristics and their higher price compared to ordinary carbon steel bolts, stainless steel items in the long run prove to be cheaper due to their durability and low maintenance cost.
-
Installation. One should remember that their proper installation requires specific tools and certain precautions: never install a lubed fastener without also providing proper torque . Galling will ruin otherwise perfectly good stainless fasteners. Make sure compatible washer is used, and restrict the use of thread lubricant to only those products specifically formulated for this type of installation.
-
Aesthetic appeal. One should not forget that stainless steel bolts are excellent not only in quality but also in design. The bolts look great on facades, balconies or other architectural designs.
There are several reasons for stainless steel bolts to be the best possible alternative in the situation. One of the main reasons for using these elements is their full recyclability: while some practical considerations contribute fully to stainless steel bolts’ long life, it is one of the most environmentally sound choices for general-purpose application. The second factor is ongoing innovation, and research in metallurgy contributes new varieties of alloys and new production methods, leading to the development of stainless steel screws that are better, stronger, and more efficient than older alternatives. Thirdly, it should be noted that stainless steel fasteners are and always have been near-synonymous with reliability. Stainless steel bolts provide high performance in various settings, continuing to operate in various environments and under increasingly harsh conditions. Fourth, as is applicable to all industry/domestic quality products, stainless steel bolts will always be top quality and ready for the job provided they comply with industry/general standards. Fifth, the market sees rising demand and consumption of stainless steel bolts all over the market, as construction, infrastructure, and industrial growth continue. Sixth, the practicalities of the modern business also stipulate the need for the coproduction of bolts and material science experts or bolt end-users. And, finally, only high-level front-to-end and back-to-back programs can consistently deliver high-quality secure stainless steel bolt inventories on time.
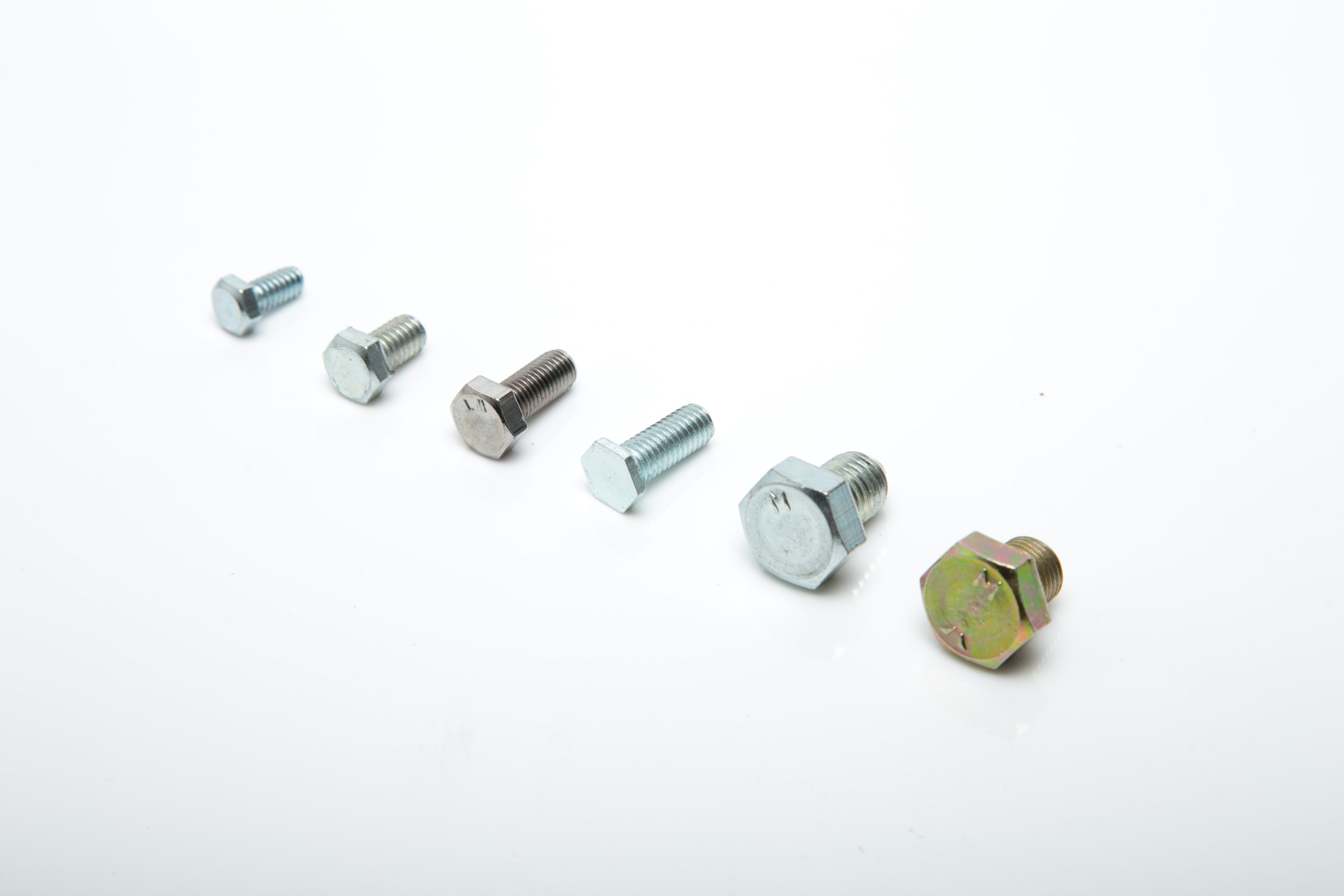
Carbon Steel Bolt – Rainbow Hardware – Fasteners Specialist Made in Taiwan Since 1980.
Titanium Alloy Bolts
The best of the best when it comes to fastening technology, titanium alloy bolts offer several distinct advantages such as resiliency, light weight, and corrosion resistance. As the most common material for bolts, the titanium bolts me primarily made of titanium with additions of small amounts of aluminum and vanadium to form the alloy. Arising application include aerospace, medical implants, and other high-performance applications.
-
Strength-To-Weight Ratio: the primary advantage of the titanium alloy bolts is the remarkable strength-to-weight ratio, significantly outpacing steel. Since the titanium metal has an average density that is about half as substantial as steel, it is possible to create bolts that are twice as light while still being as strong. As a result, titanium bolts have the highest ratio of any bolt material and are well-suited for use in aircraft and cars.
-
Corrosion Resistance: the most extraordinary feature of titanium alloy bolts is the impressive resistance to corrosion. These bolts are unaffected by salt water and all forms of realistic chemical processing, making them well-suited for any working environment. Titanium is so corrosion-resistant since exposed to air, the metal forms a thin skin of oxide that protects the titanium beneath as it heals and reforms on its own when damaged.
-
Biocompatibility: titanium alloy bolts are among the most popular materials for medical implants due to their outstanding biocompatibility. As exceedingly few metals are toxic to the human body or form dangerous compounds with other organic material. As a result, titanium alloy bolts are utilized for various construction elements without the risk of reactions or biological hazards.
-
Temperature Tolerance: titanium has a relatively wide volatile temperature range. Able to function at temperatures as low as -250°C and as high as 600°C, titanium alloy boats are suitable in aerospace applications. Being able to function while both room temperature and up to multiple hundreds of degrees in exceptional cases makes for a versatile and flexible bolt.
-
Fatigue Resistance: the titanium alloy bolts offer fantastic fatigue resistance, which protects it from cracking under repeated loading and unloading at highly stressed areas. The metal does not rust under normal conditions and maintains peak operational capacity despite the circumstances after extensive use.
Introduction: High-strength, resistant to corrosion and most aggressive media due to high chemical activity titanium alloy bolts are widely used in aerospace, science, and medicine. The manufacture of titanium alloy bolts requires the use of special equipment and the highest professionalism and precision, since the alloy has the highest strength and low thermal conductivity.
Cost of titanium alloy bolts: Titanium alloy bolts cost much more than comparable steel products. However, due to the long service life in highly corrosive environments, the titanium bolt will pay for itself in a few years, as regular replacement of steel bolts will be more expensive in total. In addition, the use of titanium bolts reduces the fuel consumption of aircraft, and the positive effect increases along with the speed and altitude of flight.
Surface treatment: Titanium bolts can be coated in different metals for better performance, for example, anodizing or nitriding.
Quality control: NDT and measurement of all characteristics in accordance with the specifications is a long and most important operation, since only the most correct bolts can be used in critical conditions.
Certification : Aerospace or medical company application titanium alloy bolts must have certification to alloy standard.
Recycling and environmental impact: Titanium has all the advantages and disadvantages of the extraction of rare-earth metals. On the one hand, it has a high cost and is not limited. However, the increased energy consumption during processing and the need to meet environmental regulations requires the development of recycling technologies. At the same time, due to reduced fuel consumption and reduced production costs due to less corrosion of equipment and pipelines, titanium complements the purpose of a “green” metallurgy.
Innovation and research: The most important industrial development are new alloys and production technologies for titanium alloy bolts.
-
Collaboration and Partnerships: Working together with researchers, manufacturers, and end-users could enable collective learning and innovation in the titanium alloy bolt space. This could help the members address industry challenges, and develop products that are in tune with the requirements of different applications.
Nickel Alloy Bolts
Nickel alloy bolts are designed to provide superior performance in extreme conditions by taking advantage of the unique capabilities of nickel and other alloying elements. They are commonly used in the chemical processing, petrochemical, and power generation industries, where resistance to corrosion, high temperatures, and mechanical stress is needed. A number of properties of nickel make it particularly suitable for these applications:
-
Resistance to corrosion.
The outstanding property of nickel is its resistance to corrosion. In various environments where the pressure is caused by chloride ions, sulphuric acid, and caustic solutions. At the same time, the resistance to corrosion in oxidising conditions is provided by an active corrosion system resulting in the formation of a passivating oxide film on the metal’s surface.
-
High temperature properties.
The melting point of nickel is around 1455°C, which ensures that it can be used in the conditions of high temperatures provided that the bolts are used for furnaces and gas turbines.
-
Creep resistance.
Nickel has good creep resistance, which means that it is not being deformed over time while being in high-temperature conditions and sustaining mechanical stress . This is particularly important in the area of steam installations and turbines in general. There are other conditions under nickel alloy bolts ensure optimal performance in various other conditions:
-
Chemical compatibility.
Nickel alloy bolts are compatible with the majority of the existing chemicals or fluids used in the process. They are, therefore, commonly used in the chemical production and processing processes. Overall, nickel alloy bolts offer excellent properties to ensure that they are not being affected by either pressure or temperature, making them indispensable to the modern industry.
When it comes to manufacturing nickel alloy bolts, it is essential to ensure certain features and pay attention to possible concerns. One of the materials’ high points is its weldability, allowing for easy and convenient usage. However, at the same time welded parts remain durable and resistant, maintaining their resistance to corrosion. Meanwhile, nickel alloy bolts usually require precise machine work, using computerized milling, turning, grinding, and drilling for the best results. Another feature, enhancing the service life concerns additional surface coatings and sprayings, improving corrosion- and wear resistance.
Moreover, to ensure the reliability and quality of the components, numerous quality control tools and techniques could be employed, such as non-destructive testing for the welding parts. The main concern for the nickel alloy bolts is mainly their high cost and incompatibility of the materials. The regular steel bolts are usually much cheaper and could be stronger while still being highly compatible with the materials. To reduce expenses, manufacturers, therefore, have to order special materials in large bulks.
Meanwhile, the nickel alloy bolt performance is highly regulated and mandatory adhered to accepted standards. The main concerns revolve around the versatility and wide use of the bolt, and numerous existing standards allow for crafting such components according to user needs while ensuring their durability and high quality. Finally, the craft is still undergoing changes and updates due to the advancing research in the area. New alloys and components are produced all the time, and research further drives tech improvements in bolt production.
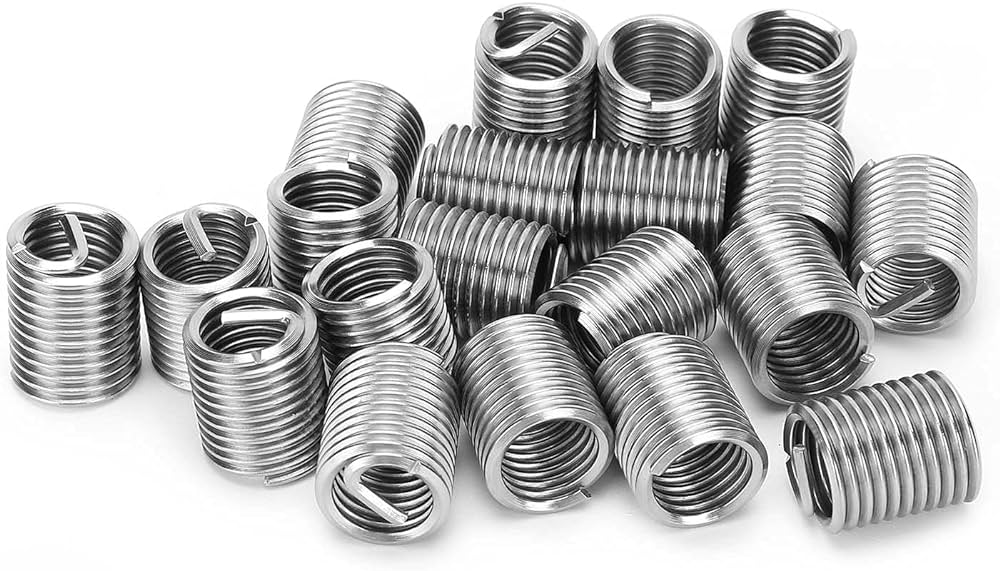
Thread Reducing Nut
Carbon Steel Bolts
Carbon steel bolts are one of the most widely used types of fasteners. They are used in construction, machinery, and automotive production due to the fact that these bolts are inexpensive and easy to manufacture. Their composition primarily consists of two metals, iron and carbon, and they are often used in the case of moderate mechanical stress and atmospheric exposure. Speaking of the pros, there are several substantial advantages: strength, affordability for users and manufacturers, ease of production, various grades, and corrosion resistance with specific methods of protection.
Strength and Durability
Carbon steel bolts have a tensile strength ranging from approximately 60,000 to 100,000 psi depending on the grade and heat treatment . These bolts have a high strength level and are commonly used in situations where high loads occur.
Affordability
Another advantage of carbon steel bolts is the price. They are made of cheaper materials than alloyed fasteners and have simpler production technology that, in turn, affects the production cost. This fact allows using carbon steel bolts for various construction and industrial projects without losing their effectiveness.
Ease of Production
By virtue of composition and structure, carbon steel bolts are easy to manufacture using traditional methods such as forging, machining, and heat treatment . The latter also facilitates a speedy guidance in production, which is why it is very easy to produce large volumes of products.
Grades
Carbon steel bolts come in different grades, and each has its own mechanical properties. Grade 8 bolts are the hardest of all carbon steel bolts and are used as heavy-duty fasteners in, for example, shock suspensions in machines and automotive vehicles . Grade 2 and Grade 5 are the types of carbon steel bolts less hard, yet also widely used.
Corrosion Resistance
Carbon steel bolts are not rust-resistant, yet thanks to a zinc coat or other elements , they can be protected from corrosion.
There are some thread types, in which carbon steel bolts are produced. For example, in terms of threads, these can be coarse threads and fine threads. It is possible to suggest that coarse threads are used in general applications, meanwhile, fine threads are used in precision assemblies . Another important aspect of using carbon steel bolts is proper installation techniques. In order to ensure reliability and safety, one has to follow the correct torque specifications, use thread lubricants, which help to decrease the friction, and also put the bolts in a controlled sequence of tightening to ensure load and pressure distribution . It can be also necessary to mention the maintenance requirements. In some cases, carbon steel bolts must be replaced or cleaned in order to prevent corrosion, which can affect the fastening quality. Moreover, one has to follow the regulations concerning the environmental aspects of using carbon steel bolts. In fact, steel production is an energy-extensive process, so these types of supplies are not the best options in terms of ecological footprint. On the other hand, their durability, recyclability, and vast availability make them moderately positive in terms of environmental impact if compared to some other alloyed fasteners . It is also important to underline that carbon steel bolts can be used with a structural steel. This is why they are largely used in building, construction, and infrastructure applications. They are suitable for use in steel-framed buildings or reinforced concrete structures in civil engineering. In other words, steel bolts can be connected through welding and bolting to steel rebars and rolled beams. Finally, one cannot forget that some standards and specifications must be followed if carbon steel bolts are used for purposes of steel connections. For example, ASTM A307 and A325 are the main standards in this area.
Safety considerations:It is essential that carbon steel bolts be handled and installed properly to avoid accidents and assure the safety of personnel and equipment. This includes following proper safety procedures involved in lifting and carrying heavy loads, ensuring personal protective equipment is used when necessary, and abiding by industry standards in connection to bolted joints.
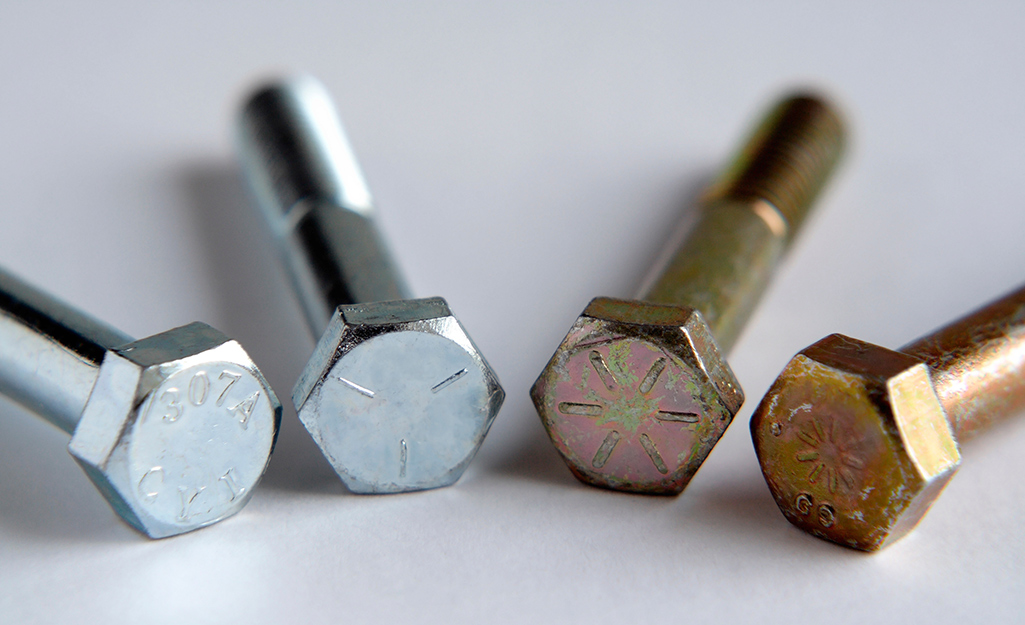
Grades of Bolts – The Home Depot
Aluminum Alloy Bolts
Aluminum alloy bolts are lightweight fasteners made from aluminum or its alloying elements such as magnesium and silicon. They are used in various industries for joining components or structures, especially in the aerospace, automotive, and marine industries. These types of bolts are chosen for their low density, corrosion resistance, and high strength-to-weight ratio. Properties. undisputedly the determining properties of aluminum alloy bolts are:
-
Low density: Aluminum alloy bolts have low density and typically weigh from 2.5 to 2.9 grams per cubic centimeter . It is about three times lower than that of steel and especially useful in applications where weight reduction is a critical factor, such as aircraft and lightweight structures.
-
Corrosion-resistant: the most important advantage of aluminum alloy bolts is their exceptional corrosion resistance, especially in marine and humid environments. The aluminum surface forms a protective oxide layer, which prevents corrosion and ensures long-term durability even in aggressive environments.
-
High strength-to-weight ratio: even though aluminum alloy bolts have a low mass, they have high tensile strength. The tensile strength may vary from 30,000 to 70,000 pounds per square inch psi , depending on the alloy composition and heat treatment. Such a high strength-to-weight ratio allows designing lightweight structures, while maintaining their strength and durability.
-
Non-magnetic properties aluminum alloy bolts are non-magnetic and do not react to magnetic fields. They are especially useful in highly sensitive electronic equipment, or they cause interference in MRI equipment in its operation. Moreover, their non-magnetic nature allows for easier sorting and handling during the bolt manufacturing, installation, or removal.
Thermal conductivity: aluminum alloy bolts have a high level of thermal conductivity and are particularly useful in thermal management applications to provide effective heat dissipation.
-
Anodizing for protection: surface treatments such as anodizing can increase the corrosion resistance and durability of aluminum alloy bolts. Anodizing includes immersing the part in an electrolytic solution and applying an electric current that will make a thick oxide layer on the surface of the part. The oxide surface will increase wear and abrasion resistance, and improve the corrosion seal of the surface of the bolt.
-
Compatibility with composites: Aluminum alloy bolts are compatible with the composite materials, which are highly used in the aviation and automotive industries. These make the aluminum bolts lightweight and non-corrosive. Using aluminum bolts for fastening the composite panels and other pieces makes the overall weight and fuel usage of these items lower.
-
Joining to other materials: joining the alloy bolt to other materials can be done in the following ways: cold forming, adhesive bonding, or mechanical fastening with threaded inserts. These joining methods will make strong connections without the threat of galvanic corrosion, or damaging the surface of the aluminum bolt, for example.
-
Limitations: aluminum alloy bolts have limitations compared to all other types of bolts in high temperature. The relatively low melting temperature of aluminum about 660 degrees Celsius for pure aluminum alloys can limit the usage of aluminum bolts in some applications that include high temperature environments. The way this fact is overcome is by using high temperature alloys or using other methods to bolt two materials together.
-
Surface protection in harsh environment: in some extreme cases, in corrosive or abrasive environments, some more surface protection techniques may be required to increase the longevity of aluminum alloy bolts. Coatings or sealant layers can be chosen , that will provide the aluminum surface an added layer of protection against chemical attacks, UV radiation, or mechanical abrasion.
-
Recycling: aluminum alloy bolts are highly recyclable and eco-friendly material. It is the responsibility of each industry to make the more eco-friendly choices for manufacturing items. Aluminum recycling requires much less energy than the primary production of the aluminum in the first place, thus, it is also a cost-effective method for reducing pollution of the air and the soil.
Types of materials used: Aluminum alloy bolts are manufactured from stamped and extruded aluminum, which provides excellent corrosion resistance and helps reduce the weight of installations and equipment. In general, the material is compliant and can withstand harsh environmental conditions.